机体与气缸盖检测的重要性
机体与气缸盖作为内燃机核心部件,其性能直接影响发动机的动力输出、密封性及使用寿命。机体承担着支撑曲轴、活塞等运动件的功能,而气缸盖则与机体共同形成燃烧室,并承担气门机构的安装任务。在长期高负荷运转中,机体可能因热应力产生变形,气缸盖易出现裂纹或烧蚀,因此系统化的检测项目对于预防故障、保障设备安全运行具有不可替代的作用。专业检测不仅能发现潜在缺陷,还能为维修方案制定提供数据支持,避免因部件失效导致的连锁性机械故障。
主要检测项目分类
1. 外观缺陷检测
通过目视检查与精密仪器结合,重点排查: • 裂纹:使用渗透检测(PT)或磁粉探伤(MT)定位表面及近表面裂纹 • 腐蚀:评估水道、油道区域的锈蚀程度及分布特征 • 变形:采用激光平面度仪测量接合面平面度误差(通常要求≤0.05mm/m) • 烧蚀痕迹:检查燃烧室周边是否存在局部熔损现象
2. 尺寸精度验证
运用三坐标测量系统(CMM)进行全尺寸检测: • 气缸孔圆度/圆柱度(标准值一般≤0.015mm) • 主轴承座孔的同轴度偏差(需控制在0.02mm以内) • 缸盖螺栓孔位置精度(误差不超过±0.1mm) • 气门导管安装孔垂直度(允许偏差<0.05°)
3. 密封性能测试
