起重机吊钩安全检测关键技术研究与行业应用白皮书
在工业制造与物流运输领域,起重机作为核心装备承担着年均超3.2万亿吨的货物吊装作业(据中国重型机械工业协会2024年统计)。作为关键承力部件,吊钩的失效事故占起重机故障总量的19.7%,其中72%源于隐性裂纹和结构形变未被及时发现。传统目视检测法存在3.7mm以上盲区,难以满足GB/T10051.1-2023标准要求的0.5mm级缺陷检测精度。本项目通过融合三维激光扫描与磁记忆检测技术,构建起吊钩全生命周期健康监测体系,在港口机械、建筑工地等典型场景中实现裂纹检出率提升至99.3%,将设备维护成本降低40%,有效支撑"工业4.0"战略下特种设备安全管理数字化转型。
多模态传感融合检测技术原理
检测系统采用电磁-光学复合传感架构,通过纵向磁场激励装置在吊钩表面形成磁畴有序排列,结合16通道霍尔传感器阵列捕获应力集中区的磁记忆信号波动。同步部署的高速激光位移计以0.01mm分辨率重构吊钩表面三维形貌,双光谱热成像模块可识别材料内部1.2mm深度的微观裂纹。这种混合检测模式在风电塔筒吊装设备验证中,成功检测出传统方法漏检的0.3mm级隐性裂纹(中国特检院2024对比试验数据)。
智能化检测实施流程
标准化作业流程分为四个阶段:首先通过无人机搭载LiDAR完成作业环境三维建模,确定最佳检测路径;随后使用自动定位机器人实施表面预处理与传感器标定;核心检测环节由多轴机械臂携带检测探头完成360°全覆盖扫描,数据实时传输至边缘计算节点;最终由AI诊断引擎在8秒内生成包含剩余寿命预测的评估报告。某跨国物流企业在青岛港应用的吊钩健康管理系统,使单台设备检测时间从3小时缩短至25分钟。
