小型卧式滚齿机参数检测的重要性
小型卧式滚齿机作为齿轮加工领域的核心设备,其性能参数直接决定了齿轮的加工精度、效率及设备寿命。随着制造业对精密齿轮需求的不断提升,参数检测成为确保设备稳定性和加工质量的关键环节。通过系统的参数检测,可及时发现设备运行中的偏差、磨损或装配误差,避免因设备故障导致的批量报废风险。同时,定期检测还能延长设备使用寿命,降低维护成本,为企业的生产效率和竞争力提供保障。
核心检测项目与技术要求
1. 主轴系统精度检测
主轴是滚齿机的动力核心,需检测其径向跳动(≤0.005mm)、轴向窜动(≤0.003mm)及回转精度(符合GB/T 17421.2标准)。使用高精度千分表配合标准芯轴进行动态测试,确保主轴在额定转速下的稳定性。
2. 分度蜗轮副传动精度
分度蜗轮副的传动误差直接影响齿轮分度精度。需通过啮合间隙检测(要求≤0.03mm)和累积误差测量(≤±15"),结合激光干涉仪进行动态补偿分析,确保分度精度达到ISO 1328-1的5级精度标准。
3. 滚刀轴定位与安装精度
检测滚刀轴与工件轴的中心距误差(≤0.02mm)、轴线平行度(≤0.01mm/100mm)及滚刀安装端面的跳动量(≤0.008mm)。需采用专用检具配合三坐标测量仪进行多维度校准。
