二十辊带材冷轧机检测关键技术解析
二十辊带材冷轧机作为高端金属精密加工的核心装备,广泛用于不锈钢、硅钢、铜铝合金等薄带材的生产。其特有的多辊系结构(包含工作辊、中间辊和支撑辊)可实现0.01mm级精度的带材轧制,但复杂机械系统对设备状态检测提出了严苛要求。定期开展系统性检测不仅能保障产品尺寸精度、表面质量,还能预防设备故障,延长关键部件使用寿命。现代冷轧线检测需融合机械参数测量、电气系统诊断和智能数据分析技术,构建全方位的设备健康管理体系。
关键检测项目体系
1. 辊系精度检测
使用激光跟踪仪对20根轧辊进行三维空间定位,检测辊间平行度误差不超过0.005mm/m,同轴度偏差<0.01mm。采用纳米级表面轮廓仪测量工作辊粗糙度Ra值(通常要求≤0.1μm),同步检测辊面划痕、凹坑等微观缺陷。通过动态偏心率测试仪监控轧辊回转精度,振动幅度需控制在3μm以内。
2. 轧制力系统检测
采用分布式压力传感器矩阵测量各机架轧制力分布均匀性,压力波动范围应<±1.5%。使用液压伺服测试台校验压下油缸响应速度(≤0.02s)和位置控制精度(±0.003mm)。通过应变片法实时监测牌坊结构应力,重点检查窗口变形量是否超出0.05mm/m的许可范围。
3. 传动系统诊断
运用振动频谱分析仪检测齿轮箱运行状态,齿轮啮合频率振幅需符合ISO10816-3标准。使用红外热像仪扫描电机轴承温度,温升不应超过环境温度35℃。通过扭矩传感器监测主传动轴动态载荷,对比设计值偏差需控制在±5%以内。
4. 冷却润滑系统检测
采用粒子计数仪检测轧制油清洁度(NAS等级≤7),利用粘度计监控油品性能变化。使用高速摄像机观察喷嘴雾化效果,覆盖率需达到带材宽度的120%。通过超声波流量计校验分段冷却管路流量均衡性,各支路流量偏差应<3%。
