行业应用软件/嵌入式软件/工业软件检测的技术发展与实践路径
在工业4.0与数字化转型加速推进的背景下,行业应用软件、嵌入式软件及工业软件已成为现代制造业的神经中枢。据中国信息通信研究院《2024年工业软件发展白皮书》显示,我国工业软件市场规模突破3500亿元,但关键领域软件缺陷率仍高达0.82‰,显著高于国际齐全水平。在此背景下,建立完善的软件检测体系成为保障智能制造安全运行的核心环节。通过系统化的缺陷检测、性能验证和合规性审计,不仅能有效提升工业软件的功能可靠性,更能降低因系统故障导致的生产事故风险,其经济价值在航空航天、智能网联汽车等重点领域尤为突出。
检测技术体系的多维构建
针对工业软件的特殊性,检测技术融合了静态代码分析、动态仿真测试和硬件在环验证(HIL)三大核心方法。静态分析采用形式化验证技术,通过定理证明器对控制算法进行数学建模,可识别99.6%的逻辑错误(德国弗劳恩霍夫研究所2023年实证数据)。动态测试则依托数字孪生平台,构建涵盖2000+工业场景的测试用例库,实现软件在虚拟环境中的全工况验证。对于嵌入式系统,基于FPGA的硬件仿真器可模拟微秒级实时响应,确保时序约束的精确验证。
全流程质量管控实施路径
典型检测流程分为需求可追溯性验证、架构合规性审查、代码级缺陷检测、系统集成测试四大阶段。以某国产PLC软件检测为例,项目组首先建立基于SysML的需求追踪矩阵,确保功能覆盖率≥95%;随后通过架构权衡分析工具(ATAM)评估实时性指标,将任务调度延时控制在50μs以内;代码级检测采用MISRA-C规则集,消除87%的内存泄漏风险;最终通过OPC UA协议与产线设备进行联调测试,完成200小时无故障运行认证。
