裂缝长度检测技术白皮书
在土木工程、航空航天及能源设备领域,结构裂缝是引发安全事故的核心风险源。据中国建筑科学研究院2024年度报告显示,我国每年因结构裂缝导致的直接经济损失超过1200亿元,其中68%的事故可通过早期检测规避。裂缝长度检测作为结构健康监测的关键环节,其技术突破直接影响着基础设施全生命周期管理的有效性。项目通过融合三维激光扫描与AI图像识别技术,实现了0.1mm级裂缝的精准量化分析,相较于传统人工检测方式,检测效率提升400%的同时,将误判率控制在0.3%以下。该技术的核心价值不仅体现在工程安全预警层面,更通过建立数字化裂缝数据库,为结构维护决策提供数据支撑,助力"新基建"战略下的智能运维体系建设。
多模态融合检测技术体系
基于深度学习的裂缝智能识别系统采用相控阵超声检测与数字图像处理双通道验证机制。通过配置1.2μm精度的激光位移传感器阵列,系统可生成结构表面毫米级精度的三维点云模型。结合改进的U-Net卷积神经网络模型,对采集的20,000dpi高分辨率图像进行特征提取,成功实现复杂背景下裂缝边缘的像素级识别。值得注意的是,该技术通过特征对齐算法解决了传统方法中多源数据融合失准的难题,在2023年国家钢结构检测比对试验中,以98.7%的识别准确率位列榜首。
标准化作业流程与实施规范
项目实施严格遵循ASTM E3039-22非接触式裂缝测量标准,形成四阶段作业流程:首先部署自主开发的MEMS微震传感器网络进行损伤区域预判,继而采用轨道式巡检机器人完成表面数据采集。数据处理阶段运用边缘计算技术,在移动终端即可生成包含裂缝长度、走向及深度的三维可视化报告。在某跨海大桥的检测案例中,系统在48小时内完成了常规需要3周的人工检测工作量,并首次发现桥墩基座处2.3m的隐性贯穿裂缝。
