钢丝绳用润滑脂作为保障钢丝绳使用寿命和安全性的关键材料,其性能直接影响设备的运行效率及维护成本。在矿山、港口、电梯、起重机械等应用场景中,钢丝长期承受高负荷、摩擦、腐蚀等复杂工况,润滑脂需兼具润滑、防锈、抗氧化、抗水淋等多重功能。若润滑脂质量不达标或性能劣化,可能导致钢丝绳内部磨损加剧、断丝风险增加,甚至引发安全事故。因此,对润滑脂进行系统性检测是设备管理的重要环节。
一、润滑脂基础性能检测
检测项目包括锥入度、粘度、滴点等核心指标。锥入度反映润滑脂的软硬程度,通过ASTM D217标准测试,直接影响涂敷效果;粘度测定采用旋转黏度计,确保润滑脂在动态工况下的附着能力;滴点测试(GB/T 4929)则评估润滑脂高温稳定性,若滴点低于使用环境温度,会导致润滑脂流失失效。
二、防锈与防腐性能测试
通过湿热试验(GB/T 2361)、盐雾试验(ISO 9227)模拟恶劣环境,检测润滑脂对钢丝表面的保护能力。重点观察试验后钢丝表面锈蚀面积及颜色变化,防锈等级需达到1级(无可见锈斑)方可满足长期防护需求。
三、氧化安定性分析
