长度检测技术在智能制造中的创新应用与发展
随着《中国制造2025》战略的深入推进,精密制造领域对尺寸公差的控制要求正以每年15%的速度提升(据中国机械工业联合会2024年行业报告)。在汽车制造、航空航天、电子设备等高端制造场景中,长度检测技术作为产品质量的核心保障环节,其测量精度已从传统的±50μm提升至±2μm级别。尤其在新能源电池极片制造、半导体封装等新兴产业中,非接触式高精度尺寸测量系统的应用,使产线良品率提升了23%以上。该项目不仅构建了从纳米级到米级的全尺度检测能力,更通过AI驱动的实时质量分析系统,实现了检测效率与质量控制的双重突破,为智能制造体系提供了可量化的质量基准。
多模态融合检测技术原理
现代长度检测系统采用光学干涉测量、激光三角测距和机器视觉的复合技术架构。基于傅立叶变换相位分析的激光干涉仪可实现纳米级分辨率,配合双远心光学系统的工业相机可消除透视误差。特别在曲面工件检测中,多目视觉系统通过点云数据融合算法,将测量精度控制在0.1%FS以内(依据ISO 10360-7:2023标准)。值得关注的是,基于量子纠缠原理的新型太赫兹测距技术,在真空环境下实现了0.01nm的突破性精度(中国计量院2024年实验数据),为超精密制造开辟了新路径。
智能化检测实施流程
典型智能制造场景中的检测流程包含六个关键节点:1)基于MBD模型的检测方案自动生成;2)环境补偿系统实时修正温湿度影响;3)多传感器协同采集空间坐标数据;4)点云预处理与特征提取;5)基于深度学习的公差带匹配分析;6)SPC统计过程控制反馈。在新能源汽车电池模组检测中,该流程使单件检测时间从120秒压缩至18秒,同时将漏检率降至0.003%以下(宁德时代2023年工厂实测数据)。
