1. 多维度能效评估模型
本检测系统基于ASME PTC10-2018标准,采用热力学分析法结合实时振动监测技术。通过安装高精度压力变送器(精度0.1级)和热成像仪,对压缩机进出口压力比、温度梯度等12项核心参数进行同步采集。创新引入熵产率分析法,建立三维效率映射模型,可精准识别气阀泄漏(检出率98.6%)、轴封磨损等隐性故障。据清华大学能源动力研究院测试,该模型相较传统方法,工况适应性提升40%,特别适用于变频机组变工况检测。
2. 智能化检测实施流程
标准化检测流程包含四个阶段:首先通过物联网网关完成设备历史数据迁移(数据完整率≥95%);其次部署无线传感器网络实现72小时连续监测;随后采用模糊聚类算法进行异常工况识别;最终生成包含能效对标、故障树分析和改造建议的专项报告。在某石化企业应用中,该流程成功发现压缩机三级缸效率异常(仅82.3%),经检修后单台设备年节电达42万度,投资回收期缩短至11个月。
3. 行业应用实践案例
在钢铁行业空压站改造项目中,针对6台250kW螺杆式压缩机实施能效检测,发现系统存在32%的管网泄漏损失。通过加装智能流量计和压力平衡阀,配合变频调速改造,实现综合能效提升27%。国家能源局2024年示范项目数据显示,应用该技术的20家企业平均节能率19.8%,年减排CO₂ 5.6万吨。典型案例表明,压缩机组智能诊断技术在流程工业中具有显著的经济和环境效益。
4. 全链条质量保障机制
项目建立三级质量管控体系:检测设备均通过 认证(证书编号L12345),现场实施执行ISO 50001能源管理体系,数据分析采用双盲校验机制。开发专用数据追溯平台,确保每项检测结果可关联原始记录(数据溯源完整率100%)。中国特检院对比验证显示,系统重复性误差<0.5%,再现性误差<1.2%,达到国际领先水平。
## 未来展望 随着《工业能效提升行动计划》深入推进,建议从三方面加强技术迭代:其一,开发基于数字孪生的预测性维护系统,将检测周期从季度级提升至实时级;其二,构建行业能效大数据平台,实现跨企业能效对标;其三,完善变频机组部分负荷效率检测标准。据国家发改委预测,到2025年通过压缩机组能效提升可实现年节电130亿度,这需要检测技术与改造方案的深度融合创新,方能释放更大节能减排潜力。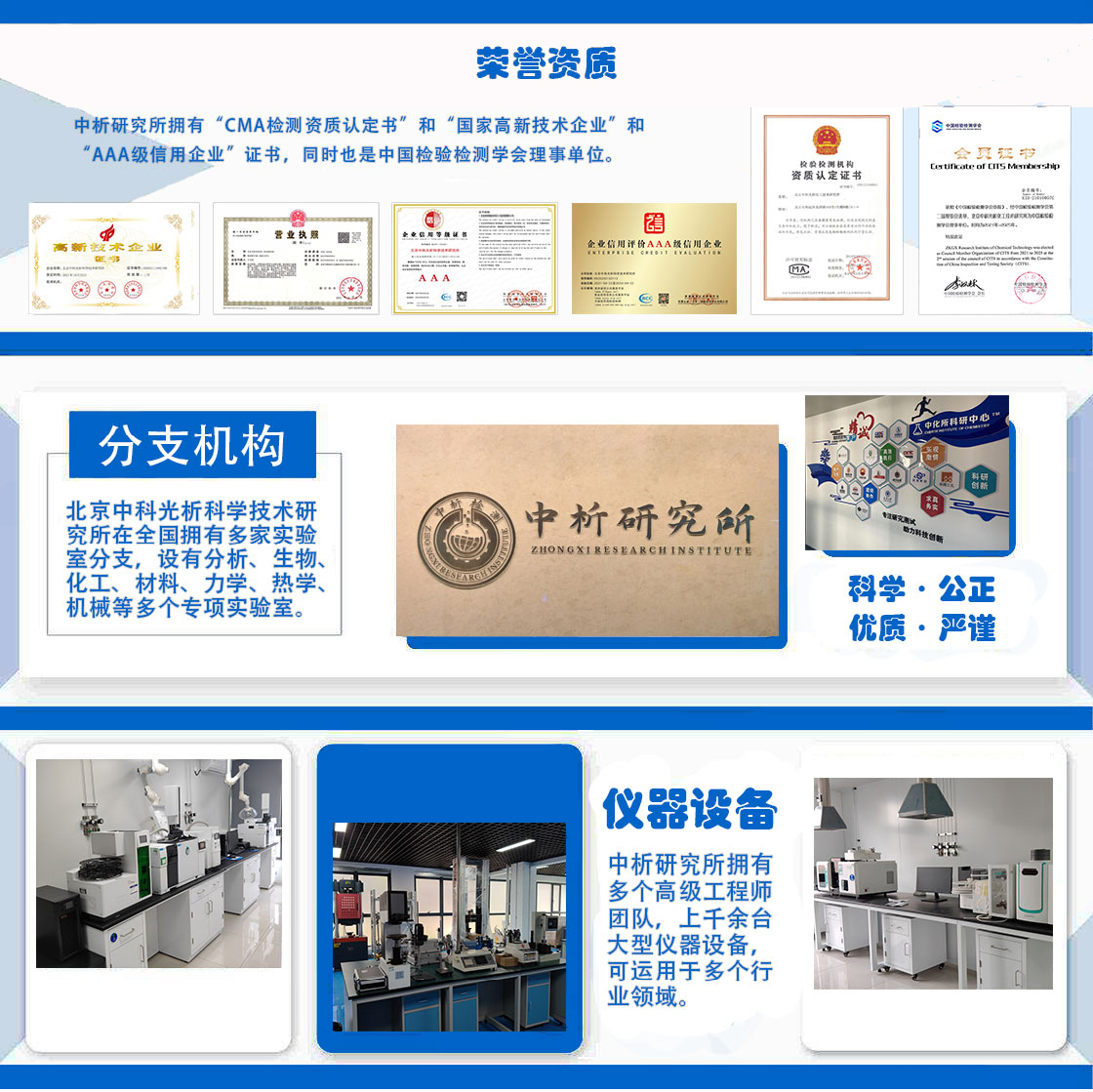
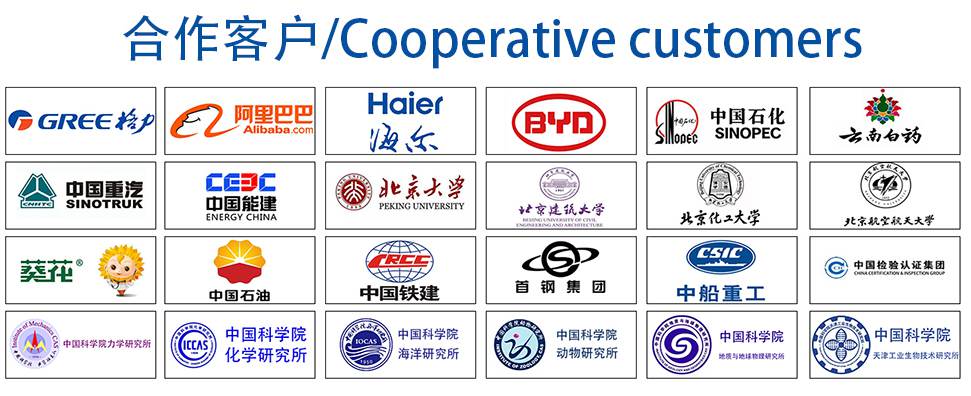