工业环境中的产品检测:保障质量的核心环节
在现代工业生产中,产品检测是贯穿制造全流程的关键环节。随着市场竞争加剧和消费者对品质要求的提升,工业环境中的检测项目已从传统的目视检查发展为融合多种齐全技术的系统性工程。无论是汽车零部件、电子元件还是食品包装,企业需要通过科学的检测体系确保产品符合国家标准、行业规范及客户需求。这一过程不仅关乎企业声誉,更直接影响生产安全、成本控制和市场竞争力。
核心检测项目分类与应用
工业环境中的检测项目可细化为物理性能检测、化学特性分析、功能性验证三大类别。其中物理性能检测包含尺寸精度测量(如三坐标测量仪)、表面粗糙度测试、抗压/抗拉强度试验等;化学特性分析则涉及材料成分检测(如光谱分析)、重金属含量测定以及防腐涂层附着力测试;功能性验证重点关注产品在模拟使用环境下的表现,例如电子产品的高低温循环测试、汽车部件的振动疲劳试验等。
智能化检测技术的突破
近年来,机器视觉与人工智能的融合正在革新传统检测模式。基于深度学习的缺陷识别系统可实时分析产品表面0.01mm级别的划痕或色差,准确率可达99.8%。例如在半导体晶圆检测中,AOI(自动光学检测)设备能以每分钟3000张图像的速度完成微米级缺陷筛查,较人工效率提升20倍以上。同时,工业CT扫描技术实现了产品内部结构的无损检测,在航空航天铸件质量控制中发挥重要作用。
