钛及钛合金无缝管检测的核心价值与应用领域
钛及钛合金无缝管因其高强度、耐腐蚀、轻量化等优异性能,被广泛应用于航空航天、石油化工、医疗植入器械、海洋工程等高端领域。这些场景对材料的质量要求极为严苛,任何微小的缺陷或成分偏差都可能导致设备失效甚至重大事故。为此,针对钛及钛合金无缝管的系统性检测成为确保其性能稳定性和使用安全性的核心环节。通过科学的检测手段,可精准验证材料是否符合GB/T 3624-2010《钛及钛合金无缝管》等国家标准以及ASTM B338等国际规范要求,同时为生产工艺优化提供数据支撑。
关键检测项目与技术解析
1. 化学成分分析
采用电感耦合等离子体发射光谱(ICP-OES)、X射线荧光光谱(XRF)等仪器,检测钛基体中铝、钒、铁、氧等元素的含量,确保合金成分满足TA1、TA2、TC4等牌号的技术指标要求,避免杂质元素超标导致的晶间腐蚀风险。
2. 力学性能测试
通过万能试验机完成抗拉强度(≥895MPa)、屈服强度(≥825MPa)和延伸率(≥10%)测试,验证管材在极端载荷下的形变能力;借助维氏硬度计(HV)和夏比冲击试验机,评估材料硬度(通常HV≥320)及低温韧性(-196℃冲击吸收功≥34J)。
3. 无损检测(NDT)
综合运用超声波探伤(UT)检测内部裂纹、气孔等缺陷(灵敏度≤Φ1.6mm平底孔),涡流探伤(ET)检测表面微裂纹,液体渗透检测(PT)识别开口缺陷,以及X射线实时成像(DR)对焊缝和热影响区进行三维缺陷定位。
