蓄电池充电控制器检测的重要性
蓄电池充电控制器作为新能源系统、电动汽车及储能设备的核心组件,其性能直接影响电池寿命、充电效率和系统安全性。随着技术进步和应用场景的多样化,控制器需适应不同电池类型(如铅酸、锂离子)和环境条件。定期检测能够验证其充放电控制逻辑、电压/电流调节精度以及保护功能的可靠性,避免因控制器故障导致的过充、过放、温升异常等问题,从而延长电池使用寿命并降低安全风险。
核心检测项目及方法
1. 基础参数检测
通过专业仪器测量控制器的输入/输出电压范围、最大输出电流及转换效率,确保符合标称值(如±2%误差范围内)。同时需测试空载功耗,验证其在待机状态下的能耗是否符合节能标准(通常要求≤1W)。
2. 充电阶段控制验证
模拟电池不同SOC(荷电状态)场景,检测控制器能否正确执行三段式充电流程:恒流充电阶段电流稳定性、恒压阶段电压波动范围(≤±0.5%)、浮充阶段维持电压精度。针对智能控制器,还需验证动态调整算法对电池老化的适应性。
3. 保护功能测试
采用可编程负载模拟异常工况,包括:
- 过压/欠压保护触发阈值及响应时间(通常≤100ms)
- 过流保护动作精度(标称值的105%-120%)
- 短路保护自恢复特性
- 温度保护(环境温感精度±2℃,散热片温升≤40K)
4. 通信与兼容性检测
对支持CAN/RS485/BMS协议的控制器,需测试通信速率(如250kbps~1Mbps)、数据帧解析正确率和抗干扰能力。同时验证其与主流电池管理系统(BMS)的匹配性,包括充电策略同步、故障码交互等功能。
行业检测标准与设备要求
检测需参照GB/T 34131-2017《储能变流器检测技术规范》、UL 1741等标准,使用高精度直流电源(分辨率≤0.1mV)、多通道数据记录仪(采样率≥10kHz)、温湿度循环试验箱等设备。推荐每季度进行常规检测,新装机或系统升级后需执行全项检测。
特殊场景附加检测项
针对光伏/风电等新能源系统,需增加MPPT(最大功率点跟踪)效率测试(≥98%);车载控制器应增加振动试验(5-500Hz扫频测试)和EMC抗扰度测试(符合ISO 11452-2标准)。智能型控制器还需进行固件版本验证和远程控制响应测试。
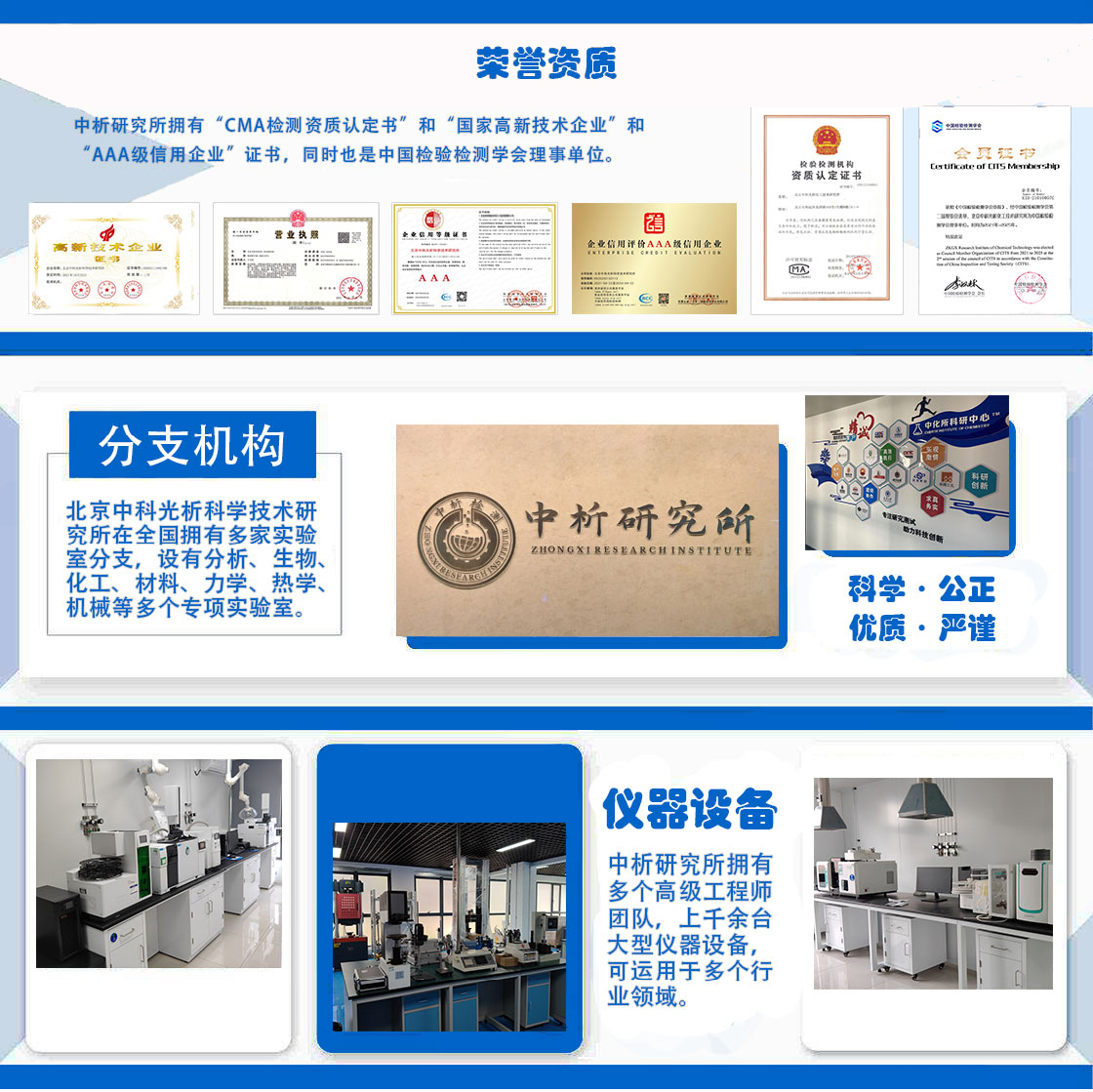
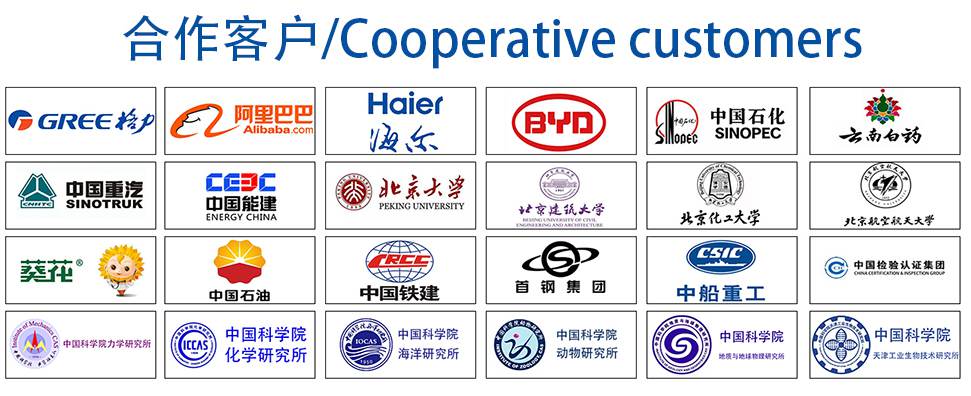