复合射孔器混凝土靶实验检测的意义与流程
复合射孔器作为油气井增产改造的关键工具,其性能直接关系到射孔作业的安全性和有效性。混凝土靶实验是评估射孔器穿透能力、破岩效果以及结构完整性的重要检测手段,通过模拟地下储层岩石的物理特性,验证射孔弹与射孔枪的匹配性、射孔深度及孔径是否符合设计要求。该实验不仅能优化射孔方案,还能为井下作业风险控制提供科学依据,是石油工程领域不可或缺的质量验证环节。
核心检测项目及技术要求
在复合射孔器混凝土靶实验中,需重点关注以下检测项目:
1. 射孔穿透深度检测
使用高精度测量仪器测定射孔弹穿透混凝土靶的总深度,误差需控制在±5mm以内。通过对比理论设计值与实际测量值,验证射孔弹装药量和药型罩结构的合理性。典型行业标准要求中密度混凝土靶(抗压强度35-45MPa)的穿透深度应达到预定目标的90%以上。
2. 射孔孔径及裂缝形态分析
采用三维扫描仪或断面剖切法获取射孔孔道直径、孔道形态及裂缝扩展特征。重点检测孔径均匀性、孔道直线度以及裂缝网络分布范围,要求平均孔径偏差不超过设计值的±10%,裂缝延伸长度应满足增产改造需求。
3. 套管损伤评估
