压缩机冷却水进水温度检测:核心项目与关键技术
一、检测项目的核心内容
-
- 检测目标:持续跟踪冷却水进入压缩机前的温度值,确保其处于设计允许范围内(通常为 25~35℃)。
- 技术手段:使用高精度温度传感器(如铂电阻PT100或热电偶),配合数字显示仪表或PLC系统实时采集数据。
- 关键指标:温度波动幅度(需控制在全量程的 ±1% 以内)、响应时间(传感器延迟需小于 2秒)。
-
- 检测目标:通过进水与出水温差评估冷却系统的热交换能力。
- 测算公式: �=�⋅�⋅�⋅Δ�Q=c⋅ρ⋅V⋅ΔT 其中,�Q为散热量,�c为水的比热容,�ρ为密度,�V为流量,Δ�ΔT为进出水温差。
- 异常判定:若温差小于 3℃,可能存在换热器结垢或水流分配不均问题。
-
- 检测内容:定期(建议每季度)采用标准温度源(如恒温水浴槽)对比传感器读数,校准误差不超过 ±0.5℃。
- 干扰排查:检查电磁干扰、接线端子氧化对信号传输的影响。
-
- 附属项目:同步监测冷却塔效率、环境温湿度、冷却水流量(需匹配温度数据判断系统整体工况)。
- 典型案例:夏季高温时,冷却塔散热能力下降可能导致进水温度超限,需联动调控补水或风机转速。
二、检测流程与关键技术规范
-
- 核对压缩机额定工况参数,明确进水温度设计阈值(参考GB/T 压缩机组能效限定值标准)。
- 检查传感器安装位置是否符合 上游5倍管径、远离弯头 的流体力学规范,避免湍流干扰。
-
- 在压缩机不同负载阶段(30%、70%、100%)记录温度曲线,识别周期性波动或突变。
- 使用趋势分析软件(如MATLAB或专用SCADA系统)拟合温度变化规律,预测临界风险点。