4. 几何尺寸与表面质量检测
使用激光测径仪测量外径公差(±0.15mm),内窥镜检测内壁光洁度(Ra≤1.6μm),金相显微镜观察晶粒度(ASTM E112标准6-8级),同时通过目视和涂层测厚仪验证表面氧化层厚度(2-5μm)及是否存在划痕、褶皱等表观缺陷。
5. 耐腐蚀性验证
通过盐雾试验(5% NaCl溶液,35℃持续720小时)、酸碱浸泡试验(10% HCl、40% NaOH溶液,80℃下24小时)等方法评估耐蚀性,配合电化学工作站测定自腐蚀电位(Ecorr≥-0.25V)和点蚀击穿电位(Eb≥1.0V),确保在海洋大气或强腐蚀介质中的长期稳定性。
全流程质量控制的意义
完整的检测体系需贯穿从原料熔炼到成品出厂的全生命周期:熔炼阶段监控铸锭成分均匀性,热挤压过程控制β相转变温度(TC4合金约995℃),冷轧工序跟踪加工硬化率,热处理后检测相组成(α+β双相组织占比),最终通过爆破试验(1.5倍工作压力保压30秒)验证承压能力。只有严格执行各环节检测标准,才能确保钛管在超临界机组、舰船冷凝器等高压高温场景下的可靠性。
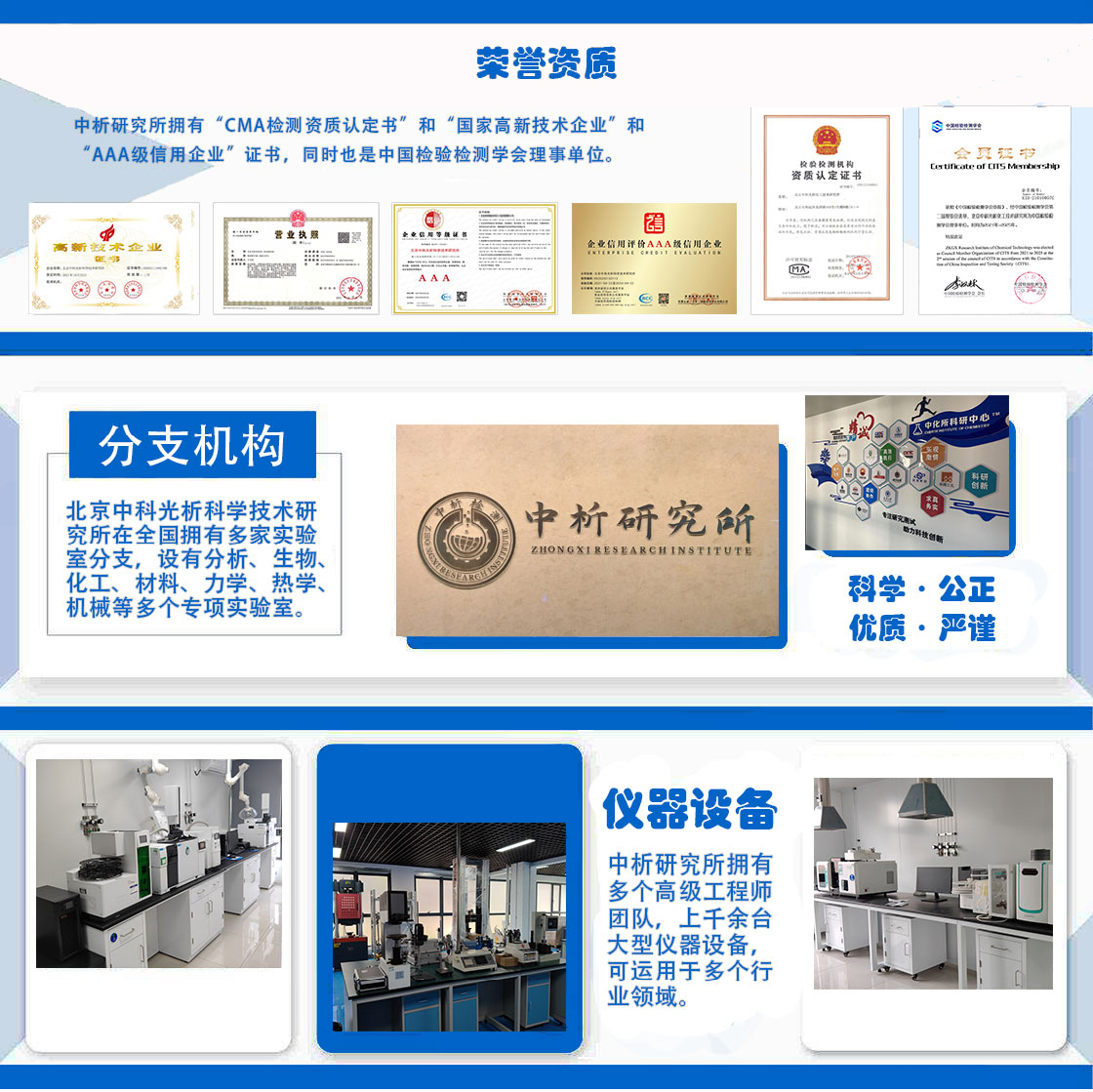
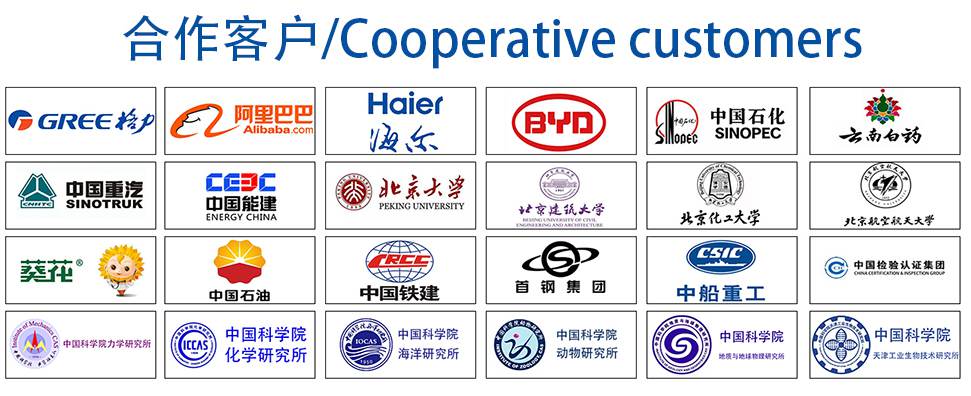