方钻杆检测的重要性与核心内容
方钻杆作为石油钻井作业中连接转盘与钻具的关键部件,承担着传递扭矩、承受轴向载荷和循环钻井液的重要功能。其长期处于高温、高压、强振动的恶劣工况下,易出现磨损、疲劳裂纹、螺纹损伤等安全隐患。为确保钻井作业的安全性和效率,定期开展系统性方钻杆检测至关重要。通过科学的检测手段,能够及时发现潜在缺陷,避免因部件失效导致的钻井事故,同时延长设备使用寿命,降低运营成本。
方钻杆检测的主要项目
1. 外观与尺寸检测
通过目视检查、卡尺测量和三维扫描技术,重点检测方钻杆外表面是否存在划痕、凹坑、腐蚀等缺陷,同时验证其外径、内径、壁厚等尺寸参数是否符合API标准要求。特别需关注驱动段棱边磨损量,若单边磨损超过3mm则需修复或更换。
2. 材料性能检测
采用光谱分析仪进行材质成分验证,确保合金元素含量符合设计要求;通过拉伸试验机测试屈服强度(通常要求≥758MPa)和抗拉强度(≥862MPa);利用夏比冲击试验评估低温环境下的韧性表现。
3. 无损探伤检测
综合应用三种齐全技术:
- 超声波检测(UT)发现内部裂纹和夹杂物
- 磁粉检测(MT)识别表面及近表面缺陷
- 渗透检测(PT)验证非磁性材料的表面开口缺陷
重点关注应力集中区域(如螺纹根部、截面突变处)的裂纹扩展情况。