-
- 设定多级报警阈值:
- 一级预警:温度超过设计值 85%(如32℃时触发预警);
- 二级停机保护:温度达到 38℃ 自动切断压缩机电源,防止抱缸事故。
- 集成水质检测数据(如pH值、浊度)综合判断结垢风险。
- 设定多级报警阈值:
三、典型问题及解决方案
异常现象 | 可能原因 | 处理措施 |
---|---|---|
温度读数漂移 | 传感器老化/信号干扰 | 更换传感器并加装屏蔽电缆 |
进水温度持续偏高 | 冷却塔填料堵塞或风扇故障 | 清洗填料,检查风机电机绝缘性 |
局部温度突变 | 管道气囊阻碍水流 | 在高点加装自动排气阀 |
四、优化建议与前沿技术
-
- 部署AI预测模型,通过历史数据训练预测温度趋势(如LSTM神经网络算法)。
- 采用无线物联网传感器(如LoRa模块)实现分布式监测,减少布线成本。
-
- 引入变频调速水泵,根据实时温度调节流量,降低无效功耗。
- 在低温季节采用自然冷却(Free Cooling)模式,减少冷水机组运行时间。
结语
上一篇:织物起毛起球性能检测下一篇:钢结构防火涂层检测
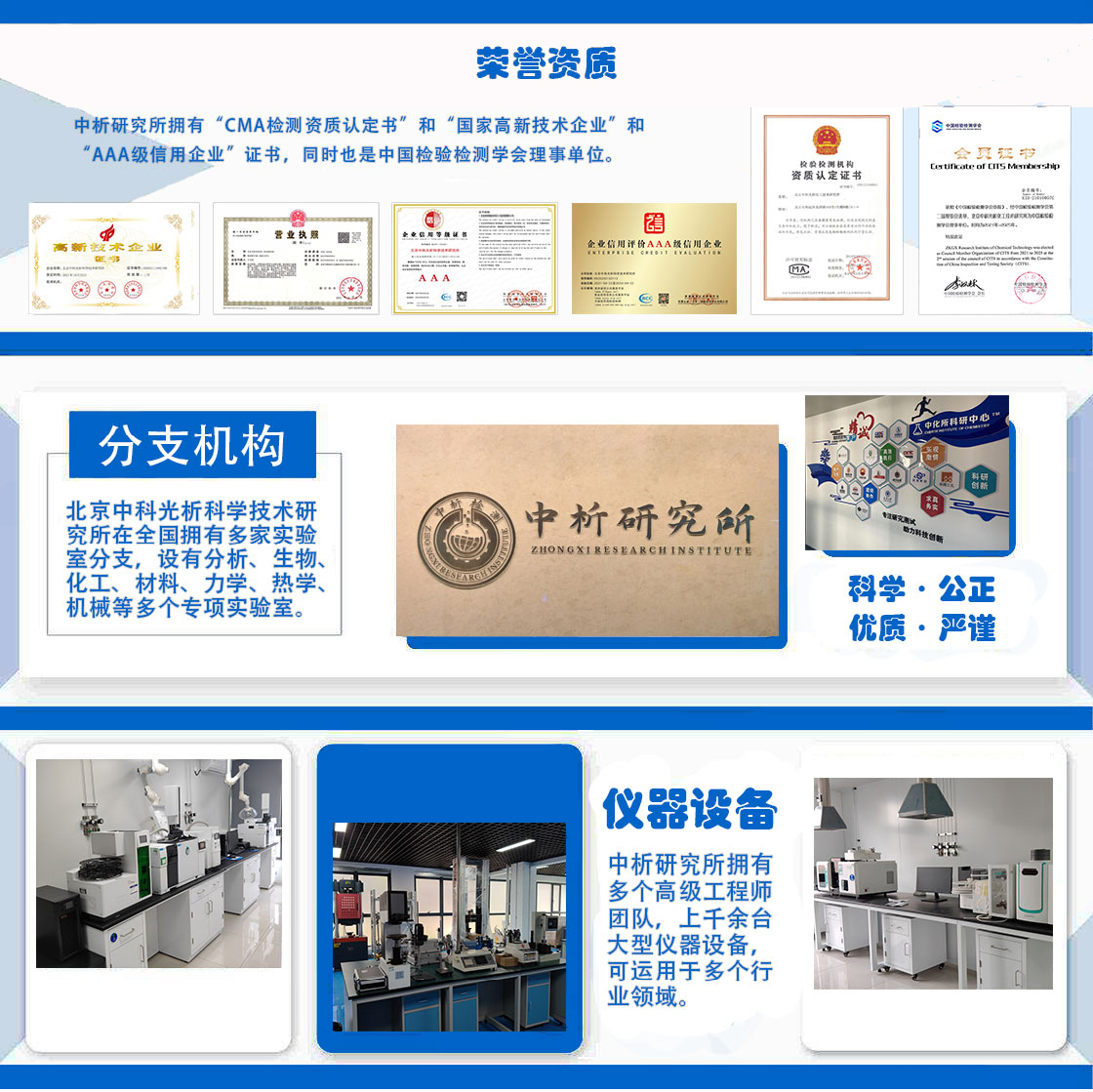
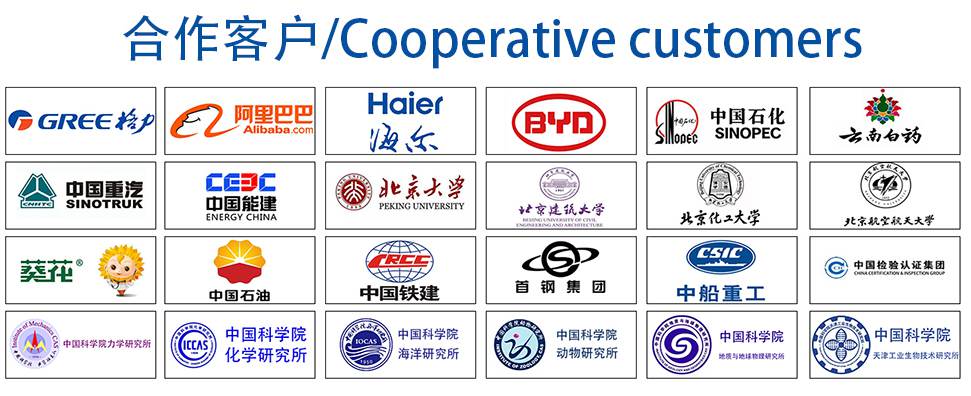
材料实验室
热门检测
280
234
209
219
217
222
231
226
234
233
221
221
224
222
215
213
228
213
228
223
推荐检测
联系电话
400-635-0567