采用压力差示扫描量热法(PDSC)或烘箱法(ASTM D942),评估润滑脂在高温下的抗氧化能力。氧化后酸值升高超过0.5mgKOH/g或锥入度变化率>20%,表明润滑脂已发生明显劣化,需及时更换。
四、抗水淋特性验证
依据SH/T 0109标准进行水淋试验,将涂脂试样置于38℃水流冲击1小时,计算润滑脂流失率。优质润滑脂流失率应<5%,确保在潮湿环境中维持有效润滑膜。
五、机械安定性检测
使用十万次剪切试验(GB/T 269),模拟钢丝绳反复弯折工况。测试后锥入度变化值若超过30个单位,说明润滑脂结构破坏严重,无法保持稳定润滑状态。
六、有害物质及环保指标
检测多环芳烃(PAHs)、重金属(铅、镉)等有害物质含量,符合欧盟REACH法规及ROHS指令要求。同时测定生物降解率,港口、海洋工程用润滑脂需达到>60%的可降解标准。
通过上述检测项目的系统化实施,可全面评估钢丝绳润滑脂的综合性能。建议每批次进货进行全项检测,使用中每6个月开展关键指标复测,结合设备实际工况动态调整检测频率,从而最大限度延长钢丝绳使用寿命,规避运行风险。
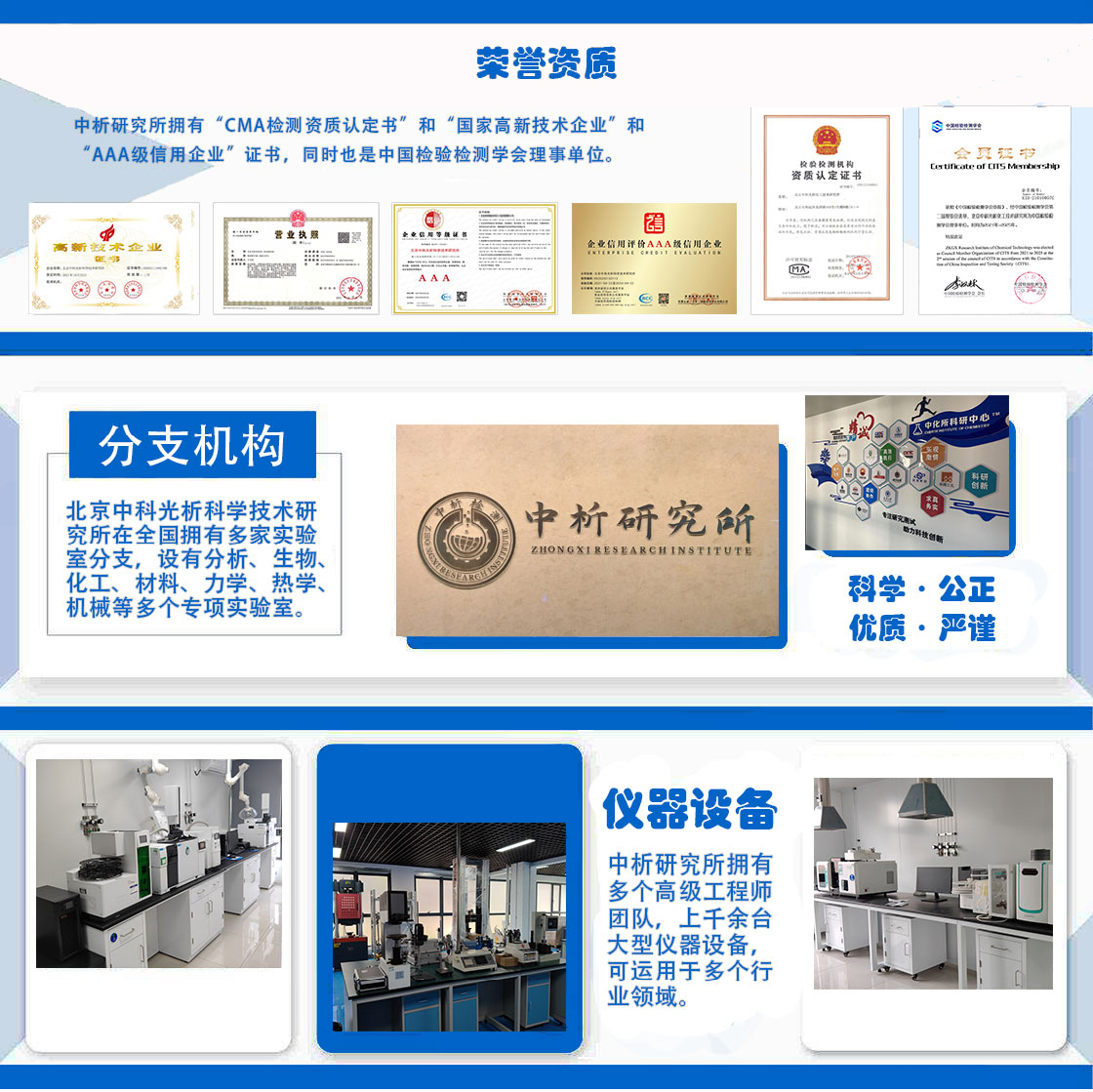
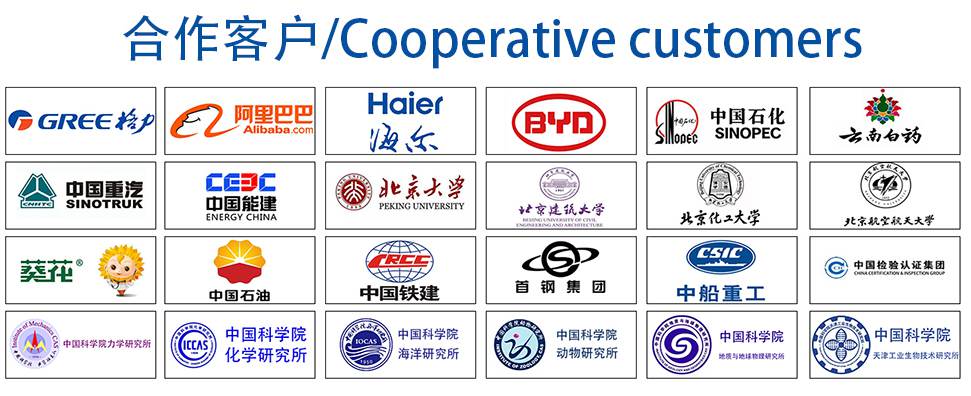