钢结构防火涂层检测项目及关键技术要点
一、钢结构防火涂层检测的核心项目
1. 涂层厚度检测
- 磁性测厚仪:适用于磁性基材(如碳钢)的湿膜或干膜厚度测量。
- 超声波测厚仪:适用于非磁性基材或复杂几何表面。
- 切片显微法(破坏性检测):通过切割涂层样本,显微镜下测量断面厚度。 标准依据:GB/T 14907《钢结构防火涂料》、CECS 24:90《钢结构防火涂料应用技术规范》。
2. 外观质量检测
- 表面均匀性、有无开裂、起泡、剥落、空鼓等缺陷。
- 颜色与设计要求的一致性(部分涂料高温后变色提示功能)。 检测工具:目视检查、放大镜辅助观察,必要时使用裂缝宽度测定仪。
3. 粘结强度测试
- 拉拔试验:使用液压或机械式拉拔仪,测定单位面积剥离力(MPa)。
- 划格法(ASTM D3359):对涂层表面划格后,通过胶带剥离观察脱落面积。 合格标准:粘结强度≥0.15 MPa(厚型涂料)或≥0.2 MPa(薄型/超薄型)。
4. 耐火性能检测
- 按GB/T 9978《建筑构件耐火试验方法》,将涂层钢结构试件置于标准火曲线(如HC曲线)下加载测试,记录耐火时间。 现场评估:
- 通过涂层厚度与耐火极限的对应关系推算(需提供涂料厂家型式检验报告)。
5. 干燥时间与固化状态
- 表干时间(触指干):手指轻触表面无粘连。
- 实干时间(完全固化):涂层完全硬化,可进行后续工序。 测试仪器:干燥时间测试仪或按GB/T 1728规定方法操作。
6. 膨胀性能测试(仅膨胀型涂料)
- 膨胀倍数:高温下涂层膨胀形成炭化层的厚度比(通常需≥5倍)。
- 炭化层致密性:通过高温炉试验观察炭化层是否连续、无开裂。 检测方法:马弗炉模拟高温环境(≥500℃),测量膨胀前后厚度。
7. 耐候性及耐久性检测
- 加速老化试验:通过QUV紫外老化箱模拟长期日照、湿热环境。
