管道质量检测的重要性与应用场景
管道系统作为工业生产和市政基础设施的重要组成部分,其质量直接关系到能源输送效率、环境保护及公共安全。管道质量检测是通过科学手段对管道材料、结构、安装工艺及运行状态进行全面评估的过程,旨在发现潜在缺陷、预防泄漏事故并延长管道使用寿命。尤其在石油化工、天然气输送、城市供水供热等领域,定期开展管道质量检测已成为保障安全生产和满足环保法规要求的必要措施。
核心检测项目与技术手段
1. 材料性能检测
通过光谱分析、金相试验和力学性能测试,验证管道材料的化学成分、显微组织和抗拉强度是否符合设计标准,确保材料在服役环境下的耐久性。
2. 几何尺寸测量
使用激光扫描仪、超声波测厚仪等设备,精确检测管道直径、壁厚、椭圆度等参数,评估加工精度和材料损耗情况,避免因尺寸偏差导致的承压能力下降。
3. 焊缝无损检测
采用射线探伤(RT)、超声波探伤(UT)、磁粉检测(MT)和渗透检测(PT)四大常规方法,结合相控阵超声(PAUT)等齐全技术,对焊接区域进行多维度缺陷筛查。
4. 防腐层完整性评估
通过电火花检漏仪检测涂层针孔,配合剥离强度试验和阴极保护电位测量,系统评价防腐体系的有效性,防止电化学腐蚀导致的管体损伤。
5. 压力管道强度试验
