起重滑车检测的重要性与基本流程
起重滑车作为工业吊装作业中不可或缺的机械设备,其安全性和可靠性直接影响工程效率及人员安全。由于长期承受高负荷、频繁启停及复杂工况,滑车关键部件易出现磨损、变形或失效问题。定期检测是保障设备正常运行、预防事故的核心手段,也是国家特种设备安全法规的强制性要求。检测工作需依据GB/T 5972-2016《起重机用钢丝绳检验和报废规范》、ISO 4309《起重机钢丝绳检验和报废实用规范》等标准,通过系统性检查与测试,评估滑车整体性能及安全隐患。
核心检测项目及技术要求
1. 结构部件完整性检测
重点检查滑车本体、吊钩、轮轴等承力部件的裂纹、变形及腐蚀情况。使用磁粉探伤或超声波检测技术排查金属构件的微观缺陷,测量滑车轮槽磨损量是否超出允许公差(通常不超过原尺寸10%)。
2. 润滑系统与轴承状态评估
核查滑轮轴承的润滑油脂填充量及污染程度,使用振动分析仪检测轴承运行时的异常振动频率。轴承径向游隙应控制在0.05-0.15mm范围内,过热(表面温度>80℃)或异响需立即更换。
3. 制动器性能测试
通过动态加载试验验证制动器的响应时间和制动力矩稳定性。标准要求制动器在额定载荷下需在1.5秒内完全抱死,制动力矩应达到额定力矩的1.5倍以上。同时检查制动片磨损量(厚度损耗不超过原设计30%)。
