压缩空气干燥器检测的必要性
压缩空气干燥器作为工业用气系统的核心设备,承担着去除压缩空气中水分、油雾、颗粒物等杂质的关键任务。其运行状态直接影响压缩空气的露点值、供气质量及后端设备的稳定性。若干燥器性能不达标,可能导致气动设备锈蚀、精密仪器故障,甚至引发生产线停工。因此,定期开展压缩空气干燥器检测是保障工业系统安全运行、降低能耗、延长设备寿命的重要技术手段。根据ISO 8573-1标准,压缩空气的湿度等级需控制在特定范围内,这要求干燥器必须通过科学的检测流程验证其效能。
核心检测项目分析
1. 露点温度检测
使用便携式露点仪对干燥器出口空气进行连续监测,验证其是否达到标称压力露点(如-40℃或-70℃)。需在不同负载工况下测试,并关注露点波动范围是否超出允许偏差值(通常±3℃)
2. 压力降测试
通过压差计测量干燥器进出口压差,对比设计参数判断吸附剂床层是否出现板结或堵塞。制冷式干燥器需额外检测蒸发器与冷凝器的压差变化,评估制冷系统效率。
3. 吸附剂性能检测
针对吸附式干燥器,需取样检测分子筛/活性氧化铝的吸附容量、抗碎强度及含水率。使用红外光谱分析吸附剂结晶结构是否退化,并通过颜色指示剂判断是否发生油污染。
4. 再生系统验证
检测再生气体温度曲线是否符合设计要求,微热式干燥器需检测再生耗气量,无热式则需验证切换阀门的时序控制精度。通过热成像仪检查加热元件的工作状态。
5. 排放系统检测
使用浮子流量计测量冷凝水排放量,验证自动排水器响应灵敏度。通过目视检查排水口是否出现油污积聚,判断前置过滤器是否失效。
智能化检测新趋势
现代检测方案开始集成物联网传感器,通过在线露点监测+云端数据分析实现预测性维护。采用超声波检漏仪检测阀门密封性,配合热力学效率计算模型评估系统综合能效。建议每季度开展常规检测,吸附剂每2年更换一次,确保干燥器持续满足ISO 8573标准要求。
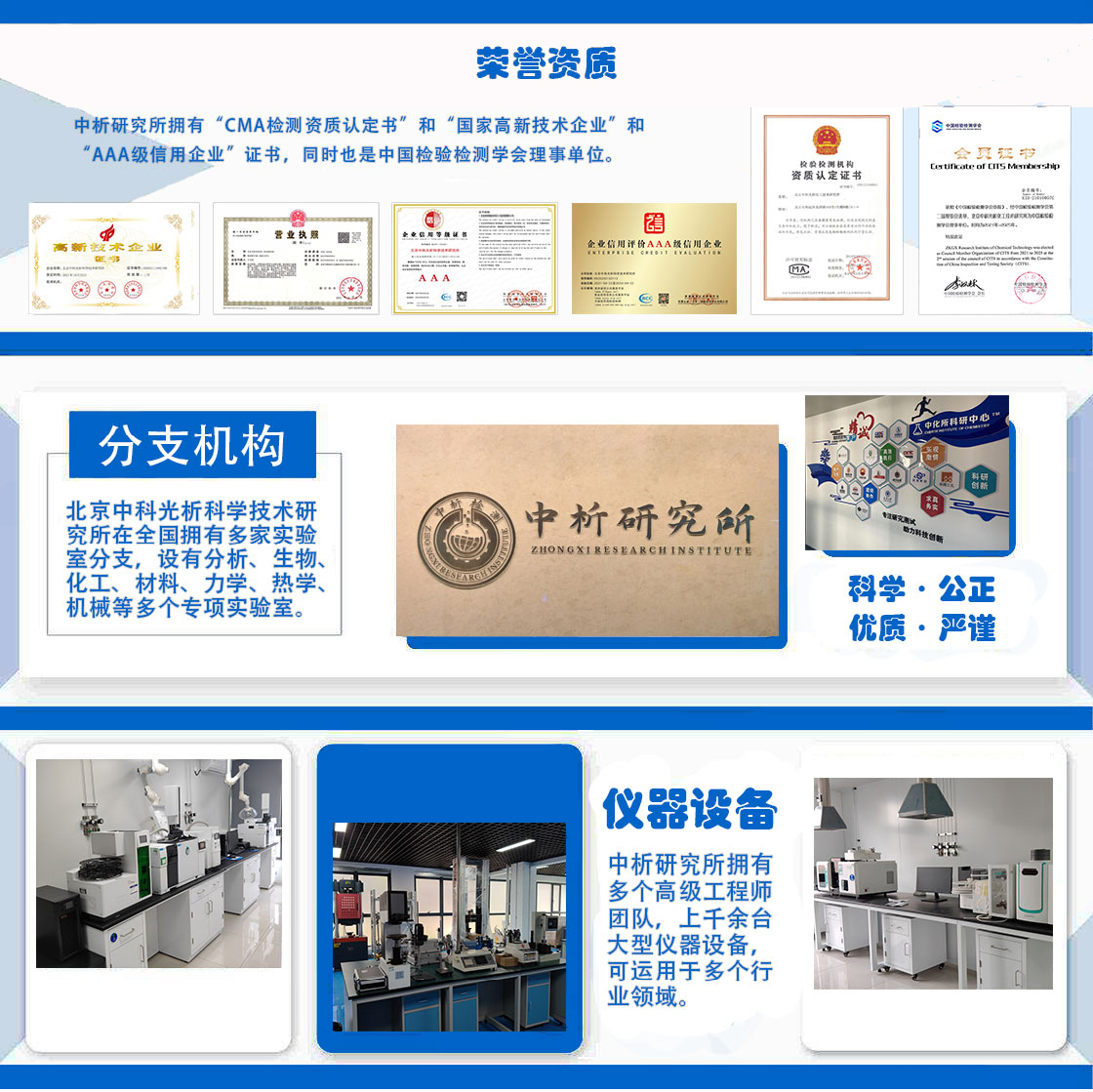
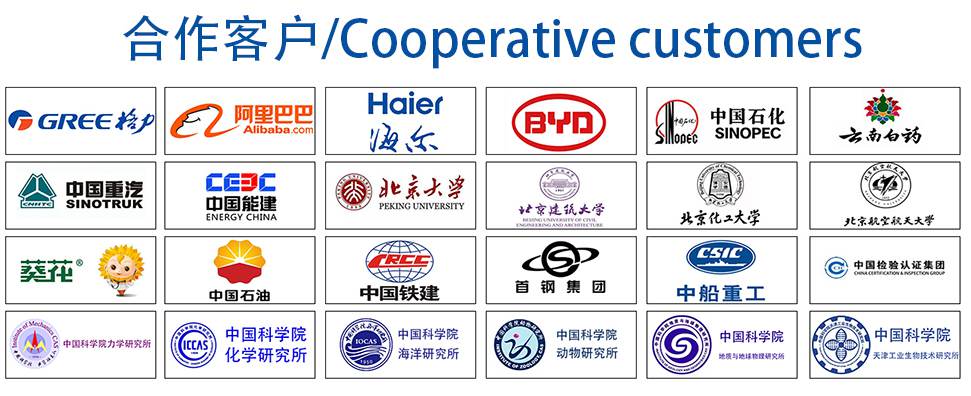