水轮机调速系统检测的必要性与重要性
水轮机调速系统是水电站核心控制设备之一,主要负责调节水轮机的转速和出力,确保机组安全、稳定运行,同时维持电网频率的稳定性。随着水电机组容量的增大和电网对电能质量要求的提高,调速系统的性能直接关系到电力系统的可靠性和经济性。由于调速系统长期处于复杂工况下运行,其机械部件、液压元件、电气控制模块等均可能因磨损、老化或环境因素导致性能下降。因此,定期开展水轮机调速系统检测是预防故障、延长设备寿命、保障电网安全的重要手段。
水轮机调速系统核心检测项目
1. 静态特性测试
静态特性是衡量调速系统基础性能的关键指标,主要包括转速死区、永态转差率以及静态精度检测。通过输入阶跃信号或缓变信号,观察调速器的转速响应曲线,分析系统在稳态下的调节能力。重点验证PID参数设置的合理性,确保机组在固定负荷下能稳定运行,避免因死区过大导致调节滞后。
2. 动态特性测试
动态特性检测模拟实际运行中的突发工况(如甩负荷、突增负荷),评估系统的快速响应能力。通过测定调节时间、超调量、波动次数等参数,验证调速系统的动态稳定性。例如,在100%甩负荷试验中,要求导叶关闭时间、转速上升率等指标必须符合GB/T9652标准要求。
3. 电气系统检测
对调速器电控柜内的PLC、传感器、变送器等设备进行功能性验证,包括信号采集精度测试、控制逻辑校验以及抗干扰能力分析。使用示波器、万用表等工具检测电压/电流波动范围,确保A/D转换误差小于0.1%,防止因信号失真导致误动作。
