抽油泵脱接器检测项目与技术要点解析
在石油开采作业中,抽油泵脱接器作为连接抽油杆与泵体的核心组件,其性能直接影响着油井生产效率和设备安全性。由于长期承受交变载荷、腐蚀介质及高温高压环境,脱接器易出现磨损、变形或疲劳失效,开展系统化检测成为保障设备运行的关键环节。本文针对抽油泵脱接器的功能特性与工况特点,重点列举关键检测项目及实施方法。
一、基础性能检测
1. 外观完整性检测:采用工业内窥镜与磁粉探伤技术,检查螺纹连接处是否存在裂纹、锈蚀或机械损伤,重点关注应力集中区域。
2. 尺寸精度验证:使用三坐标测量仪对关键配合尺寸(如接箍内径、螺纹导程)进行微米级测量,确保符合API Spec 11B标准要求。
3. 材质分析:通过光谱分析仪检测材料化学成分,辅以金相组织观察,确认是否发生材质劣化或晶间腐蚀。
二、力学性能测试
1. 抗拉强度试验:在万能试验机上模拟最大工作载荷的1.5倍进行静载拉伸,记录屈服强度与断裂延伸率。
2. 扭矩传递测试:采用动态扭矩传感器监测旋合过程中扭矩-角度曲线,评估螺纹啮合均匀性和防松性能。
3. 冲击韧性检测:通过夏比冲击试验测定低温环境下的材料韧性,预防脆性断裂风险。