执行水压试验或气压试验,验证管道系统在1.5倍设计压力下的密封性能和结构稳定性,确保无渗漏、无塑性变形等异常现象。
智能化检测技术发展趋势
随着工业4.0技术的发展,管道检测正向着自动化、数字化方向演进。智能爬行机器人搭载高清摄像头和传感器,可进入管道内部进行360°全景检测;基于大数据分析的腐蚀预测系统能提前预警高风险管段;分布式光纤传感技术则实现了长输管道的实时应力监测。这些创新手段显著提升了检测效率和数据可靠性。
检测标准与质量控制要点
检测过程需严格遵循GB/T 20801《压力管道规范》、API 570《管道检验规范》等标准要求。重点控制检测设备校准、环境参数记录、缺陷判定阈值设定等关键环节,确保检测报告具有法律效力和工程指导价值。对于发现的三级以上缺陷,必须建立完整的追踪处理机制,直至完成修复验证。
结语
管道质量检测是预防重大事故的第一道防线,需要融合多学科技术形成完整的检测体系。随着新材料应用和服役环境复杂化,检测机构应持续更新技术装备,培养专业人才,为推动管道工程高质量发展提供坚实保障。
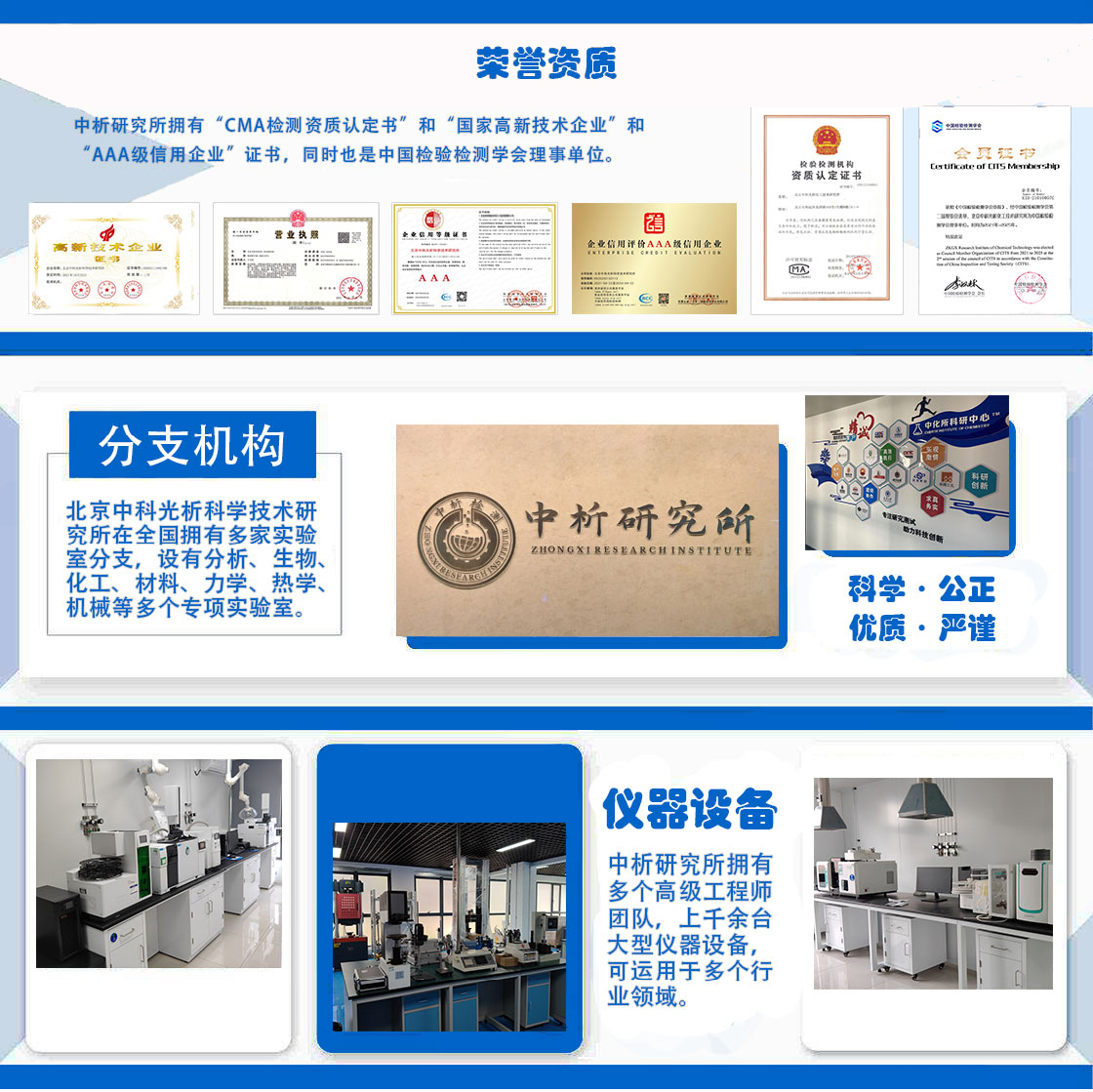
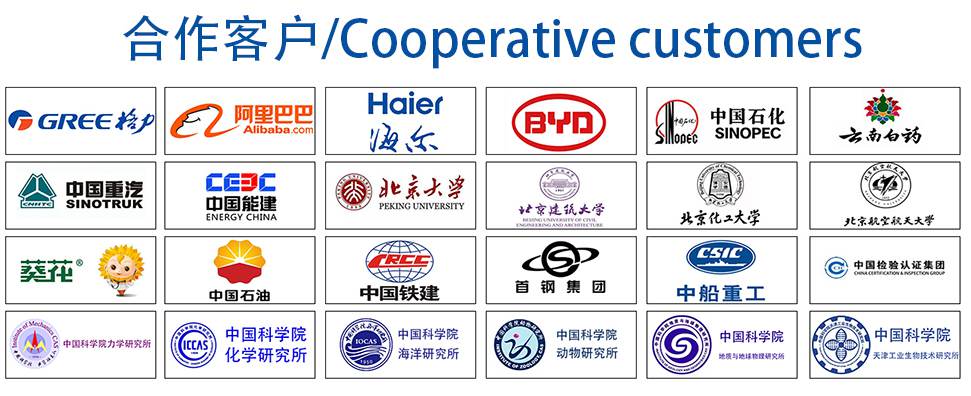