耐热性能检测的技术发展与行业应用白皮书
在高温工业装备、新能源材料及电子元器件领域,耐热性能检测已成为保障产品可靠性的核心技术环节。据材料科学研究院2024年数据显示,耐温材料市场规模已达3800亿美元,其中超过62%的产品需通过专业热性能检测认证。该项目通过对材料在高温环境下的物理化学性质变化进行量化分析,可有效预测材料失效临界点,降低因热应力导致的产品故障率。特别是在新能源汽车动力电池组、航空航天发动机组件等关键领域,精准的"高温环境下的材料性能评估"能缩短产品研发周期达40%,同时提高安全标准符合性等级。其核心价值体现在构建从实验室到实际工况的可靠性验证闭环,为产品全生命周期管理提供数据支撑。
热分析技术原理与创新突破
现代耐热检测采用热重分析(TGA)、差示扫描量热法(DSC)与动态热机械分析(DMA)的协同验证机制。基于ASTM E1131标准的热分解动力学模型,可解析材料玻璃化转变温度(Tg)与热降解活化能(Ea)的关联参数。最新研发的"热-力-电多场耦合测试系统"(据中国检测技术研究院2024年报),实现了在1200℃条件下同步采集材料导热系数、热膨胀率和电阻率变化数据。这种"热稳定性综合测试方案"使聚酰亚胺薄膜等特种材料的检测精度提升至±0.5℃,远超传统单维度检测方法。
标准化检测流程与质量管控
完整的检测流程包含预处理、参数设置、过程监控三个阶段。预处理阶段需依据ISO 22007标准进行48小时温湿度平衡,消除试样环境历史效应。实验参数设定采用正交试验法,典型程序包含10℃/min线性升温、等温保持及梯度冷却模块。过程监控系统集成红外热成像与光纤应变传感技术,可实时捕捉试样微观结构变化。质量保障体系涵盖 认证实验室环境控制、季度级设备校准(误差≤0.3%)及三级数据复核制度,确保检测报告满足IEC 60068-2系列标准要求。