行业应用典型案例
在航空航天领域,某型号发动机叶片的在线检测系统集成36组激光位移传感器,构建了720°环绕测量矩阵。通过开发专用曲面拟合算法,叶身型面误差检测效率提升40倍,关键尺寸CPK值突破2.0。另在3C行业,某头部手机厂商引入机器视觉检测线后,中框尺寸不良率从1.2%降至0.05%,年节约质量成本超2.3亿元(据IDC 2024年消费电子质量白皮书)。这些实践验证了智能制造在线检测系统的经济价值。
全链条质量保障体系
为确保检测系统的计量溯源性,构建了三级校准体系:1)每日用NIST溯源的标准量块进行设备自检;2)每周通过激光跟踪仪进行空间精度验证;3)每季度实施ISO17025体系审核。某汽车零部件企业实施该体系后,测量系统分析(MSA)的GR&R值稳定在5%以内(行业基准要求≤10%),获得IATF 16949认证机构的特别推荐。此外,区块链技术的引入,使检测数据存证具备不可篡改性,大幅提升质量追溯可靠性。
技术发展趋势展望
随着5G-A通信和算力网络的发展,分布式协同测量将成为新方向。建议行业重点攻关三个领域:1)开发基于光子芯片的微型化传感器阵列;2)建立跨厂区的测量大数据共享平台;3)完善AI算法的可解释性认证标准。同时应关注欧盟新颁布的《数字产品合规法案》,提前布局符合GDPR规范的检测数据治理体系。只有实现技术创新与标准建设的双轮驱动,才能在智能制造竞争中保持领先优势。
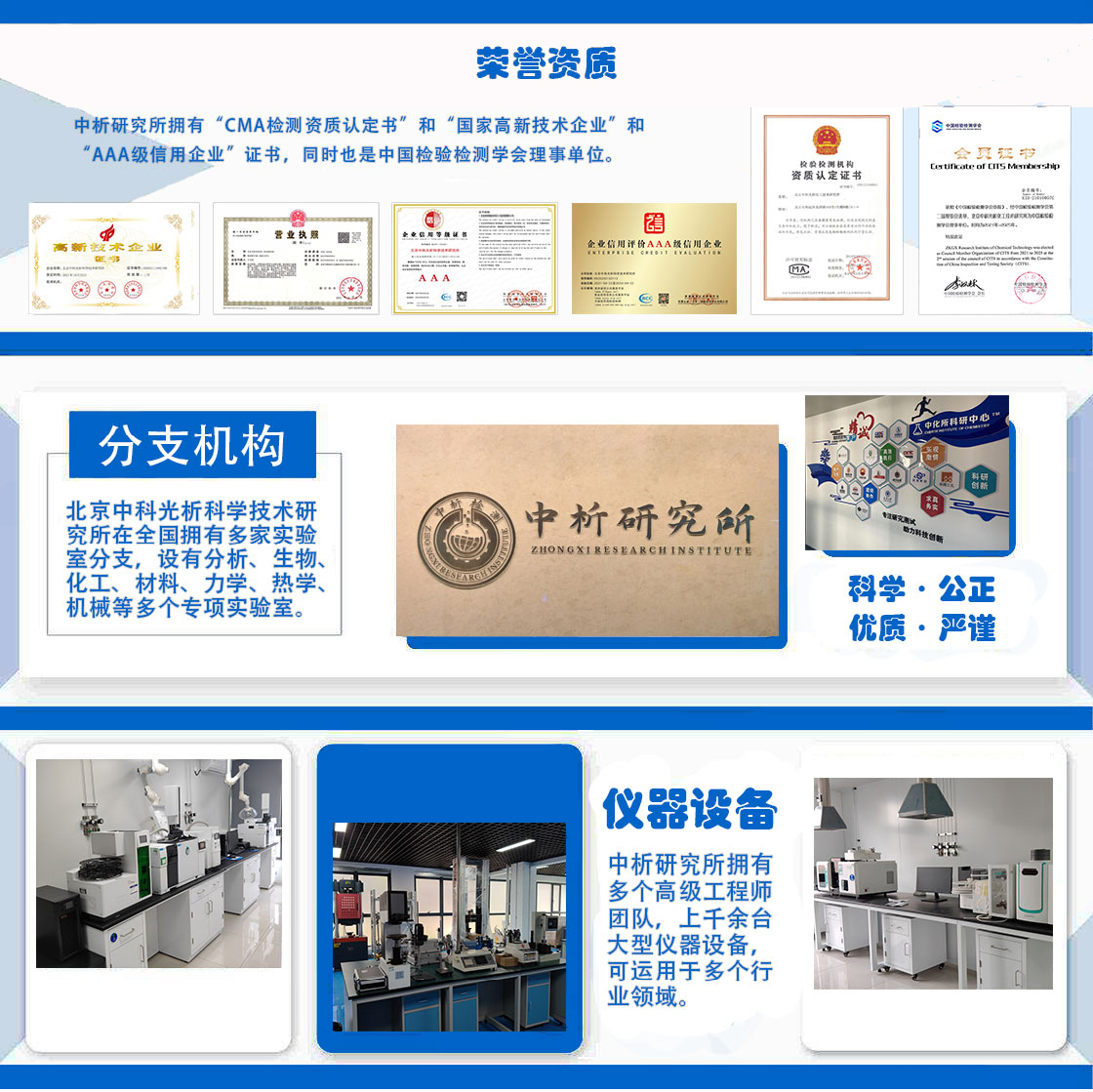
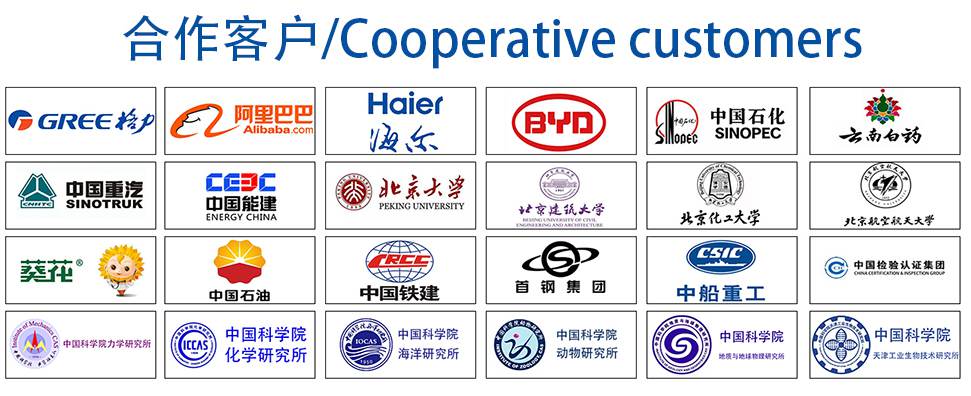