4. 螺纹连接检测
使用专用螺纹规检查API标准NC50、NC56等扣型的紧密距、锥度等参数,通过荧光渗透法检测螺纹牙底的疲劳裂纹。同时需测量螺纹部位的表面硬度(通常要求HRC22-32),评估其抗粘扣性能。
5. 动态性能测试
在模拟工况的液压试验台上进行:
- 扭矩加载测试验证极限承载能力(≥40kN·m)
- 高频振动试验检测共振频率和疲劳寿命
- 水压密封试验确保工作压力下(≥35MPa)无渗漏
6. 金相组织分析
通过显微组织观察,检查热处理是否导致晶粒粗化、脱碳层超标(>0.15mm)等异常,评估材料在长期使用后的微观结构变化趋势。
检测周期与判定标准
根据API RP 7G标准,常规检测周期为每钻进5000米或单次作业周期不超过6个月。对于发现单个裂纹长度>6mm、壁厚减薄量>12.5%、或存在贯穿性缺陷的情况,应立即停止使用并作报废处理。
通过建立完整的检测档案和数字化管理系统,可实现方钻杆全生命周期的健康状态监控,为石油钻井装备的安全运行提供可靠保障。
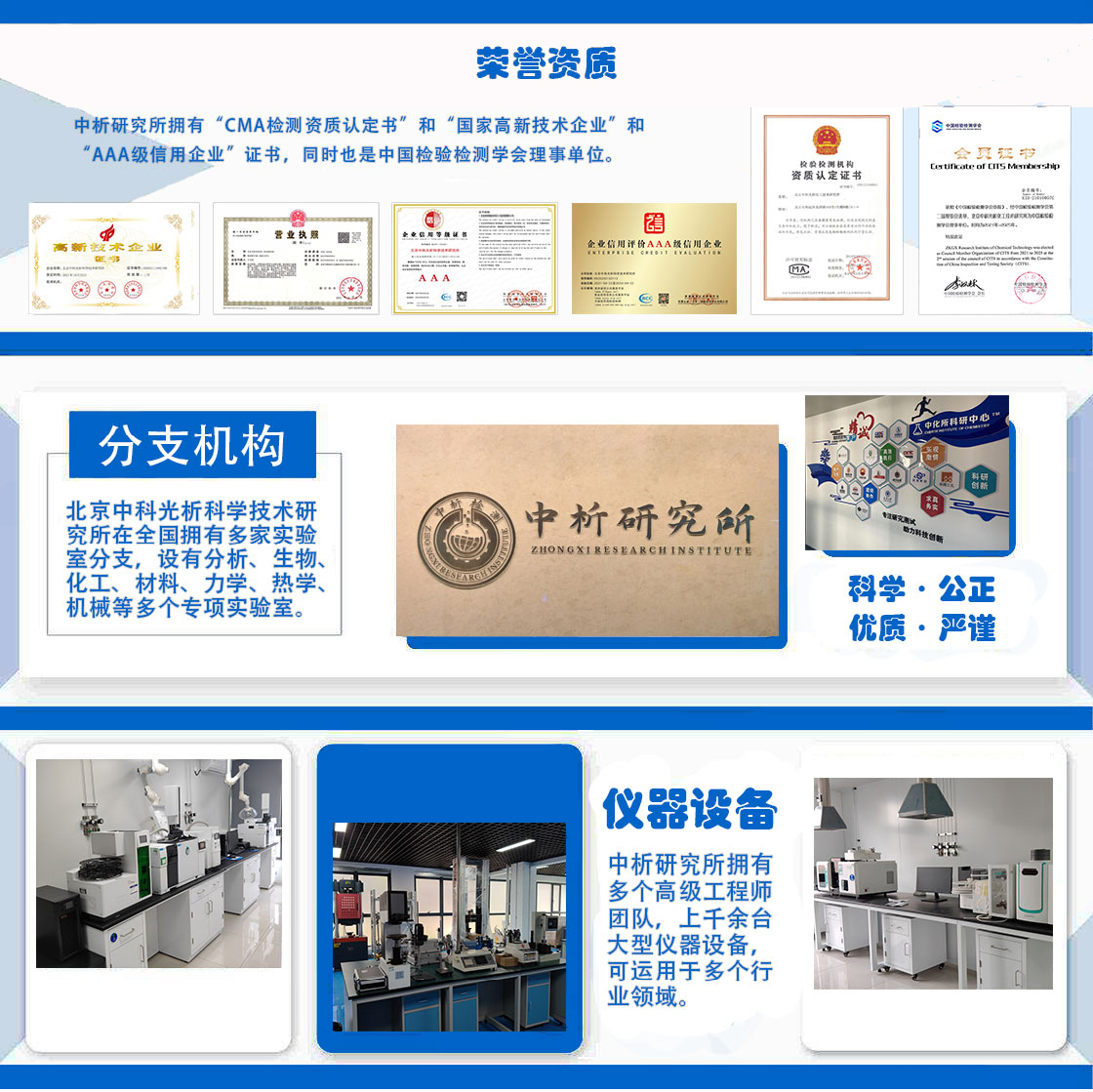
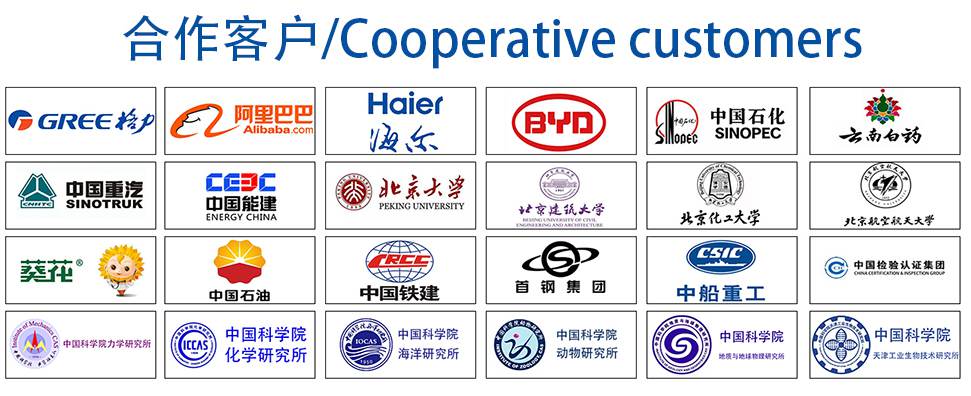