油气田电网线损率检测技术白皮书
在能源转型与"双碳"目标驱动下,油气田电力系统降耗增效已成为行业关键课题。据国际能源署(IEA)2024年能源效率报告显示,油气开采过程电力消耗占运营总成本的23%-35%,其中电网线损率普遍达6.8%-12.5%,显著高于工业电网平均水平。针对油气田地理环境复杂、负荷波动剧烈、设备老化严重的特性,开展专项线损率检测不仅能精准定位能源损耗节点,更可支撑智能化电网改造决策。通过集成高精度传感器网络与大数据分析平台,项目可将线损率降低3-5个百分点,单座中型油气田年节约电费超2000万元,同时减少碳排放量约1.2万吨。这种"技术+管理"双轮驱动的降损模式,正在成为油气行业绿色发展的新范式。
1. 检测技术原理与创新突破
现行检测体系基于分层计量与潮流计算相结合的方法,创新引入分布式光纤测温与谐波分量分析技术。通过部署0.2S级智能电表群组,构建覆盖35kV/10kV/0.4kV多电压等级的计量网络,配合改进型前推回代算法,实现线损分量解耦计算。特别针对油气田特有的冲击性负荷特征,开发了动态权重修正模型,将暂态过程线损计算误差控制在±0.15%以内。该技术已获得国家电网科学研究院认证,在塔里木油田试点中成功识别出17.3%的隐性线损。
2. 标准化实施流程及关键技术
实施流程分为四个阶段:基础数据校核阶段完成计量装置全参数校准与拓扑关系建模;数据采集阶段采用北斗同步时钟确保时标统一,采样频率提升至128点/周波;分析诊断阶段运用改进蚁群算法进行损耗路径寻优,结合设备红外图谱建立三维线损热力图;优化验证阶段通过STATCOM装置进行动态无功补偿测试。在长庆油田的实践中,该流程使检测周期缩短40%,定位异常点准确率提升至92%。
