工业锅炉节能监测检测的重要性与实施要点
工业锅炉作为工业生产中能源消耗的核心设备,其能效水平直接关系到企业运营成本和碳排放量。随着“双碳”目标的推进及《工业锅炉节能环保技术规范》等政策的实施,开展系统化、标准化的节能监测检测已成为企业实现绿色转型的关键措施。通过科学的检测手段,能够精准识别锅炉运行中的能量损失点,优化燃烧效率、降低燃料消耗,同时减少污染物排放。本文将从核心检测项目出发,全面解析工业锅炉节能监测的实施框架与技术要点。
一、热效率测试
热效率是衡量锅炉能源利用率的首要指标,检测时需依据GB/T 10180《工业锅炉热工性能试验规程》,通过正平衡法或反平衡法进行测算。重点监测燃料低位发热量、蒸汽/热水输出量、排烟温度等参数,并结合灰渣含碳量、不完全燃烧热损失等数据,综合计算实际热效率。若热效率低于额定值的85%,需对燃烧器、受热面清洁度及保温层性能进行排查。
二、排烟温度与过量空气系数检测
排烟温度过高(通常超过160℃)会导致显著的热能浪费,需使用红外测温仪或热电偶进行实时监测。同时,通过烟气分析仪测定排烟处的氧含量(O₂)和一氧化碳(CO)浓度,计算过量空气系数。合理范围应控制在1.1-1.3之间,数值过高表明漏风或配风不合理,过低则可能引发不完全燃烧。
三、辅机设备电耗监测
鼓风机、引风机、水泵等辅机设备的电能消耗占总能耗的15%-30%。需采用电能质量分析仪记录其运行功率、电流及功率因数,结合负荷率评估设备匹配度。例如,风机实际功率若长期低于额定功率的60%,建议加装变频调速装置,节电率可达20%-40%。