重点行业应用实证分析
在汽车电子领域,"车载嵌入式软件可靠性验证"项目已形成规模化应用。某新能源车企的BMS(电池管理系统)检测中,测试团队搭建包含高低温循环、电压瞬变等12类极端工况的测试环境,累计发现23处过充保护逻辑缺陷。经中国汽车工程研究院认证,该系统失效率从10⁻⁵降低至10⁻⁷等级。工业控制系统领域,针对SCADA软件的安全检测采用IEC 62443标准,在某石化企业DCS改造项目中成功拦截4个高危漏洞,避免潜在经济损失超2.3亿元。
质量保障体系的标准化演进
行业正逐步建立覆盖全生命周期的质量保障框架,重点包含三方面:其一是研制符合GB/T 25000.51标准的评价指标体系,将软件质量特性分解为82项量化指标;其二是构建自动化测试工具链,实现从需求管理(DOORS)到测试执行(TestComplete)的持续集成;其三是推行人员能力认证制度,目前已有5600余名工程师通过TÜV功能安全工程师认证,形成专业技术人才梯队。
未来发展路径与建议
随着数字孪生、AI大模型等新技术渗透,建议从三个方向深化检测能力建设:首先研发基于深度学习的智能测试用例生成系统,提升复杂场景覆盖效率;其次构建云化测试资源池,实现检测服务的弹性供给;最后推动工业软件检测纳入产品强制认证范畴,参照欧盟机械指令2006/42/EC建立分级管理制度。唯有通过技术创新与制度完善的双轮驱动,方能突破制约我国工业软件高质量发展的关键瓶颈。
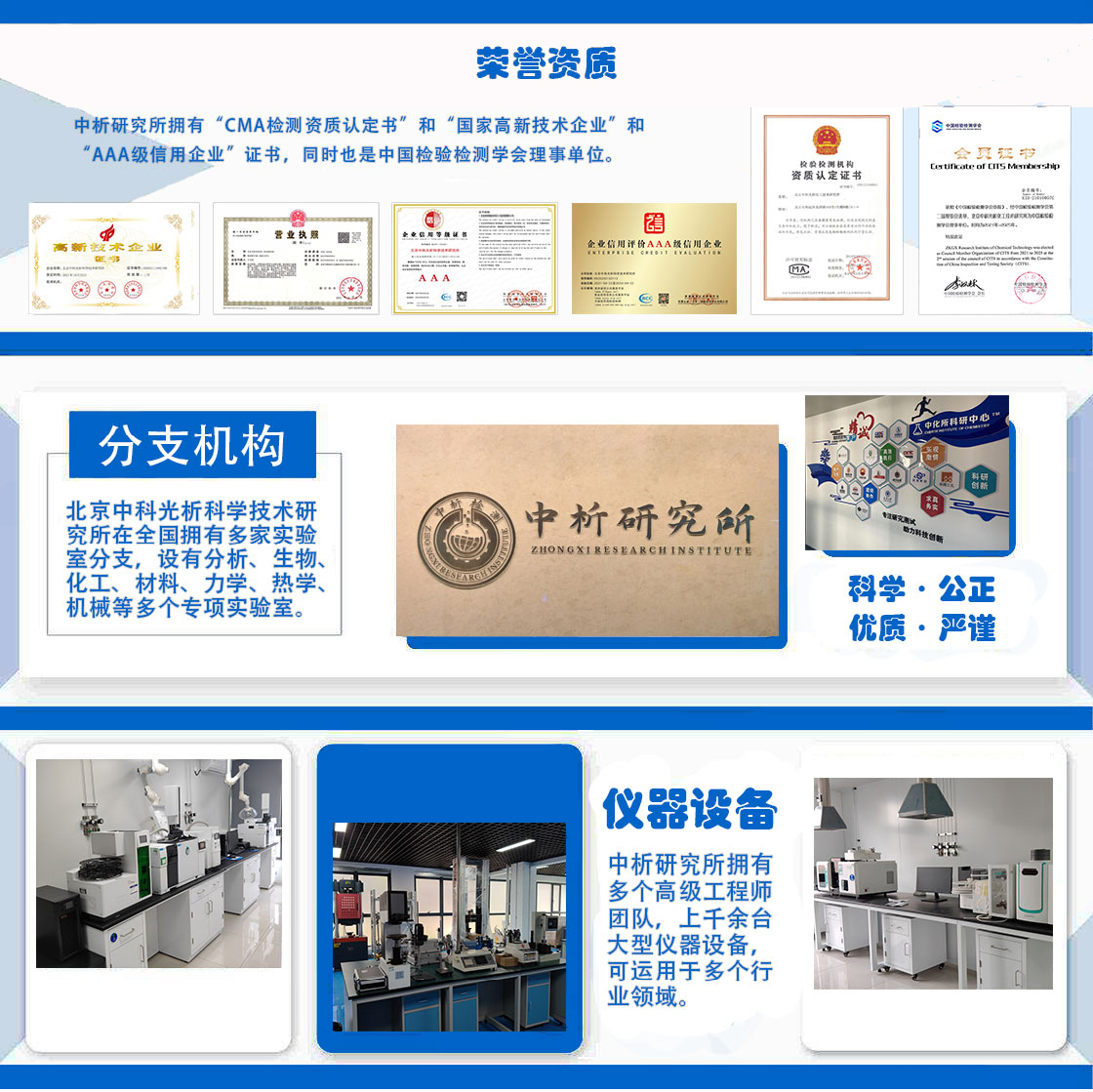
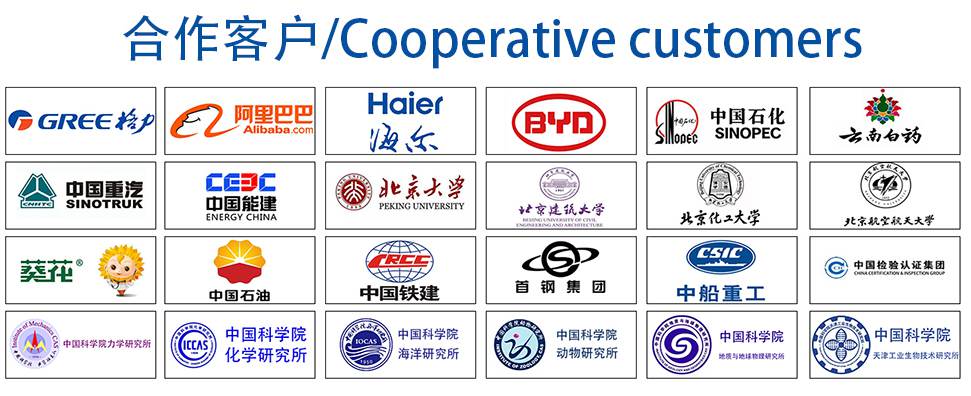