机械采油井系统效率测试检测的重要性与现状
机械采油井系统是油田开发中不可或缺的核心生产单元,其运行效率直接影响原油产量和能源消耗成本。随着油田进入中后期开发阶段,地层能量逐渐下降,机械采油井占比逐年上升,系统效率的优化成为降本增效的关键环节。系统效率测试检测通过量化分析地面设备、井下装置及配套设施的能耗与性能,为优化抽油机参数、调整工作制度提供科学依据。当前,行业普遍采用“输入功率-有效功率”的对比模型,结合动态监测技术,对机械采油系统进行全方位诊断,旨在提升有效功率占比、降低无效能耗。
机械采油井系统效率测试核心检测项目
1. 地面设备效率检测
包括电动机输入功率、功率因数、平衡度及皮带传动效率的测量。采用电能质量分析仪实时记录电机运行参数,结合示功图测试分析抽油机载荷波动对电机效率的影响,重点关注电机负载率是否处于经济区间(70%-90%)。
2. 抽油机传动系统效率检测
针对减速箱、曲柄连杆机构的机械损耗进行检测,通过振动频谱分析和润滑油颗粒监测判断齿轮磨损状态。同步测试皮带滑差率(应≤5%)和曲柄平衡度误差(标准值±2%),确保能量传递路径的高效性。
3. 井下系统效率检测
运用井下传感器与地面示功仪联动测试,获取泵效、充满度、沉没度等关键参数。重点检测柱塞与泵筒配合间隙泄漏量(需<10%)、游动阀与固定阀启闭响应时间(≤0.1秒),并通过动液面测试验证供排协调性。
