铝及铝合金管材检测的重要性
铝及铝合金管材因其轻量化、耐腐蚀、导热性好等特性,广泛应用于建筑、航空航天、汽车制造、电力设备及化工管道等领域。然而,其性能与质量直接影响工程安全和使用寿命,因此必须通过科学严谨的检测手段确保材料符合国家标准(如GB/T 4437、GB/T 6893)及行业规范。检测项目覆盖化学成分、力学性能、尺寸精度、表面质量及耐腐蚀性等多个维度,旨在全面评估材料的可靠性与适用性。
核心检测项目解析
1. 化学成分分析
铝合金的性能与其元素配比密切相关。通过光谱分析仪(如ICP-OES)检测铝(Al)、镁(Mg)、硅(Si)、铜(Cu)等主要元素及杂质元素含量,确保材料符合牌号要求(如6061、6063、5083等)。例如,镁含量过高可能导致脆性增加,而硅含量不足则影响强度。
2. 力学性能测试
力学性能是管材适用性的核心指标,包括:
- 拉伸试验:测定抗拉强度(Rm)、屈服强度(Rp0.2)及断后伸长率(A),验证材料在受力时的变形与断裂特性;
- 硬度测试:采用布氏(HBW)或韦氏(HW)硬度计评估材料抗局部变形能力;
- 弯曲试验:通过压弯或三点弯曲法检验管材塑性变形性能。
3. 尺寸与几何精度检测
使用高精度量具(如千分尺、激光测径仪)测量管材的外径、壁厚、椭圆度及直线度。例如,根据GB/T 4437标准,外径公差需控制在±0.5%以内,壁厚偏差不超过±10%。超标可能导致安装困难或结构强度下降。
