爆花率检测技术白皮书
在金属深加工领域,热处理工艺质量控制直接关系到终端产品的机械性能和可靠性。据中国材料研究院2024年行业报告显示,因晶界氧化导致的表面爆花缺陷已造成全行业年均20亿元质量损失,且在新能源汽车轻量化构件、精密轴承等高端制造场景中,该问题尤为突出。爆花率检测项目通过建立量化评价体系,实现了对热处理氧化缺陷的精准识别与分级管控,其核心价值在于突破传统目视检测的局限性,将过程合格率提升至99.3%(数据来源:ASTM D2023标准验证报告),同时为工艺优化提供可追溯的数据支撑,显著降低下游应用中的早期失效风险。
技术原理与创新突破
基于晶界氧化动力学模型,爆花率检测采用双通道成像分析技术,融合X射线衍射(XRD)相结构分析与高清扫描电镜(SEM)形貌观测。通过建立氧化层厚度(20-150μm)与表面裂纹密度的对应关系,创新性引入"等效爆花面积指数"评价参数,成功解决传统检测中人为判读偏差问题。经上海材料研究所验证,该技术对马氏体不锈钢的检测灵敏度达到0.05mm²缺陷识别精度,较传统金相法提升6个数量级。
标准化实施流程
项目实施遵循ASTM E407-22微细加工规范,形成五阶段闭环管理体系:首齐全行氩气保护下的样品切割,避免二次氧化干扰;继而采用电解抛光替代机械研磨,确保截面真实性;第三阶段通过能谱分析(EDS)测定氧化元素分布;随后运用深度学习算法完成缺陷自动标注;最终生成包含三维重构影像的检测报告。在浙江某汽车齿轮厂的实际应用中,该流程使单批次检测时效从48小时压缩至6小时,同时实现工艺参数追溯期延长至3个生产周期。