三、工况适应性检测
1. 密封性能验证:建立1.2倍工作压力的液压测试系统,持续保压30分钟检测密封面泄漏量。
2. 振动疲劳试验:在电磁振动台上模拟井下振动谱,进行10^7次循环测试并监测结构完整性。
3. 耐腐蚀评估:配置模拟地层流体的腐蚀介质,开展加速腐蚀试验评估表面处理层的防护效果。
四、智能诊断技术应用
1. 声发射监测:安装声发射传感器实时捕捉脱接器工作时的应力波信号,通过模式识别判断微裂纹萌生。
2. 应变场分析:采用光纤光栅传感器网络,构建三维应变分布云图,定位潜在失效危险点。
3. 数字孪生建模:基于实测数据建立脱接器寿命预测模型,实现剩余寿命的智能化评估。
现代检测技术已形成从传统理化检测到智能在线监测的完整体系,建议油田单位建立包含定期检测(每3个月)、工况监测(实时)、大修期全面检测(每年)的多级防控机制。通过标准化检测流程与智能诊断技术的结合,可有效降低脱接器失效导致的检泵作业频率,显著提升抽油系统运行经济性。
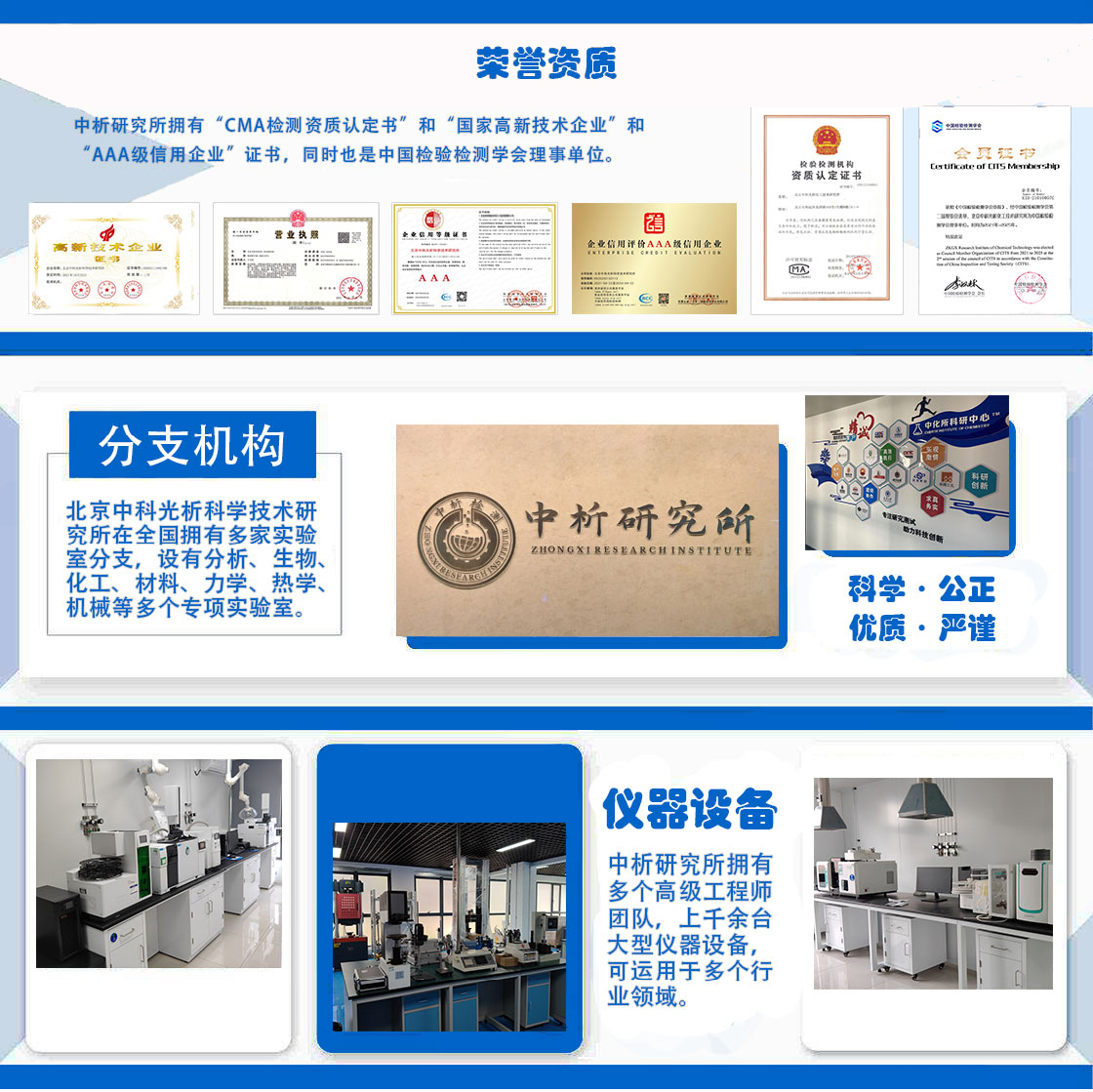
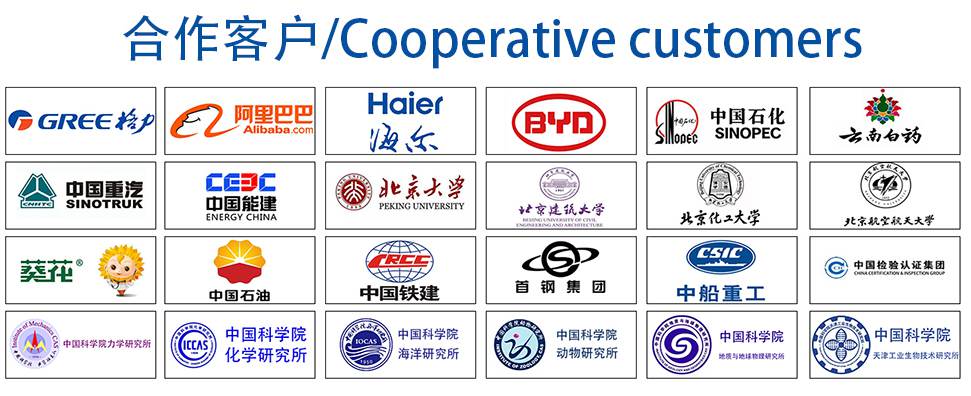