阀门-法兰、螺纹和焊接端检测的重要性
阀门作为工业管道系统中的关键控制元件,其连接端的密封性能、结构强度和可靠性直接影响系统的安全运行。法兰、螺纹和焊接端是阀门与管道连接的主要方式,不同连接形式的应用场景和检测要求差异显著。为确保阀门在高压、高温、腐蚀等复杂工况下的长期稳定性,需对连接端的几何尺寸、表面质量、材料性能等进行系统性检测。这些检测项目不仅需要符合相关国际标准(如ISO、ASME、API等),还需结合实际工况进行针对性验证,以消除泄漏、断裂等潜在风险。
法兰端检测项目
法兰端作为高压力管道的常用连接方式,其检测需重点关注以下项目:
1. 法兰尺寸精度检测:包括法兰外径、内径、厚度、螺栓孔中心距等关键尺寸的测量,确保与配对法兰的兼容性。
2. 密封面质量检测:通过粗糙度仪检测密封面的Ra值,同时检查划痕、凹坑等表面缺陷,保证密封垫片的有效贴合。
3. 螺栓孔同轴度验证:使用三坐标测量仪或专用检具检测螺栓孔的分布圆直径和位置精度,避免安装时对中偏差。
4. 材料硬度与强度测试:通过硬度计和拉伸试验机验证法兰材料的力学性能,确保其满足设计压力等级要求。
螺纹端检测项目
螺纹连接端常见于低压或小型阀门,其检测需注重细节特征:
1. 螺纹参数测量:利用螺纹通止规检测螺距、牙型角、中径等参数,确保与管道螺纹的啮合精度。
2. 螺纹同轴度检测:通过光学投影仪或专用量具验证螺纹轴线与阀门流道的同轴偏差,防止安装应力集中。
3. 表面完整性检查:采用放大镜或内窥镜检查螺纹根部是否存在裂纹、毛刺等缺陷,避免应力腐蚀开裂。