四、炉体表面散热损失检测
使用热成像仪对锅炉炉墙、管道、阀门等部位进行扫描,表面温度不应超过环境温度25℃(GB 24500规定)。重点排查保温层破损、法兰连接处漏热等问题。实测数据显示,保温层厚度不足设计值的80%时,散热损失将增加1.5倍以上。
五、水质管理与排污率控制
定期检测给水硬度、pH值及溶解氧含量,确保符合GB/T 1576《工业锅炉水质》标准。高硬度水质会导致结垢,使传热效率下降8%-12%。同时,监测连续排污率和定期排污频次,建议通过安装自动排污控制系统将排污率控制在≤5%的范围内。
六、烟气成分与环保指标监测
采用在线监测系统(CEMS)实时采集SO₂、NOx、颗粒物浓度,比对GB 13271《锅炉大气污染物排放标准》限值。对燃烧调整后仍超标的情况,需评估脱硫脱硝设备运行状态。数据表明,优化空燃比可使NOx排放降低20%-30%。
结语:工业锅炉节能检测需建立常态化机制,结合智能化监测平台实现数据动态分析。企业每年至少开展1次全面检测,并根据负荷变化进行阶段性抽检。通过多维度的数据诊断与技术改造,可提升锅炉系统能效5%-15%,显著降低综合运营成本。
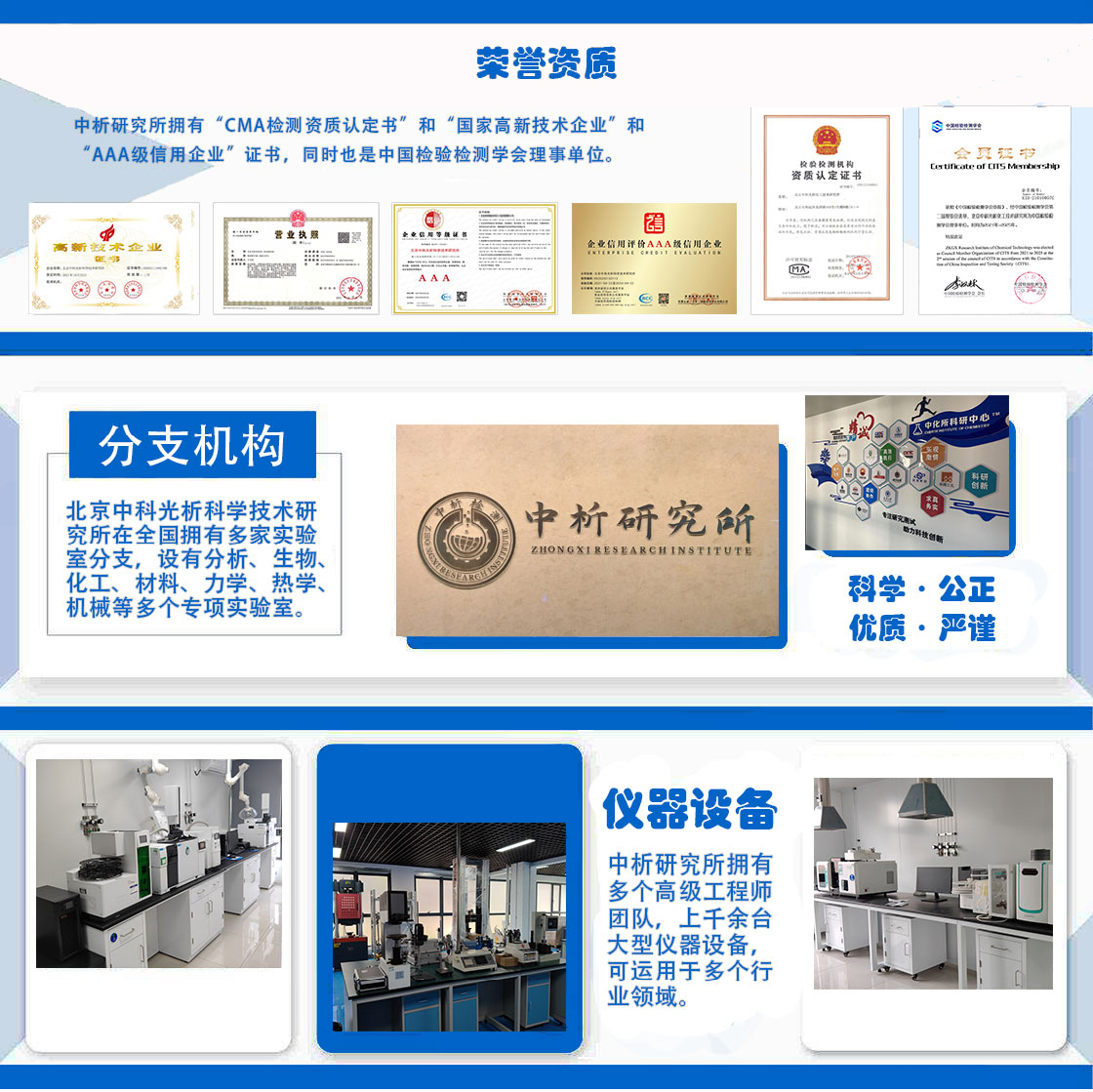
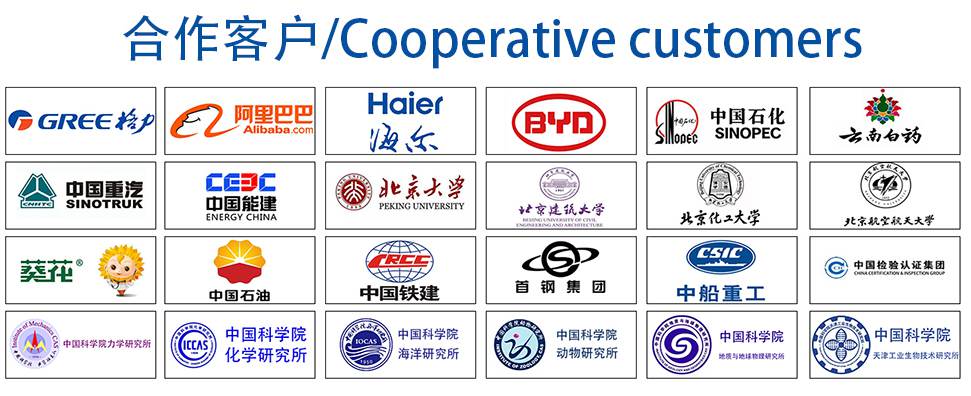