全流程质量监控体系构建
完整的检测体系需贯穿原材料入库、生产过程监控到成品出厂全链路。统计过程控制(SPC)系统通过实时采集生产数据建立动态质量模型,当检测数据超出控制线时自动触发预警。以汽车制造业为例,整车厂要求供应商执行PPAP(生产件批准程序),包含2D/3D尺寸报告、材料证明书等18项检测文档,确保零部件批次一致性。
标准化与定制化检测方案并行
虽然ISO 9001、IATF 16949等国际标准为检测流程提供基础框架,但不同行业需制定针对性方案。食品行业需严格执行微生物检测(如菌落总数、大肠杆菌检测),而医疗设备则必须通过生物相容性测试(ISO 10993标准)。某医疗器械企业通过引入X射线检测设备,使骨科植入物的孔隙率检测时间从8小时缩短至15分钟,缺陷检出率提升至99.95%。
在工业4.0背景下,产品检测正朝着智能化、网络化方向发展。通过整合MES系统、物联网传感器和大数据分析,企业可构建预测性质量管理系统。未来,基于数字孪生技术的虚拟检测将实现产品性能的跨物理空间验证,为工业制造开辟全新的质量保障维度。
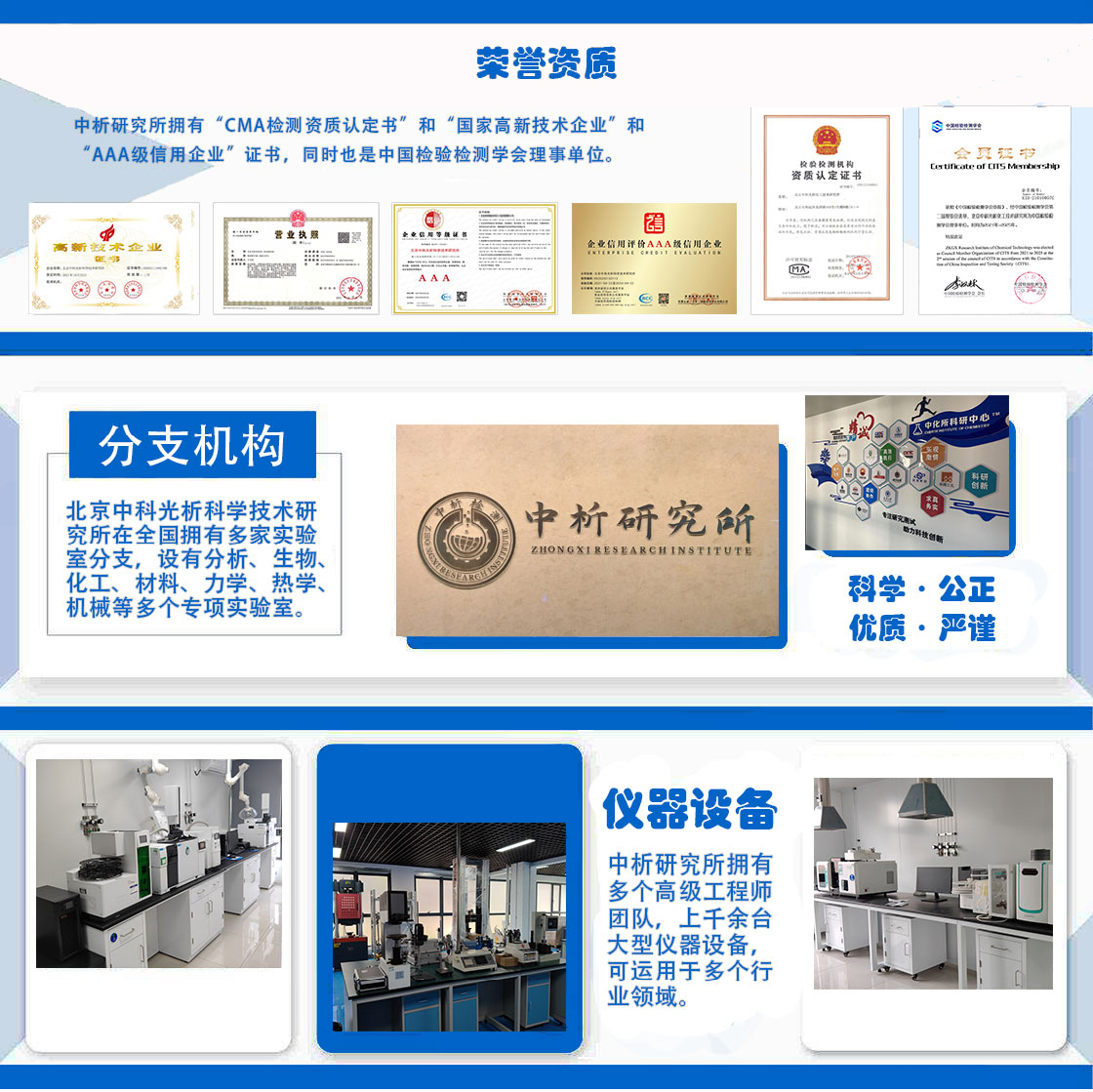
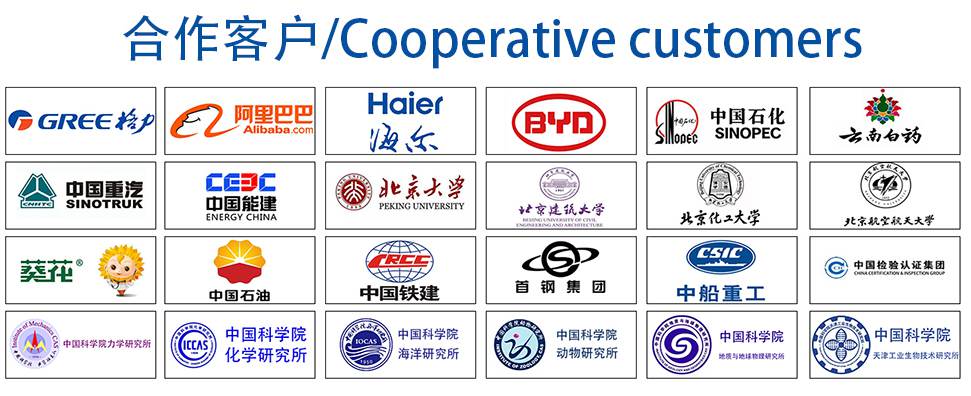