4. 密封剂兼容性测试:评估螺纹密封胶或生料带与介质、温度的适配性,确保长期密封效果。
焊接端检测项目
焊接端常用于高温高压场合,检测需覆盖焊接全流程:
1. 坡口几何检测:测量坡口角度、钝边厚度及坡口清洁度,确保焊接熔深和强度符合标准。
2. 焊接工艺评定:验证焊材匹配性、预热/后热温度控制等工艺参数,通过金相分析检查焊缝微观组织。
3. 无损检测(NDT):采用射线检测(RT)、超声波检测(UT)或磁粉检测(MT)排查焊缝内部缺陷。
4. 焊接残余应力测试:通过X射线衍射法或盲孔法评估应力分布,预防因应力集中导致的变形或开裂。
检测技术与标准应用
现代阀门检测广泛采用数字化技术,如激光扫描用于三维尺寸重建、数字图像处理技术分析密封面纹理等。检测过程中需严格执行API 598(阀门试验与检验)、ASME B16.34(阀门法兰端标准)等规范,并针对核电、LNG等特殊领域补充专项检测要求。通过建立全生命周期的检测数据库,可为阀门运维提供数据支持。
结论
阀门法兰、螺纹和焊接端的检测是保障管道系统可靠性的重要环节。通过多维度的检测项目组合、齐全检测设备应用以及标准化流程控制,可有效识别连接端的设计缺陷、制造偏差和潜在失效风险。不同连接方式的检测策略需结合其结构特点和使用场景动态调整,最终实现阀门在全生命周期内的安全高效运行。
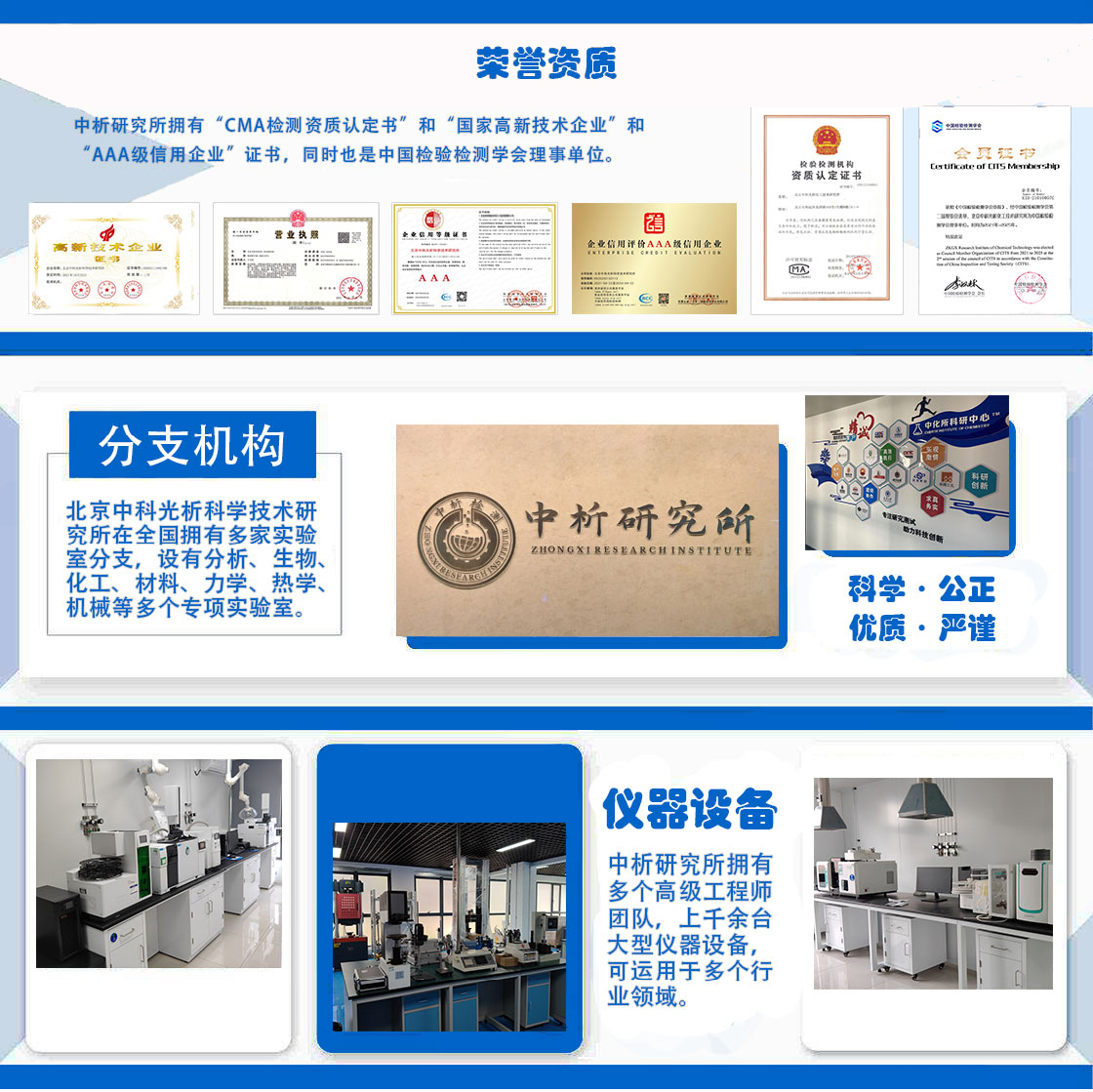
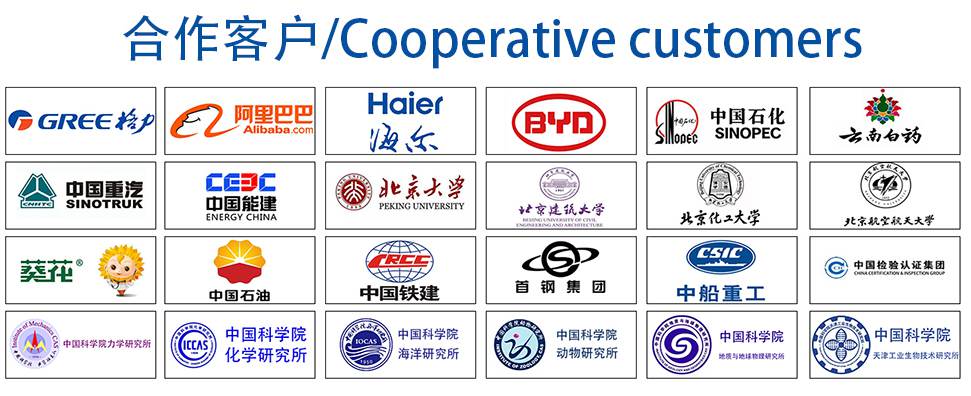