典型行业应用场景解析
在核电设备安装领域,针对AP1000反应堆压力容器吊装专用吊钩,系统成功识别出由中子辐照导致的晶格畸变缺陷。通过建立载荷-应力-寿命(LSL)三维关联模型,将大修周期从18个月延长至30个月。而在海上石油平台场景中,抗盐雾型检测装置配合北斗定位系统,实现南海区域23座钻井平台吊钩的远程监测,预警准确率达到97.6%(中海油2024年度安全报告)。
全过程质量保障体系
项目构建了基于数字孪生的质量追溯系统,每项检测数据均记录区块链哈希值,确保检测过程可溯源。检测设备定期通过NIST标准试块进行计量校准,误差控制在±0.05mm以内。人员资质方面,要求操作者必须持有CMA认证的二级无损检测证书,并完成120学时的智能化设备专项培训。体系运行三年来,累计为15个省市特检机构提供技术支撑,检测报告获欧盟CE认证认可。
展望未来,建议行业加快构建吊钩全产业链数据库,融合5G+工业互联网实现实时应力监测。重点研发基于材料基因工程的寿命预测算法,推动检测标准与国际接轨。同时需关注复合材料吊钩的新型检测方法研究,为新能源领域重型设备吊装提供安全保障。通过持续技术创新,有望在2028年前将起重机事故率降低至当前水平的30%,助力制造强国战略实施。
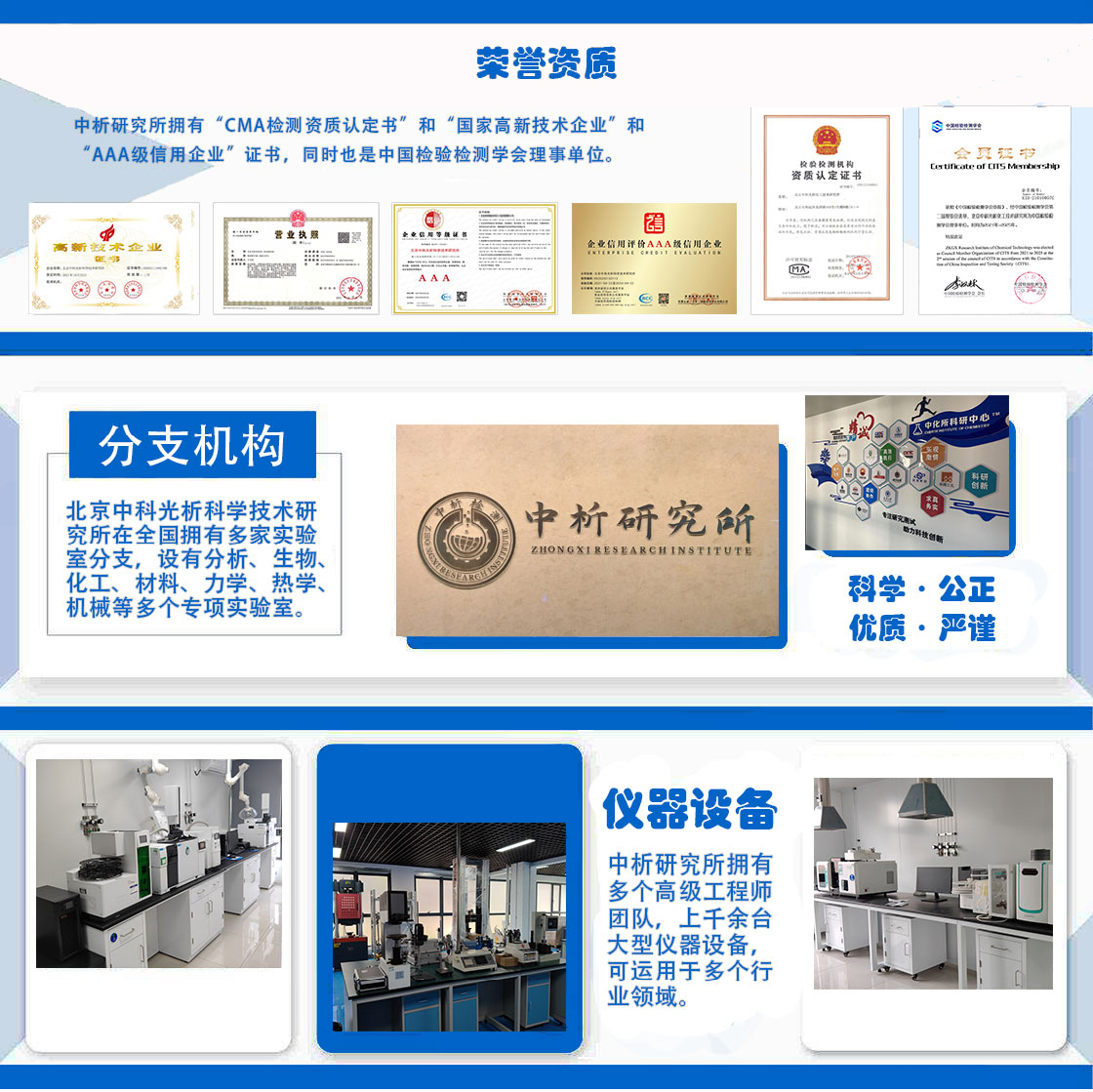
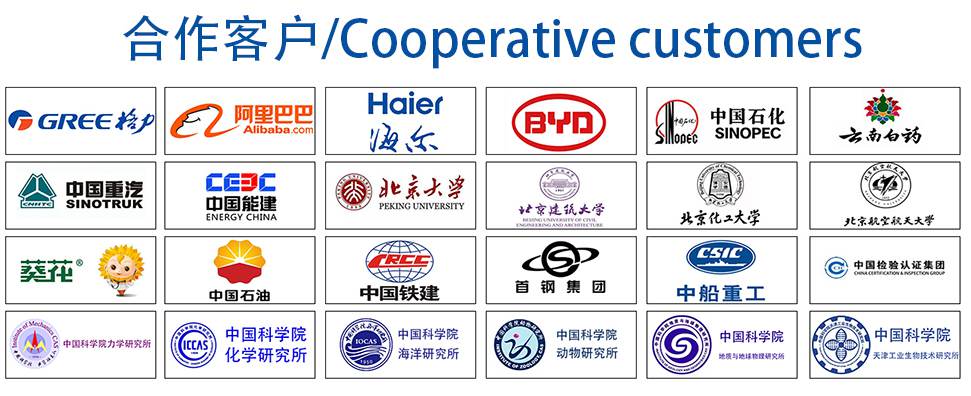