4. 系统综合能耗分析
构建电力-机械-液压能量转化模型,计算系统综合效率(达标值≥30%)。对比吨液百米耗电量(标准≤0.5kWh)、有效功率占比(≥60%)等指标,识别能耗异常节点。
5. 动态参数实时监测
部署无线载荷传感器、转速传感器和压力变送器,连续采集悬点载荷、冲程冲次、井口回压等动态参数。通过大数据分析建立效率波动预警模型,实现异常工况(如气锁、砂卡)的早期识别。
6. 油井生产参数匹配性检测
验证抽油泵排量与实际产液量的匹配度(合理范围80%-120%),分析冲次与地层供液能力的适应性。采用变频调速装置优化冲次调节精度(±0.1次/分钟),减少无效行程占比。
系统效率测试的流程与优化路径
典型测试流程包括:基础数据采集→设备校准→同步测试(地面+井下)→数据处理→效率计算→问题诊断→优化方案制定。通过建立Δη=η实测-η理论的效率差值分析体系,可针对性实施调平衡、换泵径、改管柱等措施,实现系统效率提升5%-15%的优化目标。
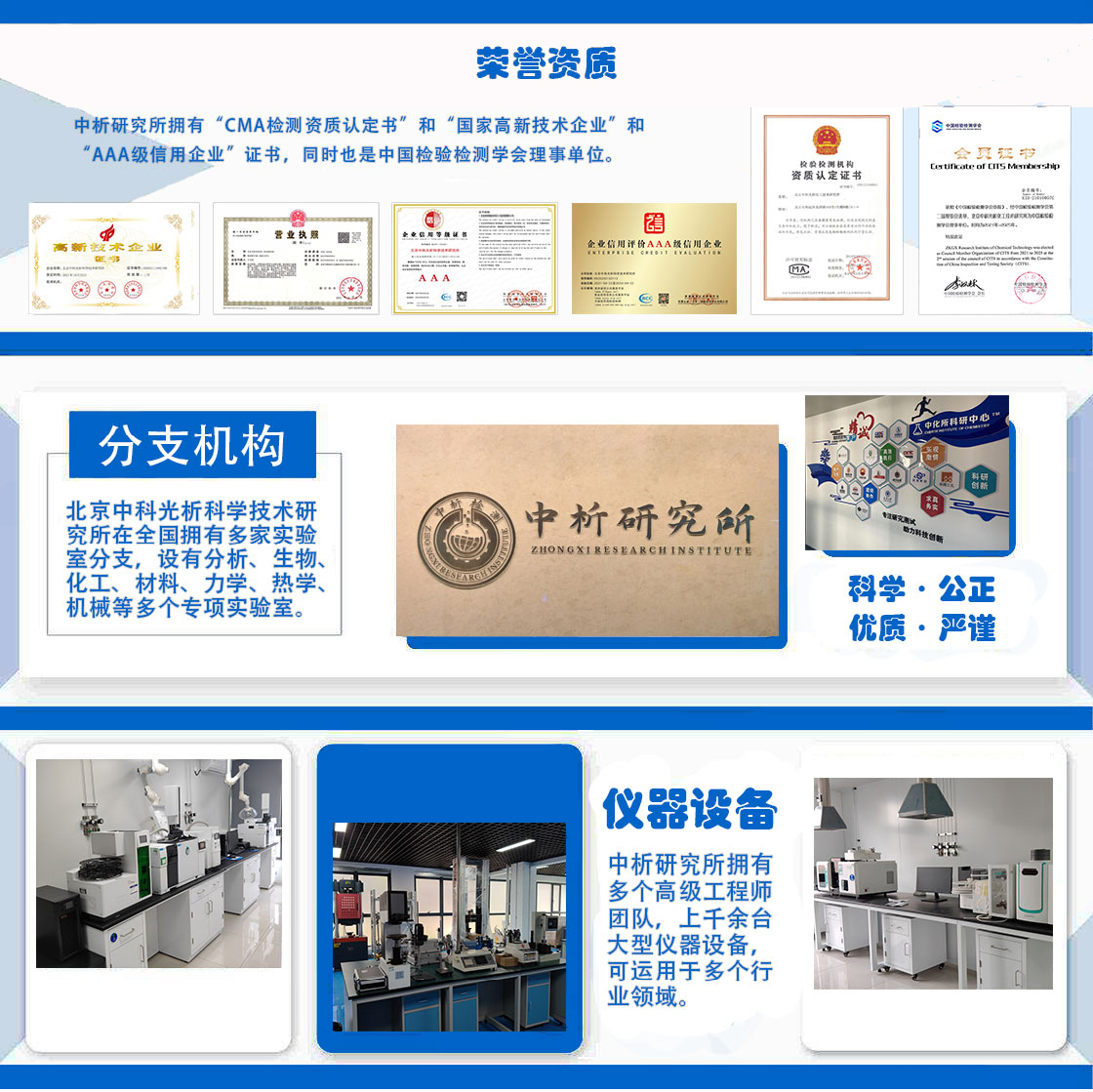
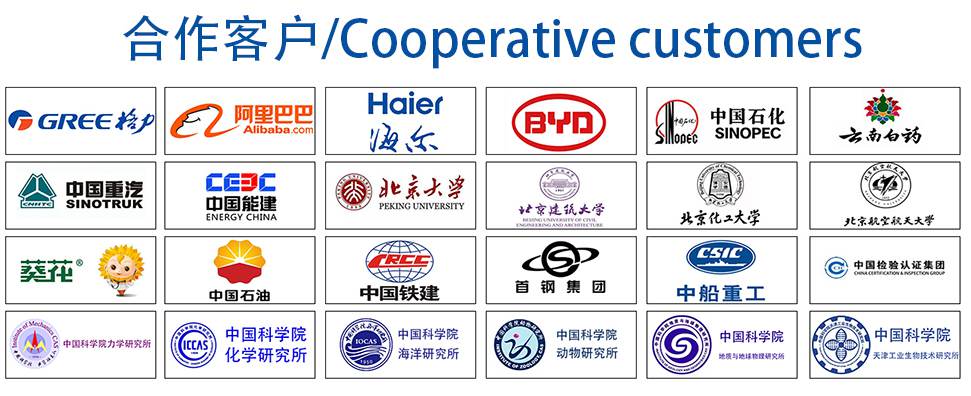