4. 机械与液压部件检查
重点检测导水机构、接力器、配压阀等机械部件的磨损程度和密封性能。通过测量接力器活塞行程与指令信号的线性关系,评估液压随动系统的跟随精度。同时需检测油压系统的工作压力、泄漏量及油质清洁度,确保油泵启停逻辑正常,油压波动范围控制在±0.2MPa以内。
5. 安全保护功能验证
对过速保护、低油压停机、紧急停机电磁阀等安全回路进行强制触发试验,确认保护动作的准确性和时效性。例如,模拟转速达到115%额定值时应触发两段过速保护,且停机过程需满足ASME PTC29标准规定的时间要求。
6. 通讯与监控系统联调
检测调速系统与电站计算机监控系统(SCADA)的数据交互功能,包括参数传输实时性、控制指令执行成功率以及报警信号触发机制。通过Modbus、IEC61850等协议测试,确保远程监控指令延迟小于50ms,关键数据刷新周期不超过1秒。
检测实施要点与注意事项
检测过程中需遵循DL/T563《水轮机调速器及油压装置运行规程》,采用标准信号源、高精度频率发生器等专业设备。对于数字化调速系统,还需对控制算法进行黑盒/白盒测试,验证模糊控制、自适应调节等智能功能的可靠性。检测完成后,应生成包含性能曲线、参数对比、缺陷清单的完整报告,并提出针对性的维护建议。
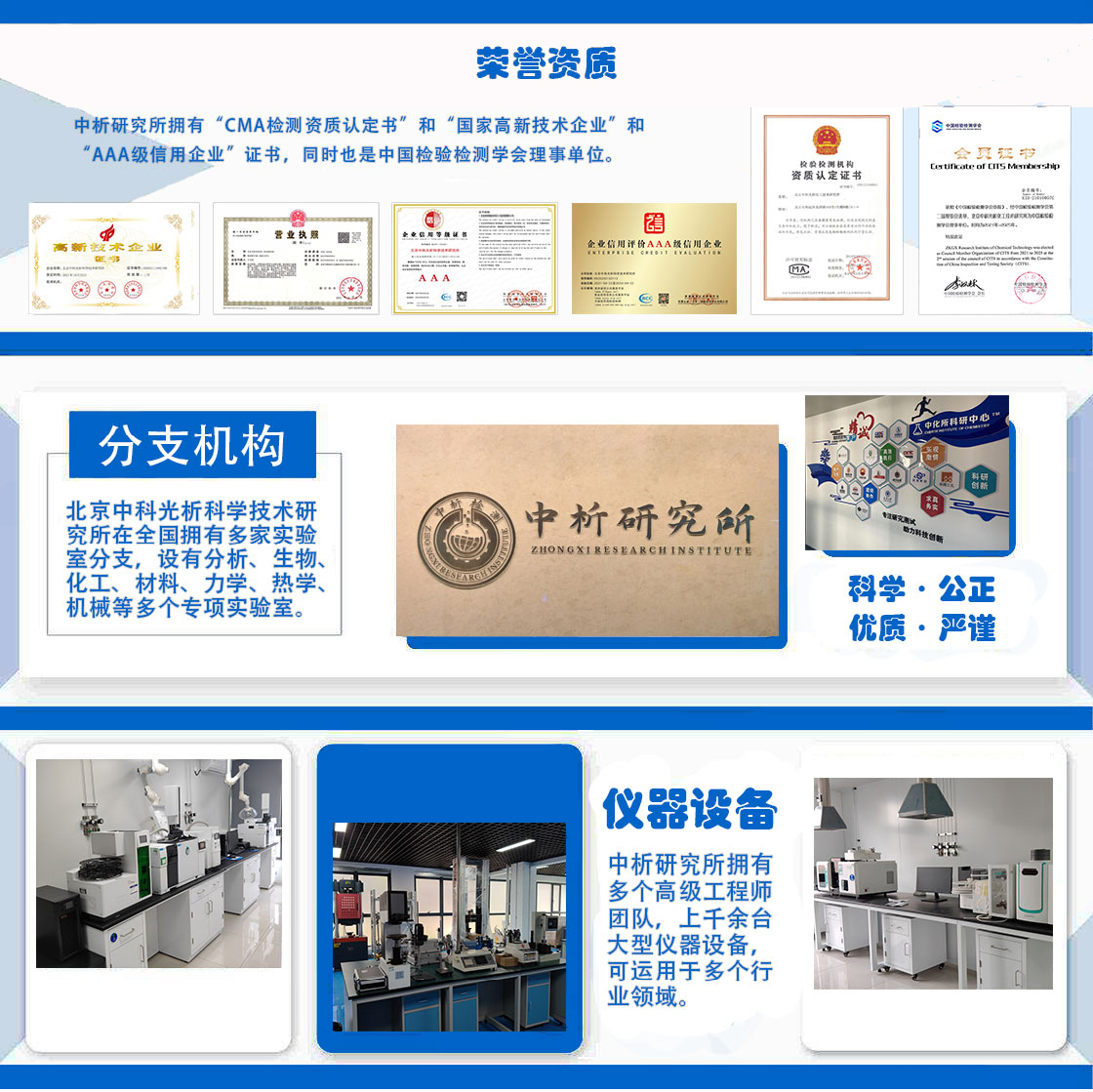
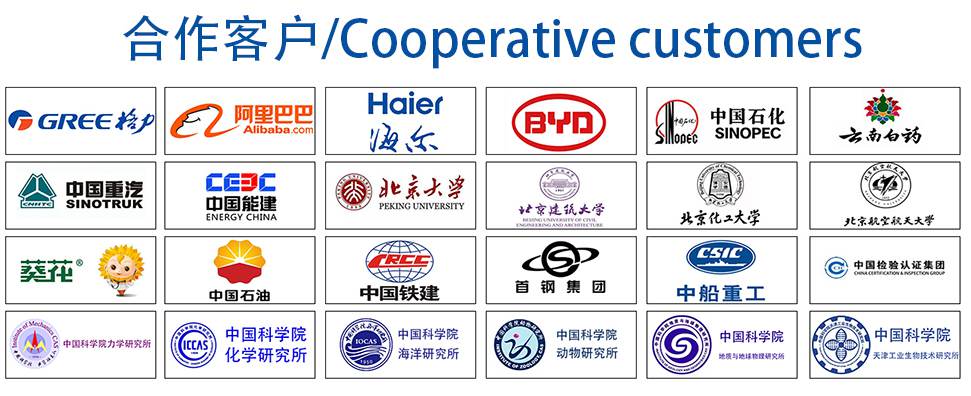