石油工业用加热炉节能监测检测项目解析
石油工业用加热炉作为油气加工、储运环节的核心热能设备,其能源消耗占生产总成本的15%-30%。开展节能监测检测是优化能效、降低碳排放的关键举措。根据GB/T 28750《工业锅炉及火焰加热炉节能监测方法》和SY/T 6381-2016《石油工业用加热炉能效监测规范》,完整的节能监测体系需覆盖设备运行全过程的12项核心指标,通过量化分析为技术改造提供科学依据。
一、主要检测项目与技术要求
1. 热效率检测:采用热平衡法或反平衡法,要求正平衡法测量误差≤±3%。重点监测燃料低位发热量、烟气成分及温度等参数,工业炉热效率基准值需≥85%
2. 排烟温度监测:使用K型热电偶多点测量,温度偏差控制在±5℃内。对于天然气炉,排烟温度应≤180℃;燃油加热炉≤220℃。每升高10℃热损失增加0.5%-0.8%
3. 过剩空气系数测定:采用烟气分析仪检测O₂、CO₂含量,要求燃气炉α=1.05-1.15,燃油炉α=1.10-1.25。当α值超过1.3时,每增加0.1将导致热效率下降1.2%
二、关键辅助检测指标
4. 炉体表面温度场扫描:应用红外热像仪进行全炉体扫描,外壁温度不得超过环境温度+50℃。局部高温区域(>150℃)需标注并进行保温层修复