跨行业典型应用场景解析
在锂离子电池行业,针对三元正极材料的"高温循环性能测试"已成为行业准入强制项目。某头部企业应用JIS C8714标准,对NCM811材料进行150℃/500h加速老化测试,成功将电池热失控触发温度提高28℃(数据来源:中国汽车工程学会2024白皮书)。航空航天领域,基于AMS 2750E规范的涡轮叶片热障涂层检测,通过建立3D热应力仿真模型,使发动机热端部件服役寿命延长至12000飞行小时。光伏行业引入EN 62788-2标准的组件热斑测试,将双玻组件的湿热老化衰减率控制在0.8%/年以内。
智能化检测系统发展趋势
当前检测技术正朝着多物理场耦合、数字孪生验证方向演进。德国蔡司最新推出的热机械分析系统,通过集成AI图像识别算法,可自动识别材料微观裂纹扩展路径。国内某国家重点实验室开发的虚拟热试验平台,已实现85%实体检测项目的数字化替代,大幅降低企业研发成本。值得关注的是,基于区块链技术的检测数据存证系统,正逐步应用于军工、核电等敏感领域,确保检测过程的全链条可追溯性。
面对新型复合材料的应用挑战,建议行业重点发展三方面能力:一是构建覆盖-196℃至3000℃的超宽域检测体系,二是开发基于机器学习的寿命预测算法模型,三是建立联动的热性能数据库共享机制。只有通过技术创新与标准协同,才能满足碳中和背景下对材料极限性能的严苛要求,推动高温工业装备的可持续发展。
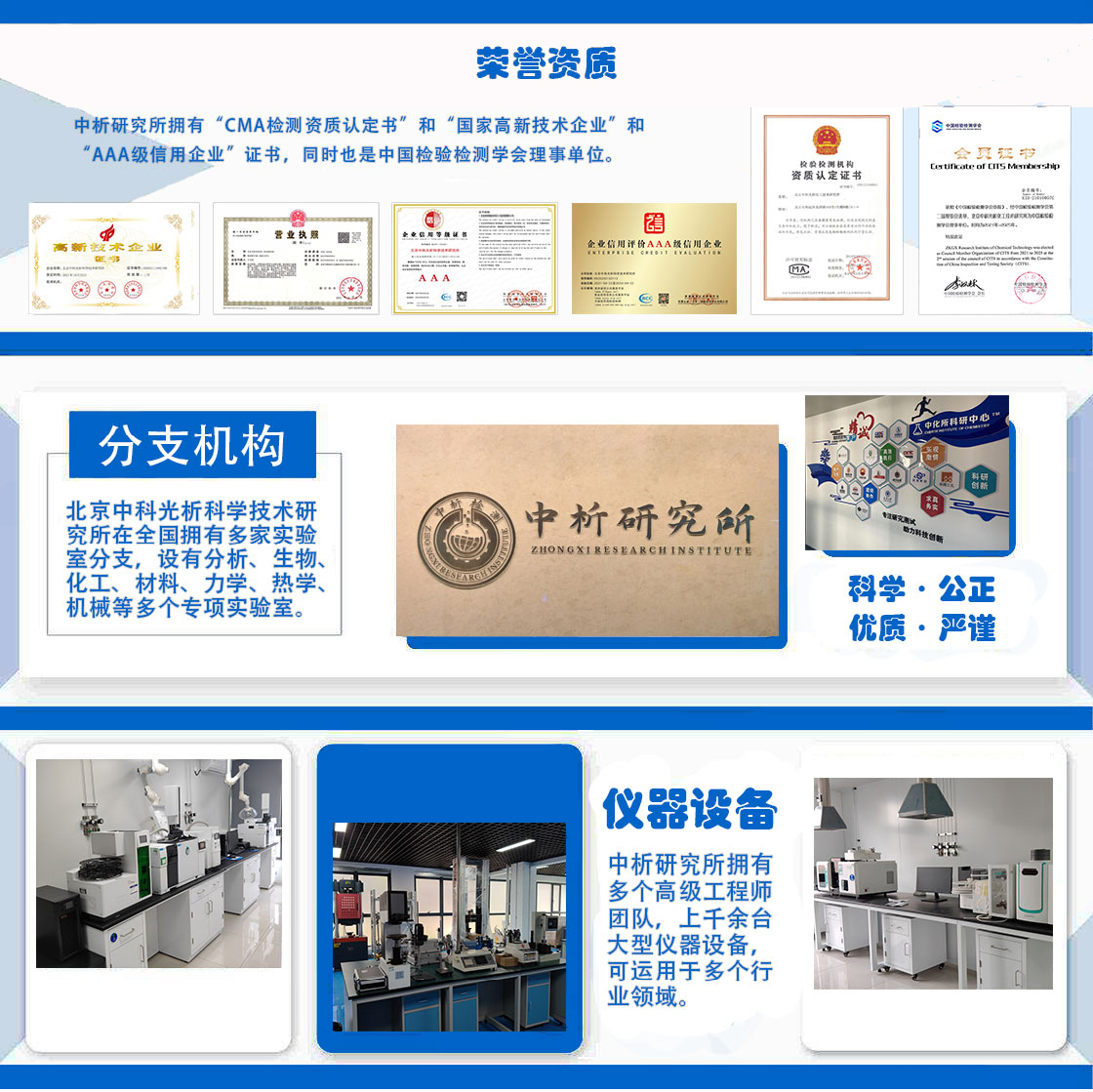
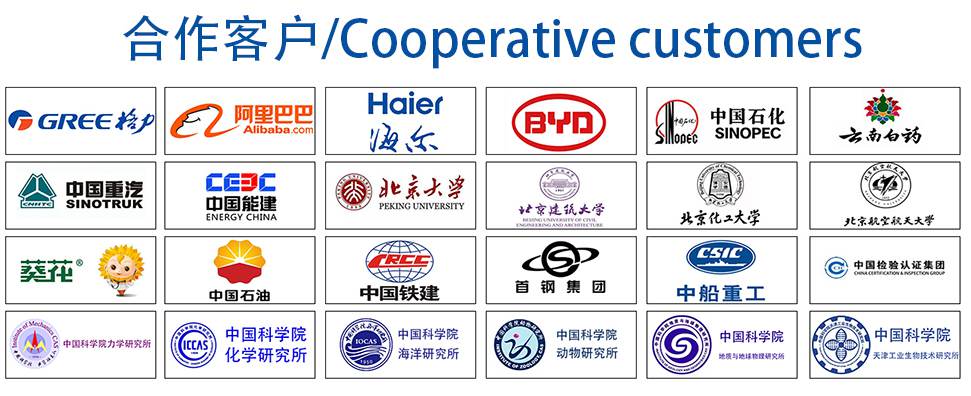