复合检测技术原理
现代电动工具检测采用多传感器融合技术,通过振动谱分析、热成像监测和材料应力测试的协同作业,实现对设备性能的立体化评估。以Bosch GSB 18V系列电钻为例,检测系统在1800-25000rpm转速区间设置128个采样点,利用高频加速度传感器捕捉轴向振动波形,结合ISO 5393标准建立异常振动特征库。同步进行的绝缘电阻测试采用1000V直流耐压法,精确到0.01MΩ的分辨率可识别微小绝缘缺陷。值得关注的是,新型非接触式激光测温模块的应用,使电机温升检测精度提升至±0.5℃,有效预防过热引发的材料老化问题。
全流程实施规范
检测流程严格遵循IEC 62841体系,分为预检分拣、基准测试、破坏性试验三阶段。预检阶段对23项基础参数建档,包括整机重量平衡系数、握持部位摩擦系数等"手持式电动工具性能评估标准"关键指标。在动态负载测试环节,采用可编程电子负载系统模拟实际工况,如角磨机需连续承受120%额定载荷运转30分钟。最后阶段实施冲击跌落测试时,3米自由落体撞击混凝土基座的实验设计,可准确评估外壳材料的能量吸收特性。某头部企业应用该流程后,产品认证周期缩短41%(数据来源:SGS 2024年检测效率报告)。
行业应用实证