4. 吊钩与滑轮组功能验证
使用三维坐标测量仪检测吊钩开口度变形量(禁止超过原尺寸15%),借助激光对中仪确认滑轮组平面度偏差(≤2mm/m)。进行空载与125%额定载荷试运转,观察滑轮转动灵活性及钢丝绳脱槽风险。
5. 电气控制系统诊断
对遥控装置、限位开关等电气元件进行绝缘电阻测试(≥1MΩ),验证过载保护装置的触发准确性。使用电流钳表检测电机三相电流平衡度(偏差≤10%),确保控制线路无短路或虚接现象。
检测周期与注意事项
常规检测应每季度实施1次全面检查,频繁使用(>200次/月)或高危环境(腐蚀、高温)需缩短至每月1次。检测后需出具包含缺陷定位图、实测数据对比的详细报告,对达到报废标准的部件必须强制更换。特别需注意:严禁在未解除载荷状态下进行维修作业,检测人员应持有特种设备检验资格证并做好个人防护。
智能化检测技术的应用趋势
随着工业物联网的发展,无线应力传感器、热成像仪等设备已实现滑车运行状态的实时监测。通过大数据分析可预测轴承剩余寿命,AI视觉系统能自动识别钢丝绳断丝缺陷,检测效率较传统方式提升60%以上,标志着起重设备检测进入数字化新阶段。
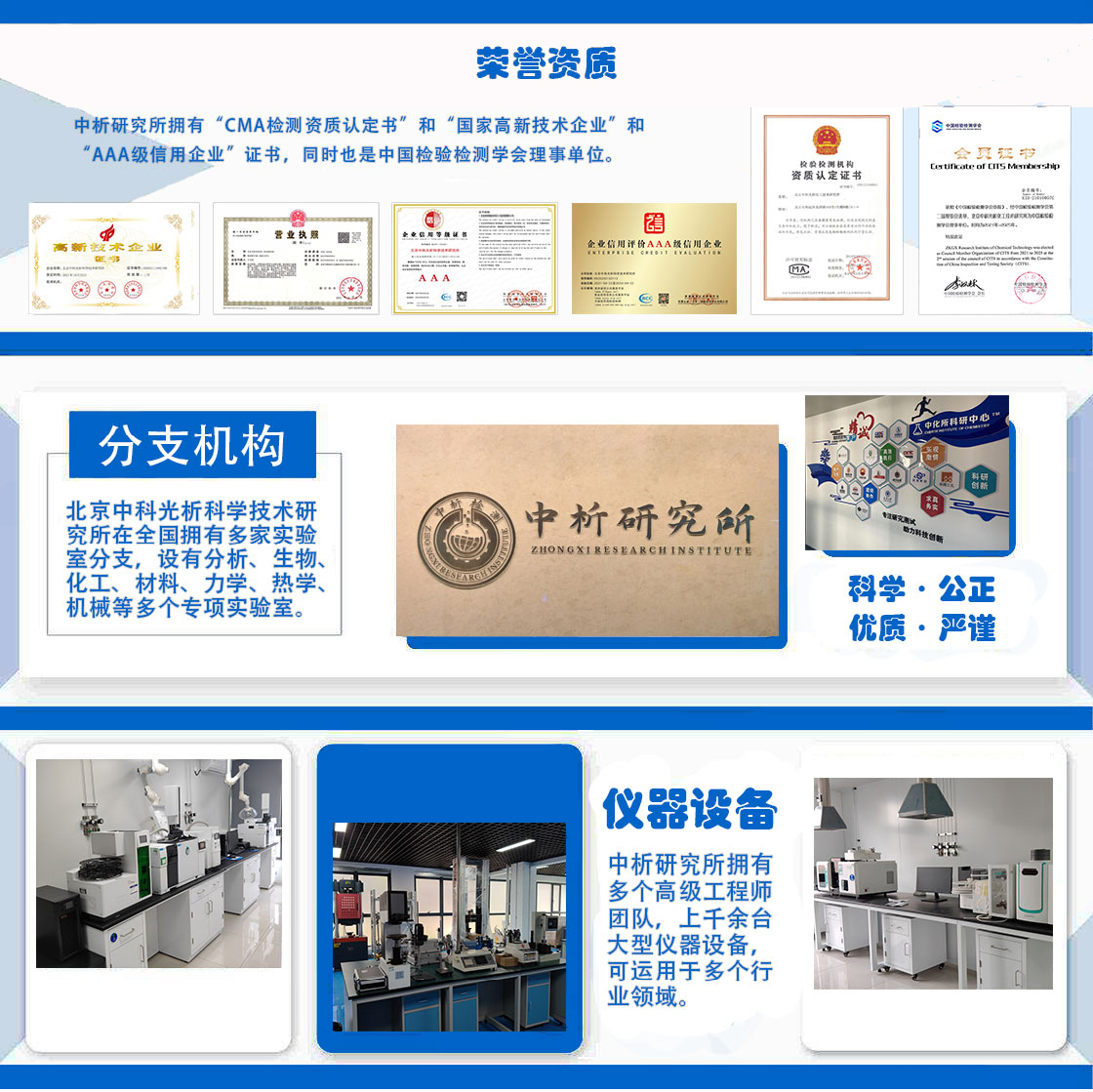
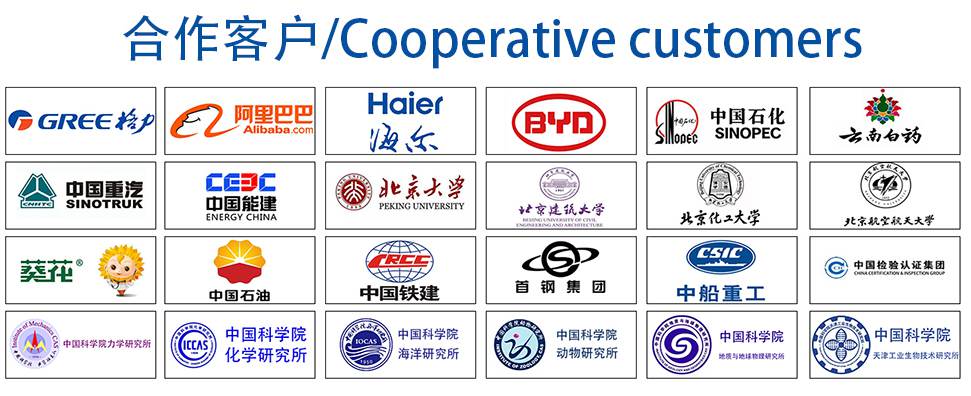