- 耐冻融循环(GB/T 1735):-20℃~50℃循环测试涂层是否开裂。
- 耐盐雾性能(GB/T 1771):评估沿海或工业区涂层的抗腐蚀能力。
8. 环保与化学性能
- VOC含量:气相色谱法测定挥发性有机物,符合GB 30981限制标准。
- 有害物质检测:铅、镉等重金属含量(GB 24408)、甲醛释放量。
- 组成成分分析:红外光谱(FTIR)验证涂料与送检样品一致性。
二、现场检测关键环节
1. 施工工艺核查
- 检查基材处理记录(喷砂除锈等级Sa2.5以上,粗糙度40~70μm)。
- 喷涂工艺参数验证(压力、喷距、层间间隔时间)。
- 随机抽查隐蔽部位(如焊缝、螺栓连接处)涂层覆盖质量。
2. 抽样原则
- 按GB 50205规定,每500㎡至少取5个测点(梁、柱、桁架均需覆盖)。
- 复杂结构或高风险区域(如逃生通道)增加抽检密度。
三、常见问题及处理对策
问题类型 | 成因分析 | 解决方案 |
---|---|---|
涂层厚度不足 | 施工偷工减料或喷涂不均 | 局部补涂至设计厚度,并重新检测 |
粘结强度不达标 | 基材预处理不合格或固化不良 | 铲除缺陷区域,重新喷砂并涂装 |
耐火性能衰退 | 材料掺假或老化失效 | 取样送实验室复核,必要时全面更换 |
膨胀层发泡不均匀 | 施工温度过低或配比错误 | 查明工艺偏差原因,返工处理 |
四、结语
上一篇:压缩机冷却水进水温度检测下一篇:排烟温度检测
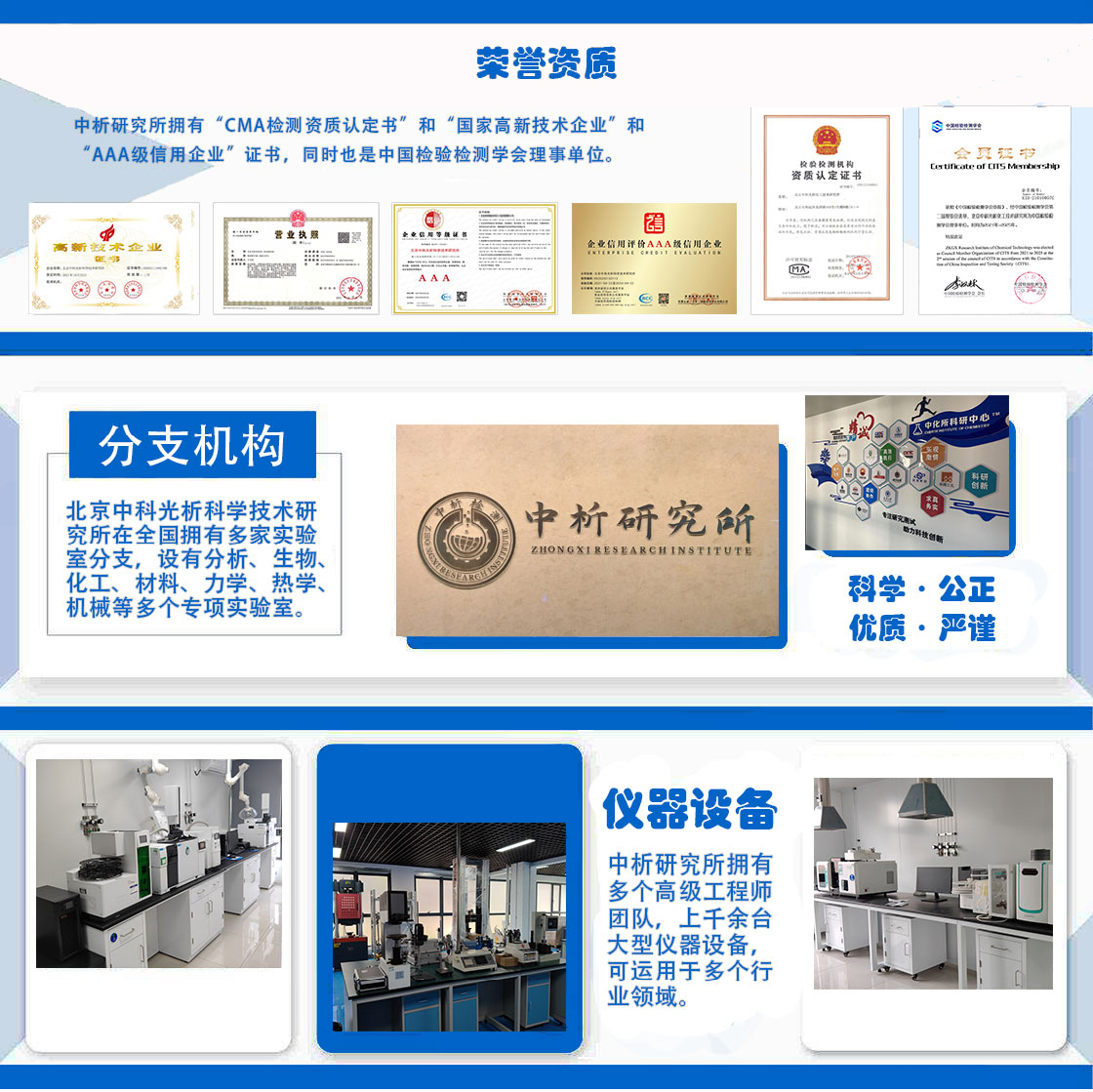
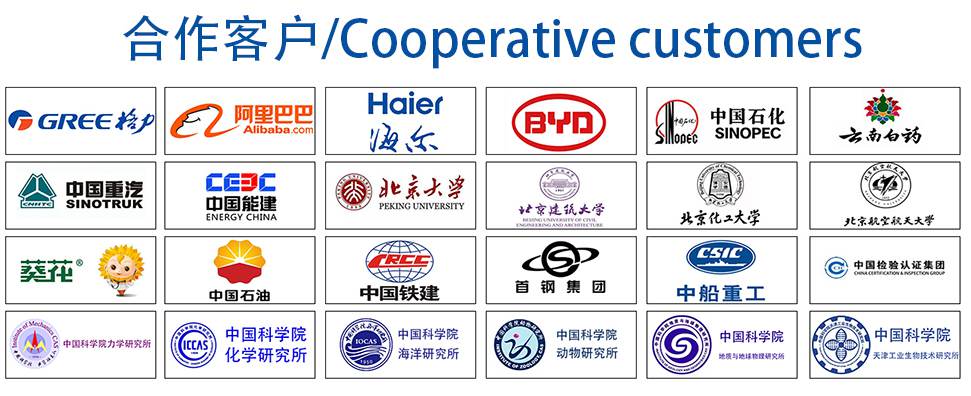
材料实验室
热门检测
22
26
24
21
48
43
50
45
47
49
41
48
42
48
40
46
38
47
42
40
推荐检测
联系电话
400-635-0567