4. 表面质量与耐腐蚀性评估
通过目视检查、显微镜观测及电化学测试,检测表面裂纹、划痕、氧化膜完整性等缺陷。盐雾试验(如GB/T 10125)模拟严苛环境,评估阳极氧化或涂层处理的耐腐蚀能力,确保管材在海洋或工业大气中的长期稳定性。
5. 无损检测(NDT)
针对内部缺陷,采用超声波检测(UT)定位气孔、夹杂物等体积型缺陷,涡流检测(ET)识别表面及近表面裂纹。此外,X射线成像可直观显示焊缝质量,避免因内部缺陷引发的安全隐患。
检测流程与标准选择
检测需遵循“抽样-预处理-项目测试-数据分析-报告生成”流程,根据应用场景选用GB、ASTM、ISO等标准。例如,航空航天领域常采用AMS 2772规范,而建筑用管材需满足EN 755系列要求。专业机构需配备CMA/ 资质,确保结果权威性。
结语
铝及铝合金管材检测是保障材料性能与安全的关键环节,需结合多维度数据综合判定质量等级。企业应选择具备完善检测能力与认证资质的实验室,同时关注材料加工工艺与检测结果的关联性,实现从生产到应用的全生命周期质量管理。
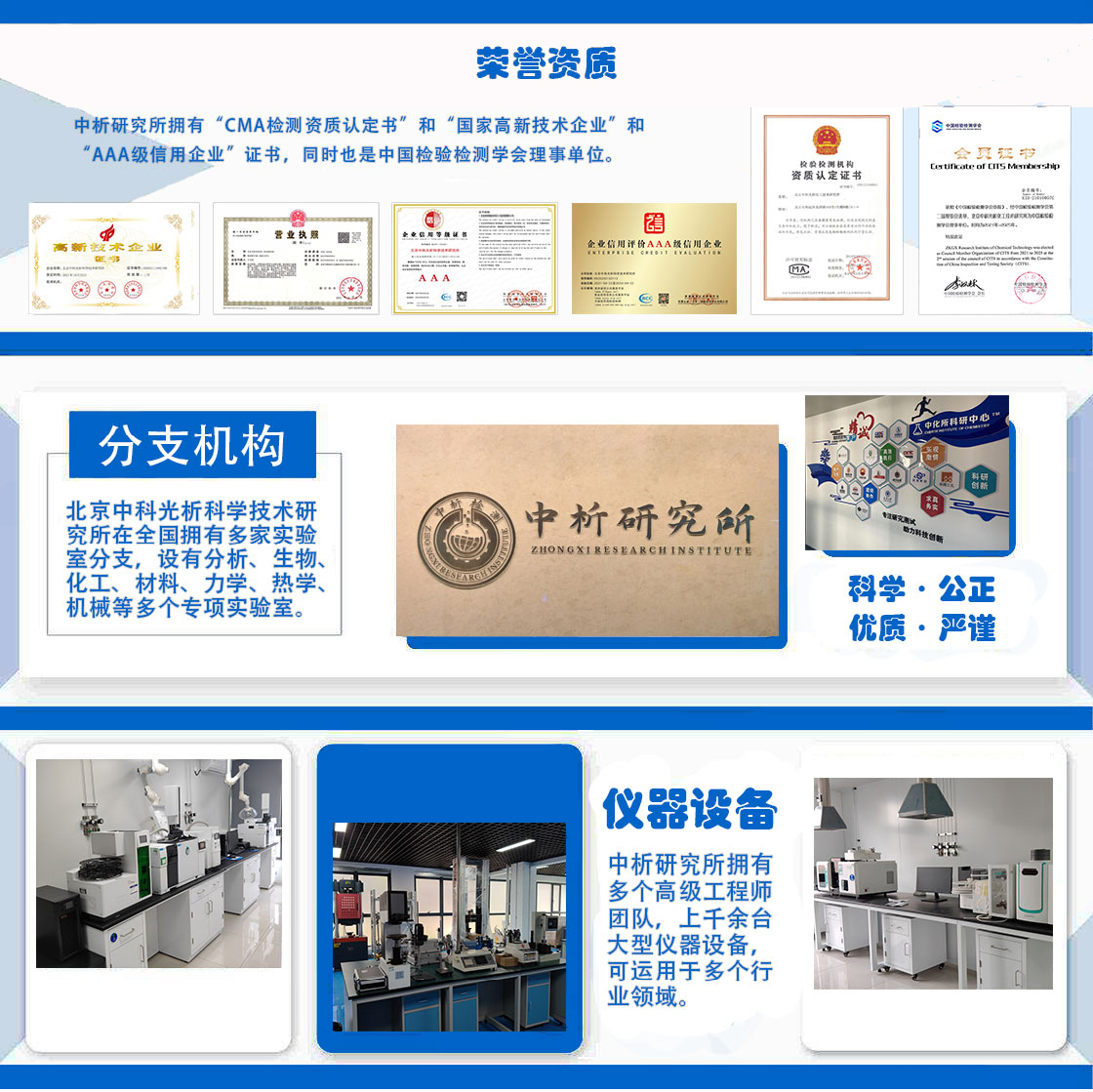
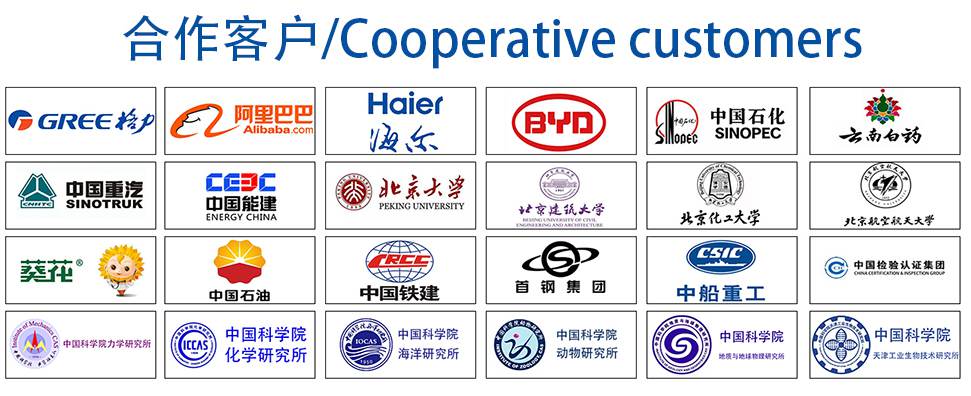