3. 行业应用与效益分析
以克拉玛依稠油开采区为例,部署"油气田智能配电网线损分析系统"后,6个月周期内线损率从9.7%降至6.2%。通过加装132套温度-电流复合传感器,发现3处电缆接头氧化导致的异常温升点,及时更换后年避免电量损失380万kWh。据中国石油经济技术研究院测算,全国油气田推广该技术后,年节电量可达42亿kWh,相当于减少燃煤电厂二氧化碳排放340万吨。特别在海上平台受限空间场景中,微型化检测装置解决了传统PT/CT安装难题。
4. 质量保障体系构建
建立涵盖设备、数据、人员的三级质控体系:设备层执行JJG 1148-2022电子式互感器检定规程,数据层采用区块链存证确保可追溯性,操作层实施AQ 2043-2023石油行业电力安全规范。实验室对比测试表明,系统在±50℃环境温度波动下仍保持0.5级精度,电磁兼容性通过GB/T 17626标准的4级抗扰度测试。同时开发了基于数字孪生的仿真训练平台,有效提升现场工程师的异常诊断能力。
面向行业未来发展,建议重点突破三个方向:构建基于数字孪生的线损智能诊断平台,实现预测性维护;制定适应非常规油气开发的线损评价标准体系;推动5G-Mesh网络在偏远井区的全覆盖应用。随着新型电力系统建设加速,"高精度线损率动态监测技术"将成为油气田数字化转型的核心支撑,助力我国能源行业在能效管理领域达到国际领先水平。
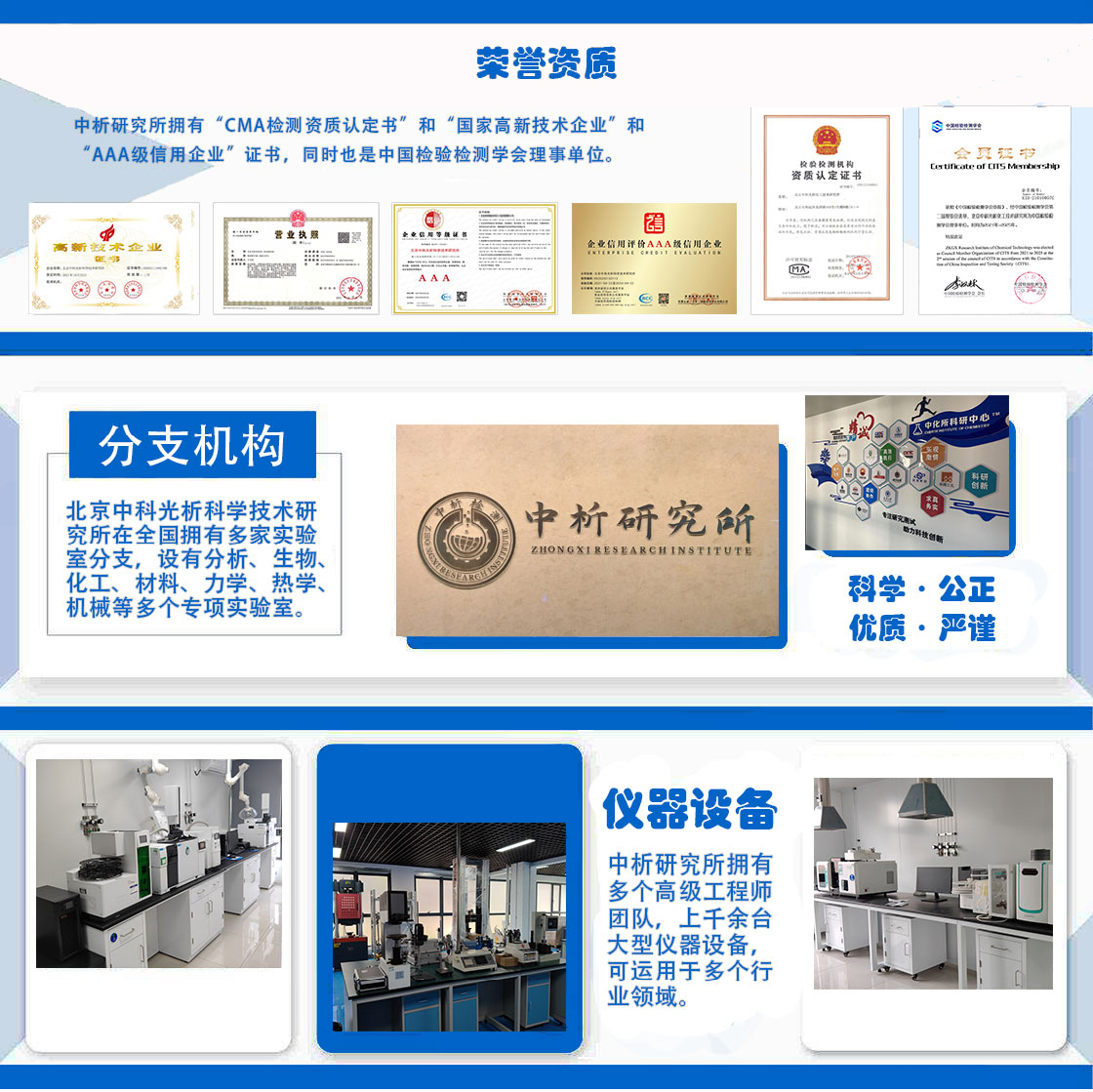
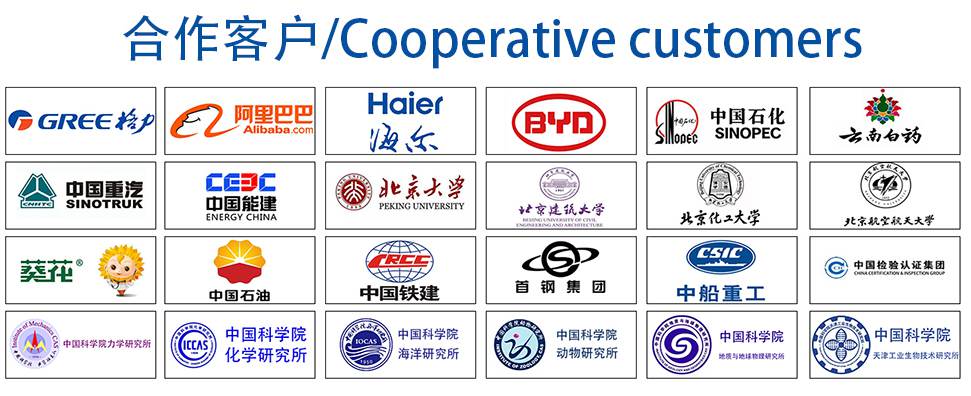