在实验靶体内预埋模拟套管(材质为J55或N80钢级),通过超声波探伤和显微观察检测射孔后的套管变形、裂纹及毛刺情况。判定标准包括:套管穿孔边缘毛刺高度≤1mm,周边无超过2mm的径向裂纹,椭圆度变形量控制在3%以内。
4. 射孔弹残留物检测
收集孔道内残留的金属药型罩碎片和未完全燃烧的炸药成分,通过X射线荧光光谱分析(XRF)和质谱分析法(MS)评估材料燃烧效率,残留物质量不得超过装药总量的5%,且不得含有影响后续增产作业的有害物质。
5. 动态压力与温度数据采集
在混凝土靶内部署高频压力传感器和热电偶,记录射孔瞬间冲击波压力峰值(通常要求达到100-300MPa)、压力衰减曲线以及温度变化范围(一般不超过300℃)。这些数据为优化射孔参数提供关键支撑。
实验质量控制的创新方向
随着智能检测技术的发展,复合射孔器混凝土靶实验正逐步引入数字化手段。例如应用CT扫描技术实现孔道三维重建,利用机器学习算法预测裂缝扩展模式,以及通过声发射技术实时监测射孔过程。这些创新方法显著提升了检测精度和效率,为射孔器性能评估建立了更完善的科学体系。
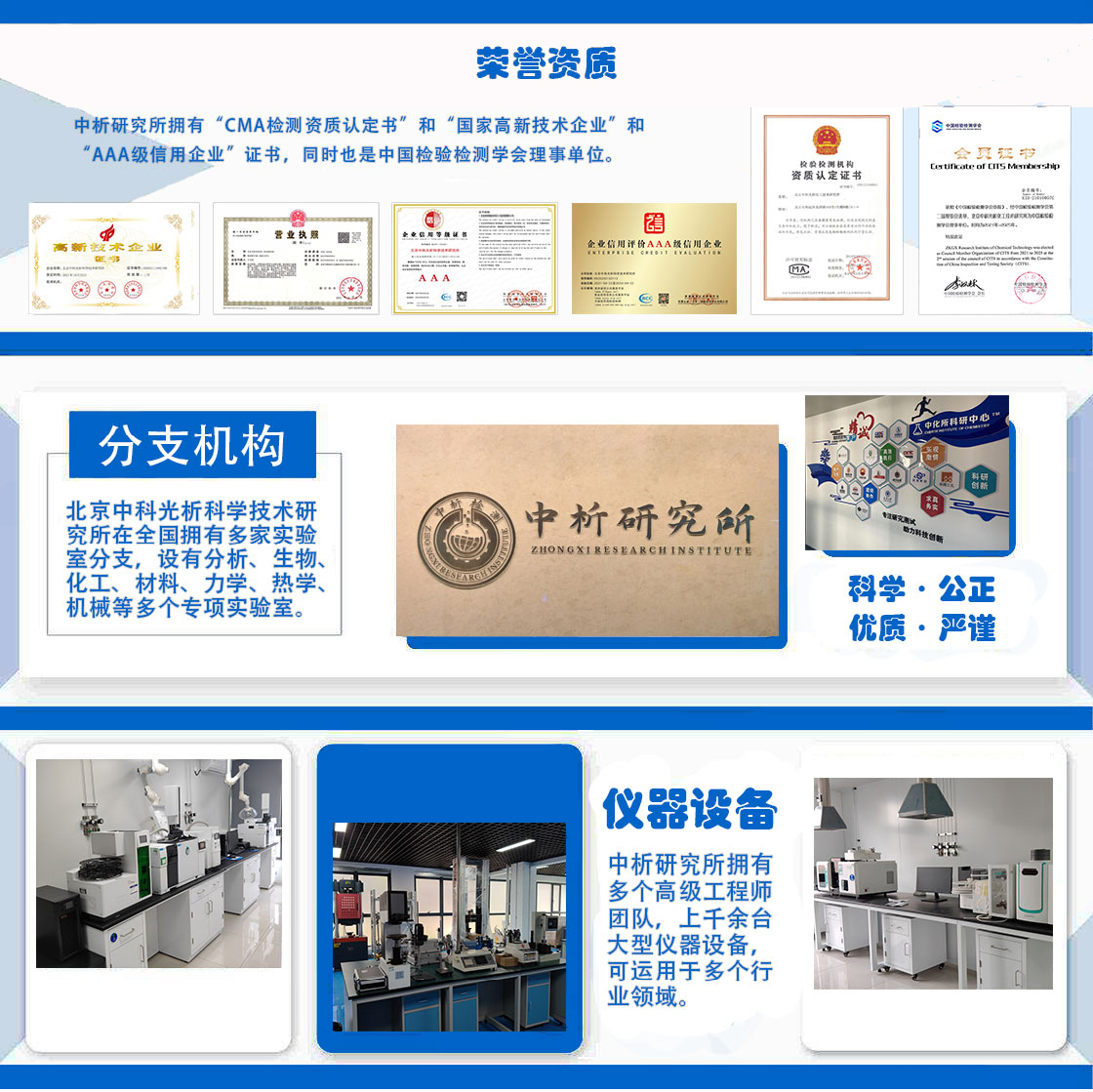
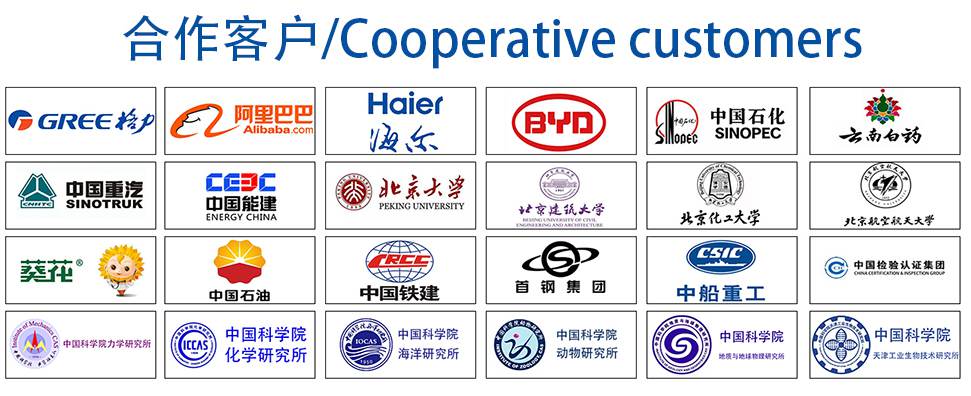