钻井用化学剂检测:确保油气勘探安全与效率的核心环节
在石油与天然气勘探开发过程中,钻井用化学剂作为钻井液的核心构成部分,直接影响钻井作业的安全性、效率及环境保护水平。从抑制井壁坍塌的页岩抑制剂到调整流变性的增粘剂,从降低摩擦阻力的润滑剂到控制储层损害的暂堵剂,各类化学剂需经过严格检测才能投入现场应用。随着油气勘探向深井、超深井及复杂地层拓展,钻井化学剂的性能检测已发展为包含物理化学分析、功能性验证、环境评价等多维度的系统化检测体系,涉及超过30项关键技术指标。
一、基础理化性能检测
该检测层级涵盖化学剂的本质特性验证,包括酸碱度(pH值)测试(ASTM E70标准)、密度测定(GB/T 1884)、粘度特性分析(旋转粘度计测试)、固相含量检测(高温烘箱法)及热稳定性实验(高温老化测试)。其中,抗温性能检测需模拟井下高温环境(最高可达260℃),通过热滚实验评价化学剂的热分解特性。
二、功能性应用检测
针对化学剂在钻井工程中的具体功能开展专项测试:
- 润滑性测试:采用极压润滑仪测定摩擦系数降低率(API RP 13B-1标准)
- 滤失控制检测:通过HTTP滤失仪在高温高压条件下测定滤失量
- 页岩抑制性评价:使用线性膨胀仪测定泥页岩水化膨胀抑制率
- 储层保护测试:借助岩心流动实验评价渗透率恢复值