4. 切削系统动态性能测试
包括切削力波动监测(≤±10%额定值)、主轴温升(≤25℃/4h连续工作)及振动幅度(≤4μm@3000rpm)。通过安装振动传感器和红外测温仪,模拟实际加工负载进行动态数据采集。
5. 数控系统响应与误差补偿
针对数控型设备,需检测伺服电机位置跟踪误差(≤±1脉冲)、插补精度(≤0.005mm)及反向间隙补偿效果(残余间隙≤0.003mm)。通过编写特定G代码进行闭环测试,验证系统补偿算法的有效性。
检测流程标准化建议
建议采用“静态检测→空载运行→负荷测试→复检校准”的四步流程,结合设备说明书参数与行业标准(如JB/T 6343.1-2015)进行对比分析。对于关键参数应建立检测台账,通过趋势分析预判潜在故障。同时推荐使用具备数据存储功能的智能检测仪器(如无线扭矩仪、数字式激光校准仪),实现检测数据的可追溯性与深度分析。
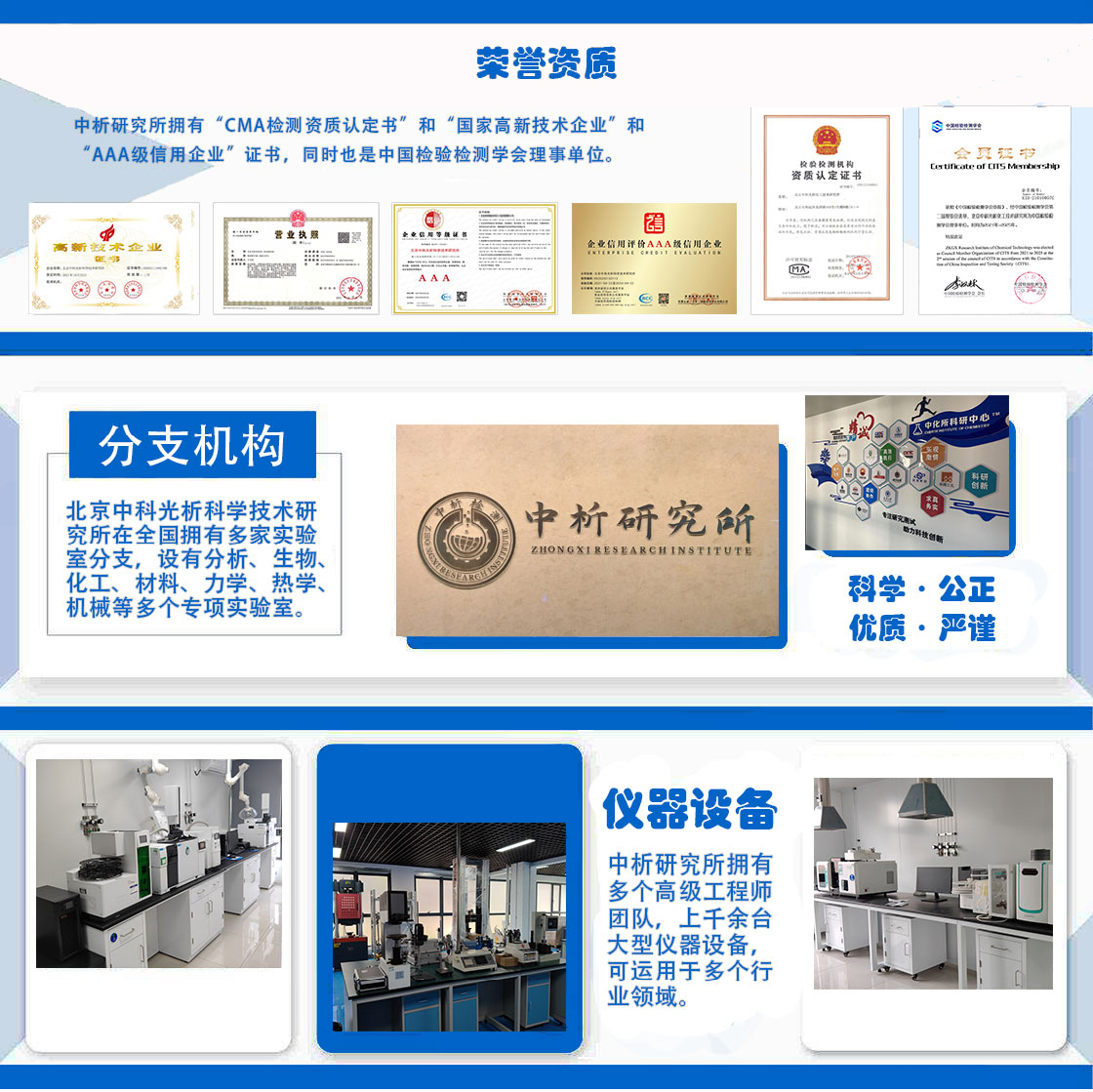
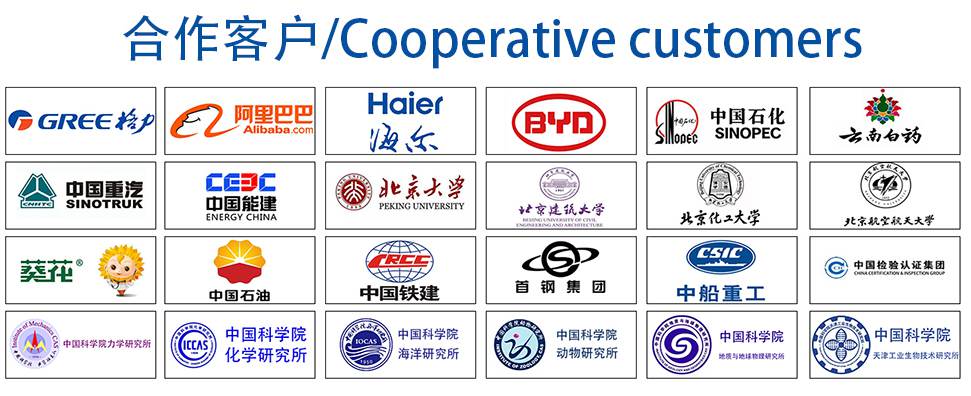