5. 电气控制系统测试
运用PLC信号发生装置模拟128个I/O点信号,检测系统响应正确率需达100%。通过激光多普勒测速仪验证AGC(自动厚度控制)系统的动态调节精度,厚度波动应≤±0.5μm。使用绝缘电阻测试仪测量高压柜绝缘电阻值(≥100MΩ),接地电阻须<0.1Ω。
6. 安全防护装置验证
测试紧急停止系统响应时间<0.5s,防护罩联锁装置触发成功率需达100%。采用激光对射传感器检测人体进入危险区域时的停机距离(≥500mm)。通过载荷模拟装置校验过载保护装置的触发阈值精度(±1%FS)。
7. 材料性能检测
配置在线测厚仪(精度±0.1μm)和表面检测系统(分辨率5μm),实时监控带材厚度公差与表面缺陷。使用残余应力分析仪测定轧后材料应力分布均匀性,通过杯突试验机评估材料成形性能(极限拉深比≥2.0)。
8. 智能化检测升级
部署工业物联网传感器网络,实现振动、温度、压力等300+参数的在线采集。应用机器学习算法构建设备健康预测模型,关键部件剩余寿命预测误差<10%。通过数字孪生技术建立三维仿真系统,支持轧制过程虚拟调试与异常工况模拟。
现代二十辊冷轧机检测已形成涵盖机械、电气、工艺的全维度体系,企业需建立包含日常点检(每班)、预防性检测(每月)和大修检测(年度)的三级制度。通过检测数据与生产工艺的深度耦合,可实现设备OEE(综合效率)提升15%以上,同时降低30%的意外停机损失。
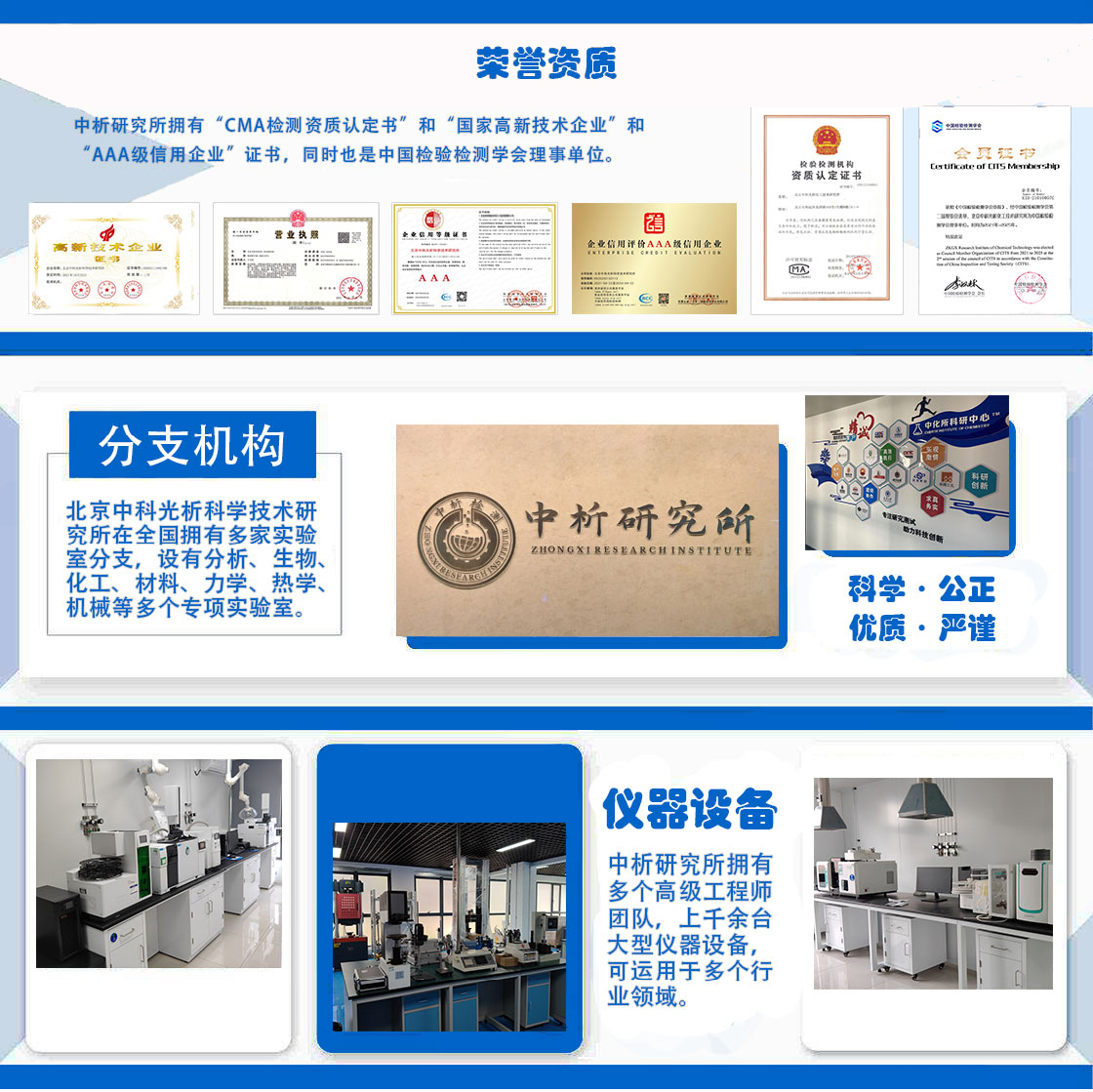
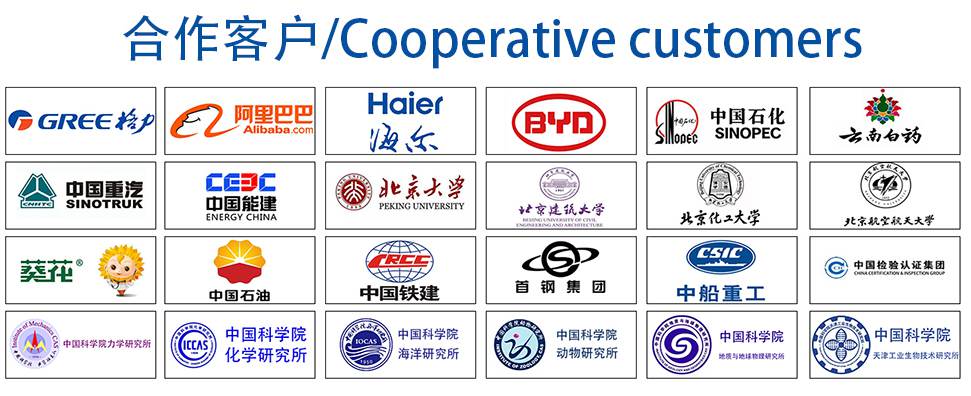