法兰封闭器检测项目及技术要求
法兰封闭器作为管道系统中关键的密封组件,其性能直接影响工业设备的运行安全与介质防泄漏能力。在石油化工、能源输送、制药等领域,法兰封闭器的失效可能导致严重的安全事故或环境污染。因此,建立系统化的法兰封闭器检测体系成为设备维护工作的核心环节。完整的检测流程需涵盖材料性能、密封形态、力学强度等维度,并参照GB/T 9124、ASME B16.5等国内外标准执行。
一、外观与尺寸检测
通过目视检查和三维测量仪对法兰封闭器进行基础评估:
1. 表面是否存在裂纹、凹痕、腐蚀等缺陷
2. 密封面粗糙度是否满足Ra≤3.2μm要求
3. 法兰孔径与螺栓孔同心度误差是否≤0.1mm
4. 密封槽深度、宽度与设计图纸的偏差是否在±0.05mm范围内
二、密封性能测试
采用水压试验与氦质谱检漏双重验证:
1. 1.5倍工作压力下保压30分钟,压降不超过5%
2. 使用氦气作为示踪气体检测泄漏率,标准泄漏量需≤1×10⁻⁶Pa·m³/s
3. 高温工况模拟测试(200℃±5℃)密封材料热稳定性
三、材料特性分析
通过理化实验室检测确保材质合规:
1. 光谱分析验证不锈钢材料的Cr/Ni/Mo元素含量