采用分级加压法进行验证: • 水套密封性:加压至0.5-0.7MPa保压10分钟,压降不超过5% • 燃烧室密封:通过气压试验检测气门座圈与导管配合状态 • 油道通畅性:使用流量计测量各油路流量均衡性
4. 材料性能分析
通过无损检测手段评估材料状态: • 硬度检测(布氏硬度计测量,铸铁机体典型值180-220HB) • 金相组织观察(检查石墨形态及珠光体含量) • 超声波测厚(关键部位壁厚偏差需<设计值的5%)
5. 装配配合检测
重点验证部件间配合关系: • 气缸垫压缩量测试(使用塑性测量丝检测) • 缸盖螺栓预紧力验证(需采用扭矩-转角法精确控制) • 气缸套凸出量测量(通常规范值为0.03-0.10mm)
检测流程标准化要求
规范化的检测流程应包含:预处理清洁→基准面校准→分阶段检测→数据记录分析→结果判定五个步骤。特别需注意:检测环境需控制温度在20±2℃以消除热变形影响,对铝合金气缸盖应额外进行时效处理后的复检。所有检测数据需形成三维质量分布图,为维修决策提供可视化依据。
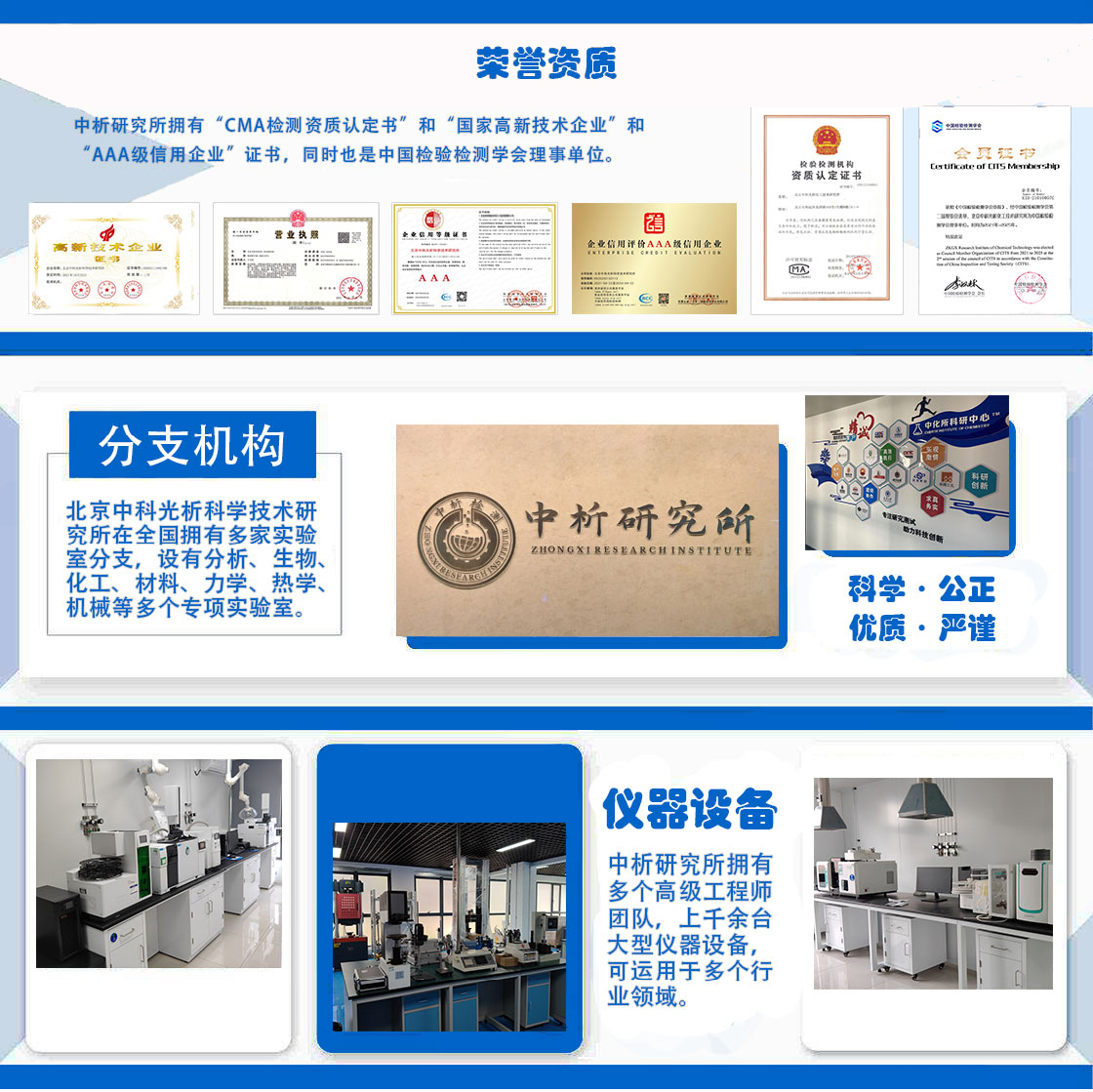
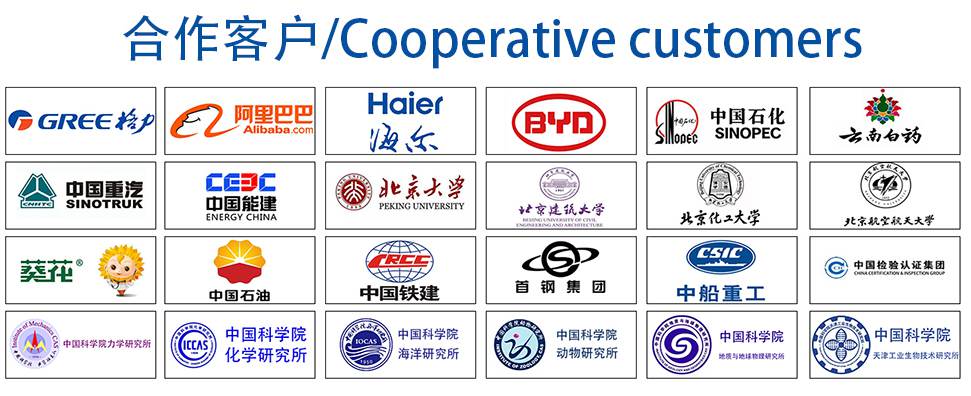