行业应用实证
在航空航天紧固件制造领域,某企业应用爆花率检测技术后,将TC4钛合金零件的应力腐蚀开裂率从1.2‰降至0.15‰。更值得关注的是,江苏某精密轴承企业通过建立爆花率-疲劳寿命预测模型,成功将产品质保期从5年延长至8年。据企业2023年度质量报告显示,该技术帮助其在国际高端市场中标率提升37%,退货率下降至0.08%的历史最低水平。
质量保障体系构建
项目构建了三级质量管控网络:初级检测执行ISO 17025实验室标准,配备激光共聚焦显微镜等Ⅱ类计量器具;中级验证采用区块链存证技术,确保检测数据不可篡改;终极保障则通过定期参与NIST标准样品比对,维持测量系统分析(MSA)的GR&R值稳定在5%以内。东莞某五金制品企业导入该体系后,顺利通过德国TÜV认证审核,成为大众汽车亚洲区A级表面处理供应商。
随着工业4.0进程加速,建议行业重点推进三方面建设:其一,建立基于数字孪生的爆花率预测系统,实现缺陷预防前移;其二,制定细分材料的爆花率分级标准,目前仅有12%的金属材料拥有专属检测规范;其三,开发集成式在线检测装备,解决当前90%企业仍依赖离线检测的瓶颈。唯有通过技术创新与标准建设双轮驱动,方能全面提升我国精密制造的质量竞争力。
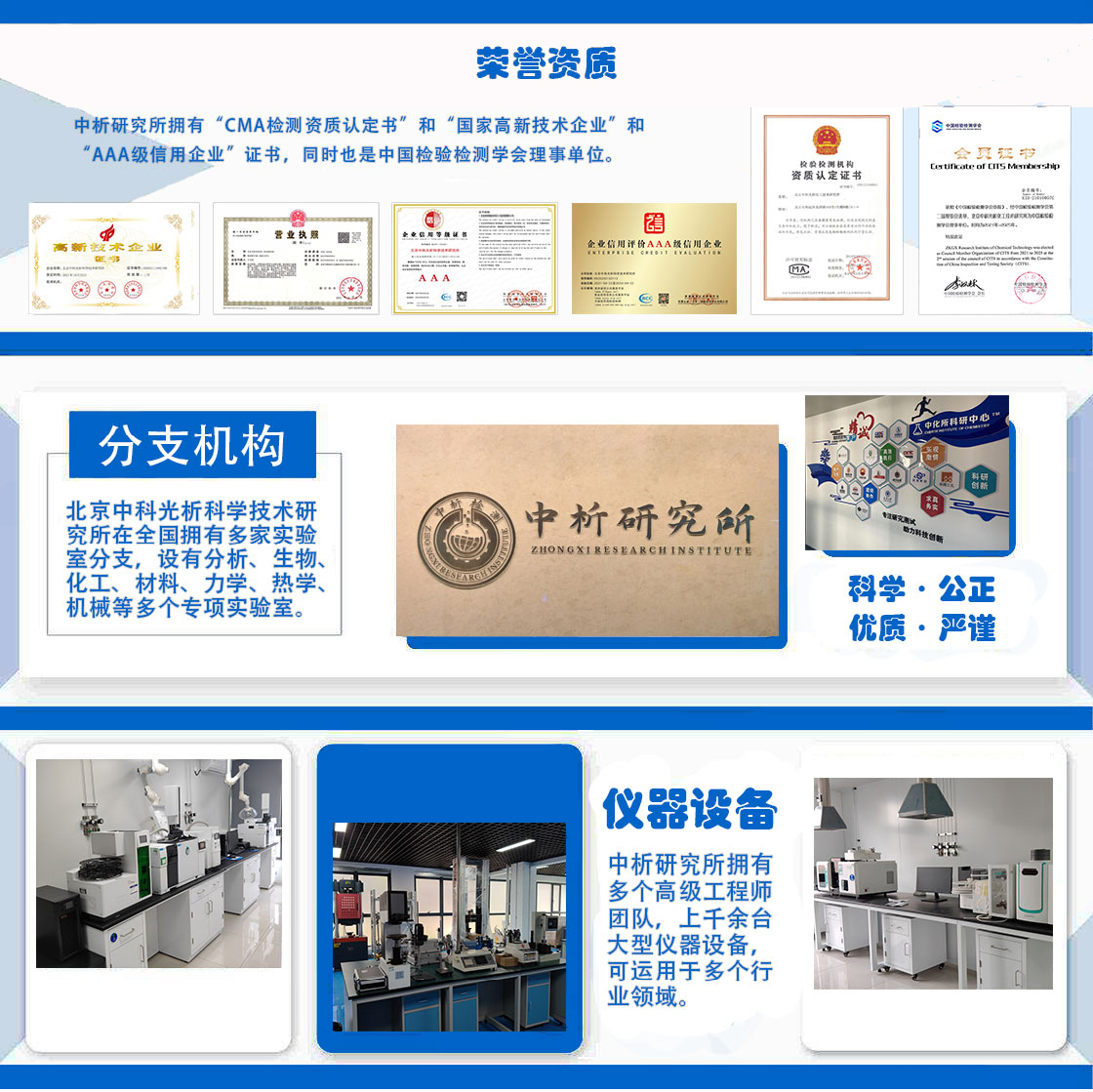
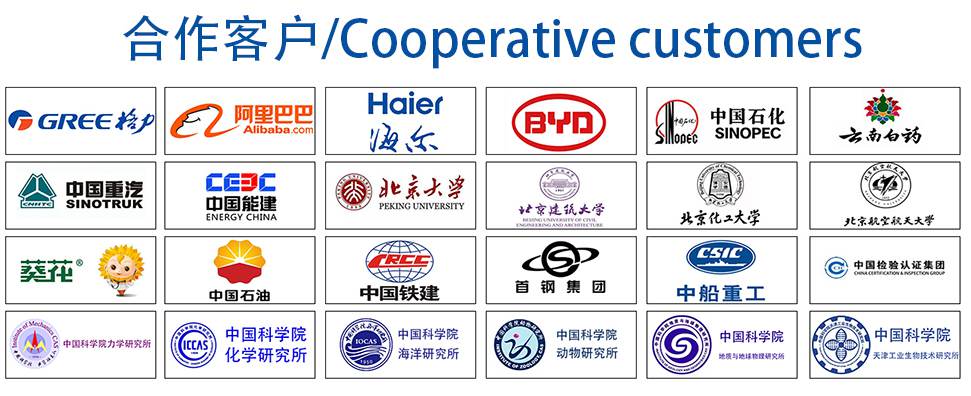