三、环境安全检测
依据国际环保法规(如OSPAR公约)及国家标准,重点开展:
- 生物毒性测试:采用发光细菌法(ISO 11348-3)或鱼类急性毒性试验
- 生物降解性分析:根据OECD 301标准进行28天生物降解率测定
- 重金属含量检测:ICP-MS法测定铅、汞、镉等重金属元素
- 陆域/海洋排放评估:模拟不同环境条件下的降解行为及生态影响
四、质量控制与合规性验证
生产企业需建立从原料检验到成品放行的全过程质量管控:
- 原材料入厂检验:包括有效成分滴定、杂质谱分析(HPLC)
- 批次稳定性测试:加速老化实验验证产品保质期
- 混合配伍性检测:评价不同化学剂间的协同/拮抗效应
- 标准符合性验证:对照API 13A、SY/T 5504等行业标准进行符合性认证
随着智能化检测技术的发展,基于机器视觉的自动粘度测量、采用微流控芯片的快速毒性筛查等创新方法正在逐步取代传统检测手段。第三方检测机构认证(如 、CMA)已成为产品质量国际认可的必要条件,检测周期从常规的5-7个工作日缩短至紧急检测服务的48小时响应,为油气勘探开发提供强有力的技术保障。
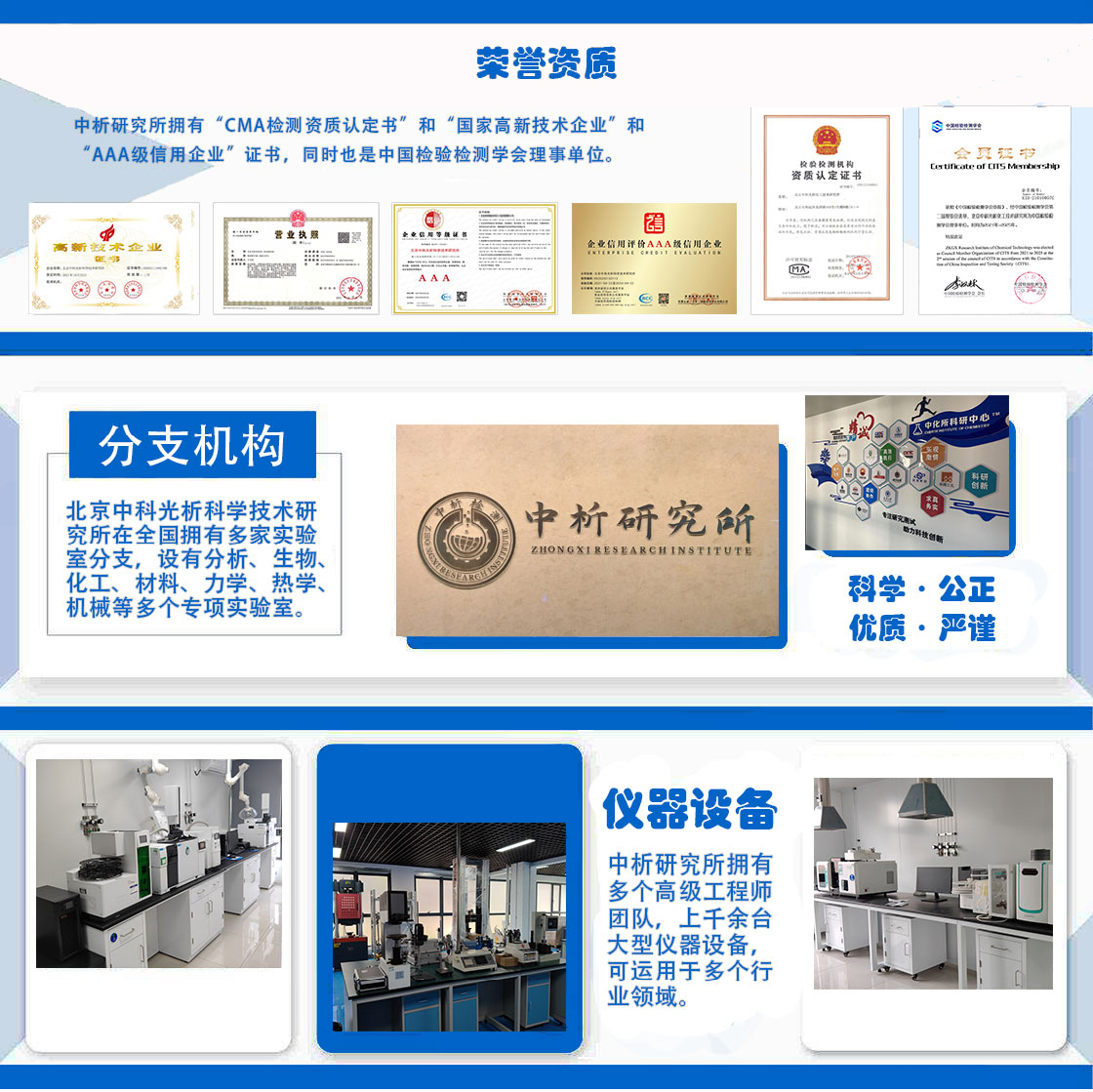
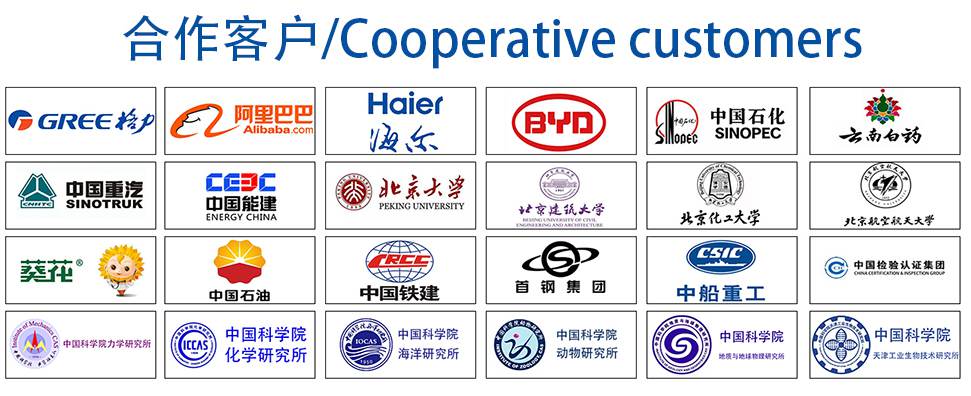