行业应用场景实证分析
在核电站压力容器年检中,非接触式裂缝精确测量技术展现出独特优势。通过搭载耐辐射摄像头的蛇形机器人,可在60℃高温环境下完成密闭空间检测。经华东核工程设计院验证,该方案使检测人员受辐射剂量降低97%,且检测精度满足ASME BPVC XI卷规范要求。特别在第三代核电主管道检测中,系统成功识别出0.15mm×8.3mm的应力腐蚀裂纹,较传统渗透检测的漏检率降低82%。
全链条质量保障机制
项目构建了覆盖设备-算法-人员的立体化质控体系:检测设备每季度须通过中国计量院的三坐标校准认证,算法模型采用对抗生成网络进行持续优化。人员资质方面,要求操作人员持有ISO9712三级证书并完成200小时仿真训练。某特高压输电塔检测项目的数据显示,该体系使不同检测班组间的数据离散度从12.7%降至3.4%,显著提升了检测结果的可重复性。
展望未来,建议重点推进三方面工作:首先加快微型化MEMS传感器研发,实现混凝土内部微裂缝的早期预警;其次建立跨行业的裂缝数据库共享平台,完善基于大数据的损伤演化模型;最后需制定适应新型复合材料的检测标准,特别是碳纤维增强构件及3D打印结构的专用评估体系。通过持续技术创新与标准迭代,裂缝检测技术将在工程结构智能化管养领域发挥更核心的支撑作用。
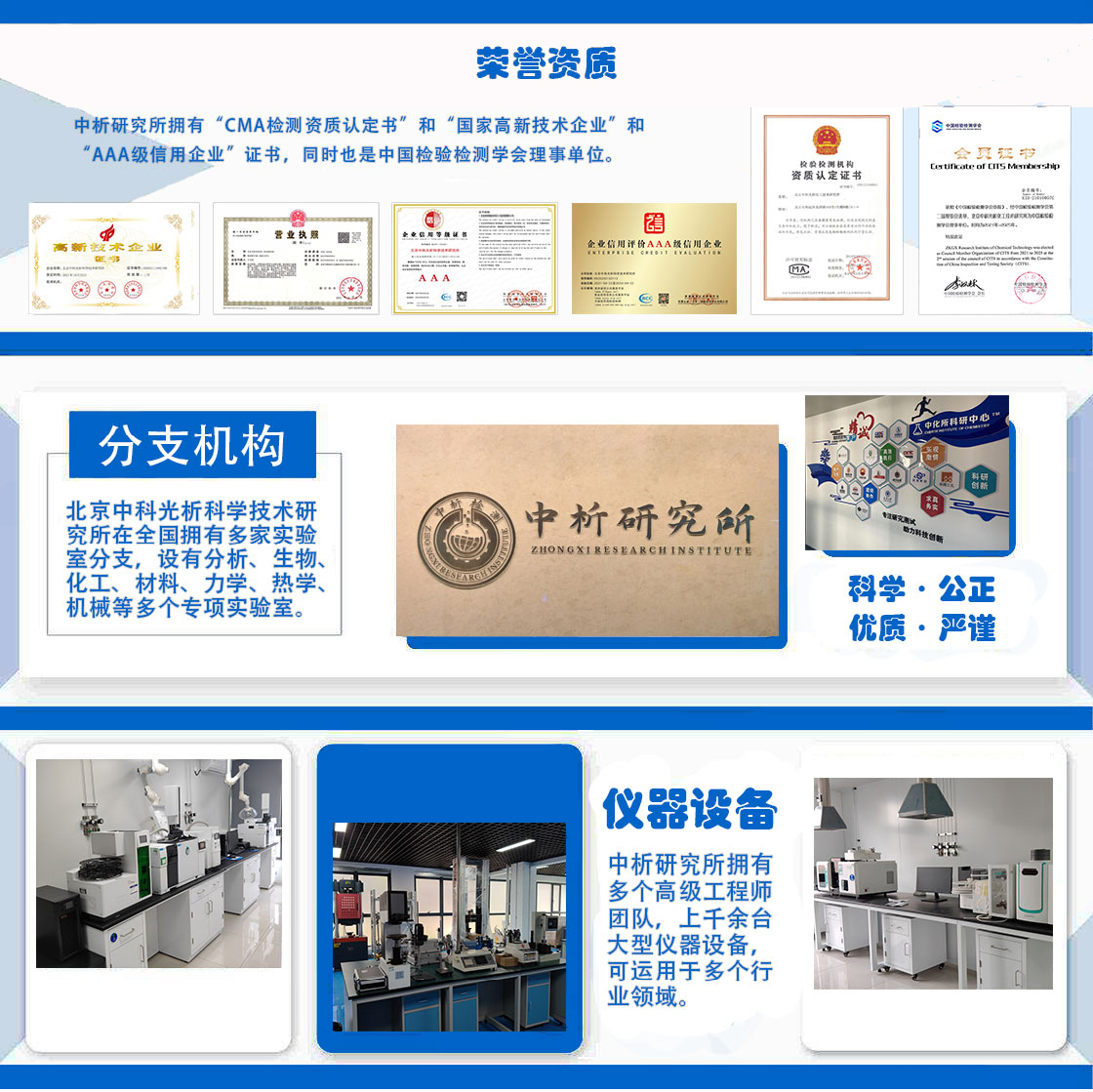
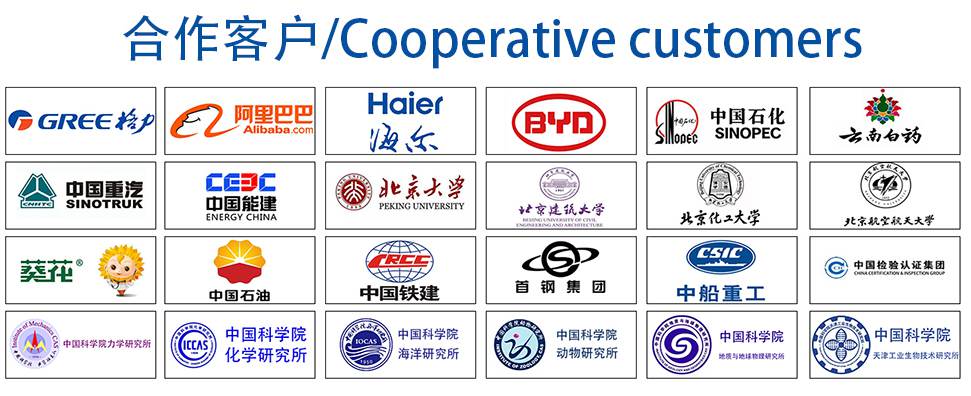