2. 布氏硬度检测(HB180-220区间)
3. 金相显微镜观察晶粒度(6-8级为合格)
4. 应力腐蚀试验(42%MgCl₂溶液,沸腾状态持续720小时无裂纹)
四、动态循环测试
模拟实际工况进行疲劳评估:
1. 交变压力测试(0-1.6MPa循环5000次)
2. 热循环试验(-20℃至150℃交替冲击100次)
3. 振动台测试(频率10-200Hz,加速度5g持续8小时)
五、无损检测
应用齐全检测技术排查隐蔽缺陷:
1. 超声波探伤(UT)检测内部气孔、夹杂物
2. 磁粉检测(MT)检查表面及近表面裂纹
3. 渗透检测(PT)验证密封面微渗漏通道
4. X射线成像(CR)分析焊接接头完整性
完整的检测报告应包含原始数据记录、缺陷分布图及整改建议。对于检测不合格的法兰封闭器,需进行失效分析并建立纠正预防措施数据库。建议每12个月或设备大修期间开展系统性检测,确保密封系统全生命周期可靠性。
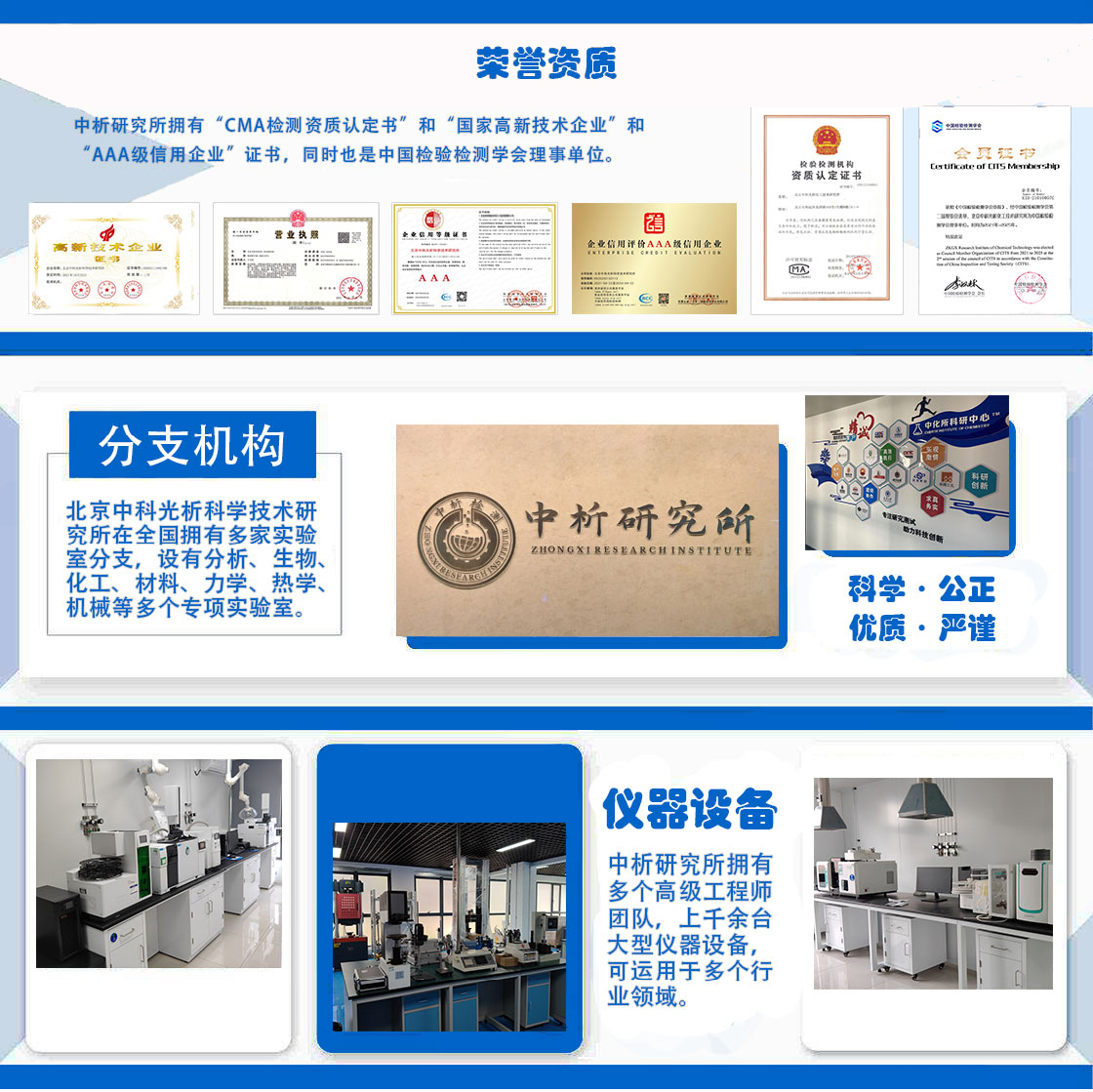
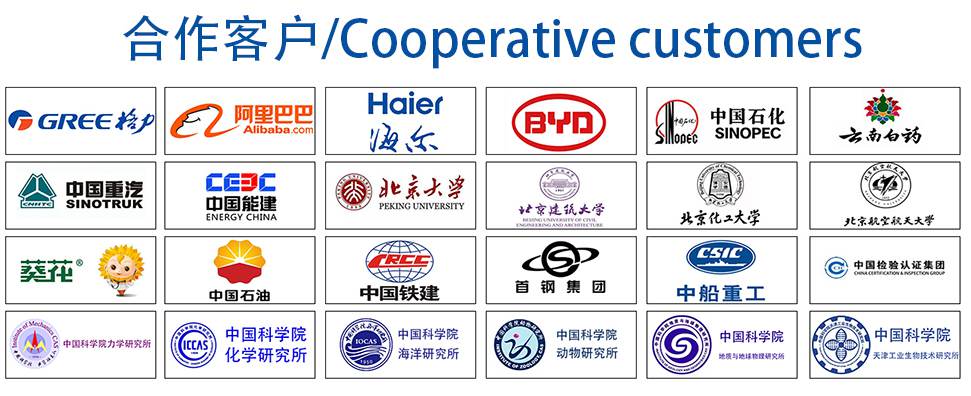