5. 燃烧器效率测试:包括燃烧完全度(CO浓度<50ppm)、火焰形态(长度/直径比≤3:1)等,确保燃料化学能转化率>98%
6. 燃料消耗量计量:安装涡轮流量计或质量流量计,连续72小时监测数据波动,系统误差应<1.5%。同步记录负荷变化曲线与燃料消耗的匹配度
三、检测实施要点
检测前需确保加热炉连续运行>8小时达到热稳定状态,检测期间负荷波动不超过额定值的±5%。数据采集应覆盖不少于3个完整生产周期,采用Class 1级精度仪器,温度测量点布置需避开涡流区。检测报告需包含设备基本信息、检测条件说明、数据修正计算过程及能效改进建议。
通过系统化的节能监测,石油企业可实现单台加热炉年节能量200-500吨标煤,投资回收期普遍在1-2年内。以某炼厂常压加热炉改造为例,通过优化过剩空气系数(从1.28降至1.12)和修复炉墙保温,热效率提升7.2%,年节约燃料费用超120万元。
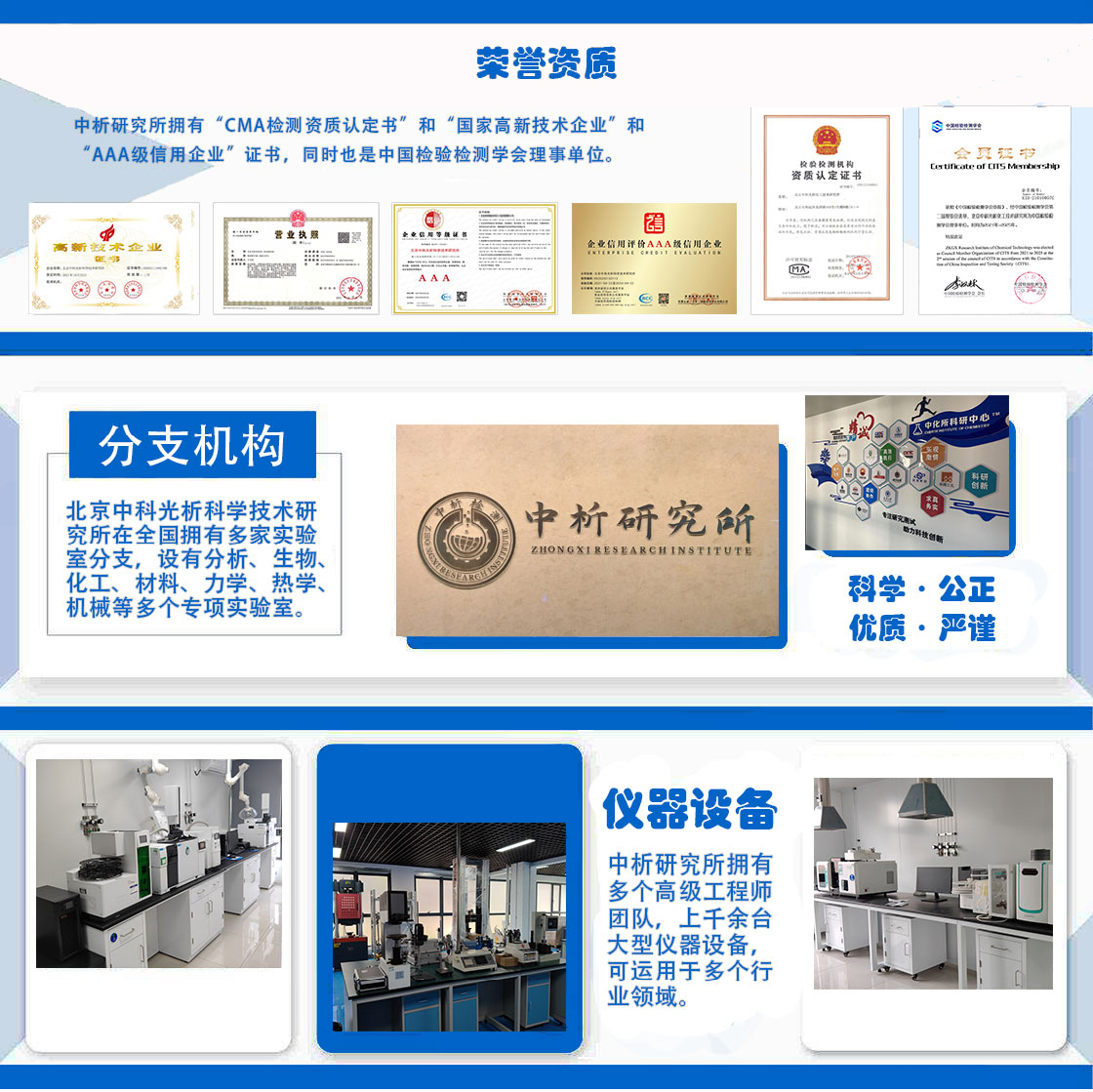
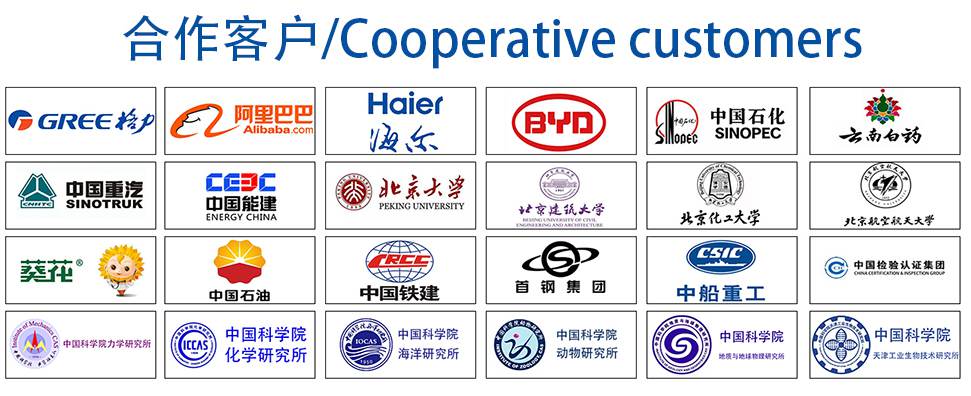