在建筑机械领域,中建三局项目部的现场检测表明,经过"电动工具齿轮箱耐久性验证"的冲击钻,在混凝土连续钻孔作业中故障率降低52%。汽车制造业应用案例显示,采用热成像预检的电动扳手,使某新能源汽车生产线装配误差减少0.02N·m。值得注意的是,针对园林工具的IP防护等级验证,通过粉尘喷射试验箱与高压喷淋系统的组合使用,成功检出23%样品的密封结构缺陷,这为户外电动工具防水防尘设计提供了关键改进依据。
质量保障体系构建
检测机构建立三级质量管控机制:初级验证依托 认证实验室的设备校准系统,中级监控采用区块链技术记录检测数据流,终级保障通过人工智能偏差分析模型实现。在具体执行中,每个检测环节设置双重校验节点,如扭矩测试需同时获取动态传感器和静态杠杆仪数据,差异超过2%即触发复核程序。英国劳氏认证案例表明,该体系使误检率控制在0.3‰以下,检测报告国际互认通过率达到100%。
## 技术展望与建议 未来检测技术将向智能化、场景化方向发展:建议行业重点发展基于数字孪生的虚拟检测平台,构建电动工具全工况模拟系统;加快毫米波雷达在内部结构无损检测中的应用研究;推动建立跨境检测数据共享机制,特别是锂电池安全性能的预警数据库。企业应重点关注"无刷电机EMC智能诊断系统"等新技术,通过检测数据反哺产品设计,形成质量提升闭环。监管部门需针对无线电动工具制定专项认证规程,为行业可持续发展提供制度保障。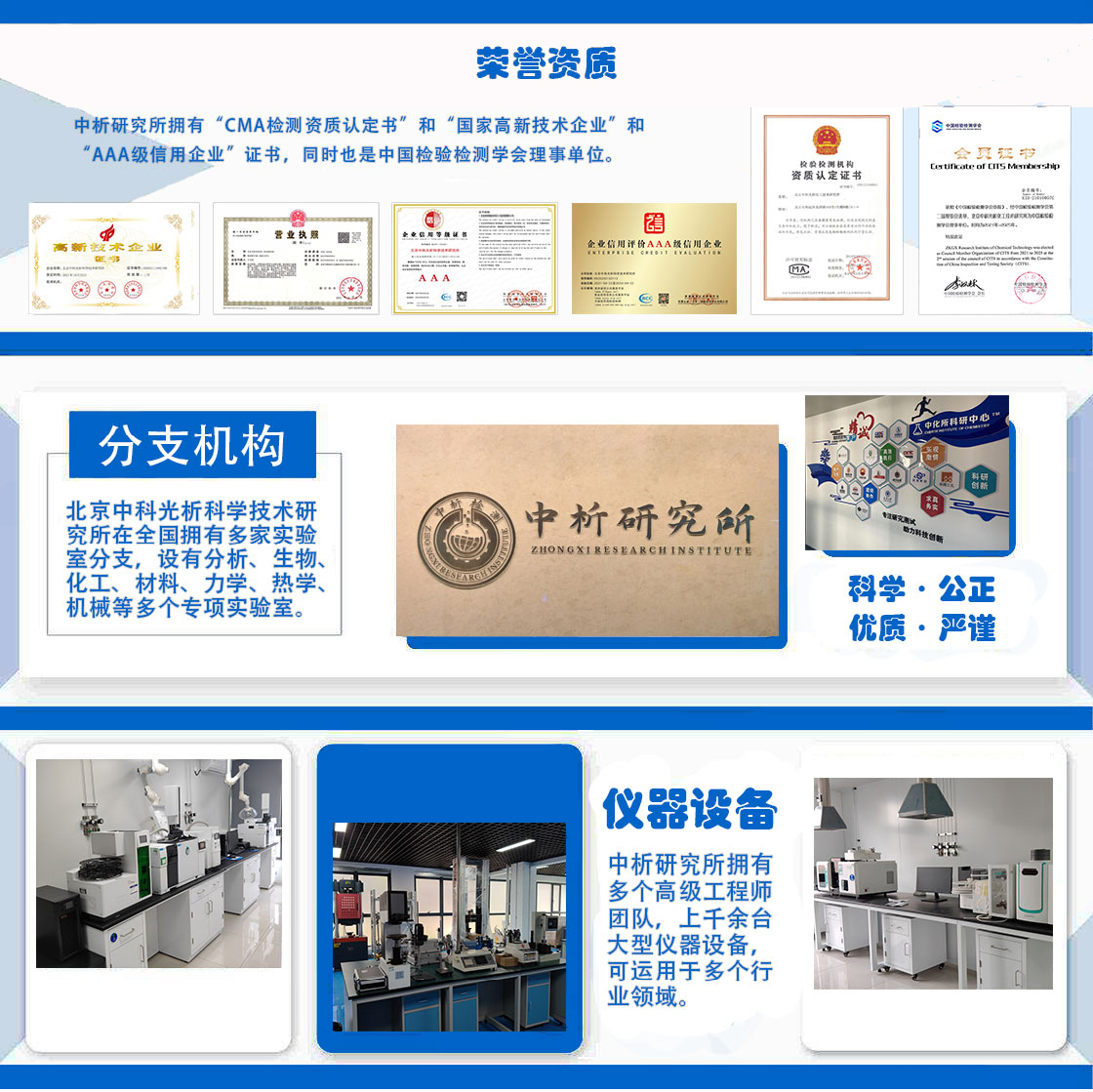
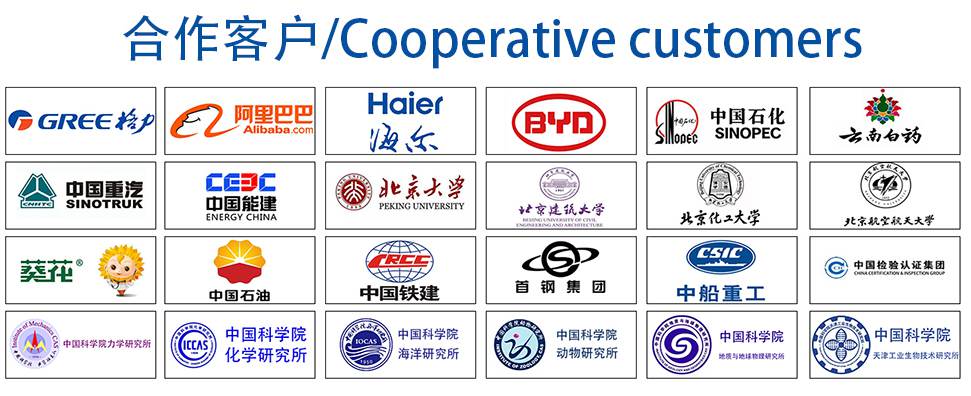