坐标镗床转台检测的重要性
坐标镗床作为高精度加工设备的核心组成部分,其转台的性能直接影响工件的定位精度和加工质量。转台长期承受切削力、重复定位载荷及环境因素影响,可能产生几何误差、传动系统磨损或电气系统漂移等问题。通过系统性检测,可及时发现转台的分度精度误差、回转刚性不足、定位重复性异常等隐患,避免因设备精度衰减导致的批量工件报废,同时为设备维修和精度补偿提供科学依据。
核心检测项目及方法
几何精度检测
使用电子水平仪和激光干涉仪检测转台工作面的平面度(误差应≤0.005mm/1000mm),通过直角尺配合千分表测量转台轴线与镗轴轴线的垂直度(允差0.008mm)。对于环形转台,需采用球杆仪进行圆周轨迹精度检测,分析径向和轴向跳动量。
分度定位精度检测
采用多齿分度台或高精度角度编码器进行全闭环检测,评估转台在0°-360°范围内的定位误差。要求单点定位误差≤±3",重复定位误差≤±1.5"。对于数控转台,需同步检测伺服系统的跟随误差和反向间隙补偿效果。
回转传动系统检测
通过扭矩传感器测量蜗轮蜗杆副的传动效率(应≥85%),使用振动分析仪检测齿轮啮合频率下的异常振动(振幅应≤4μm)。重点检查转台锁紧时的微动位移量,采用应变片法测试锁紧力分布均匀性,确保夹紧状态下的刚性满足切削要求。
智能化检测技术应用
现代检测已引入激光跟踪仪和数字孪生技术,通过建立转台三维误差模型,实现温度补偿、动态误差预测等功能。采用无线传感器网络实时监测转台运行状态,结合大数据分析提前预警潜在故障。对于精密级转台(ISO标准P3级),建议每500小时或加工关键部件前执行全项检测。
检测结果分析与处理
检测数据需参照GB/T 17421.2-2016标准进行评估,对超差项目进行溯源分析:机械磨损需调整预紧力或更换轴承;电气系统误差应重新校正光栅尺零位;热变形问题则需优化冷却系统。通过激光干涉仪生成的误差补偿表导入数控系统,可使转台定位精度恢复至出厂标准的95%以上。
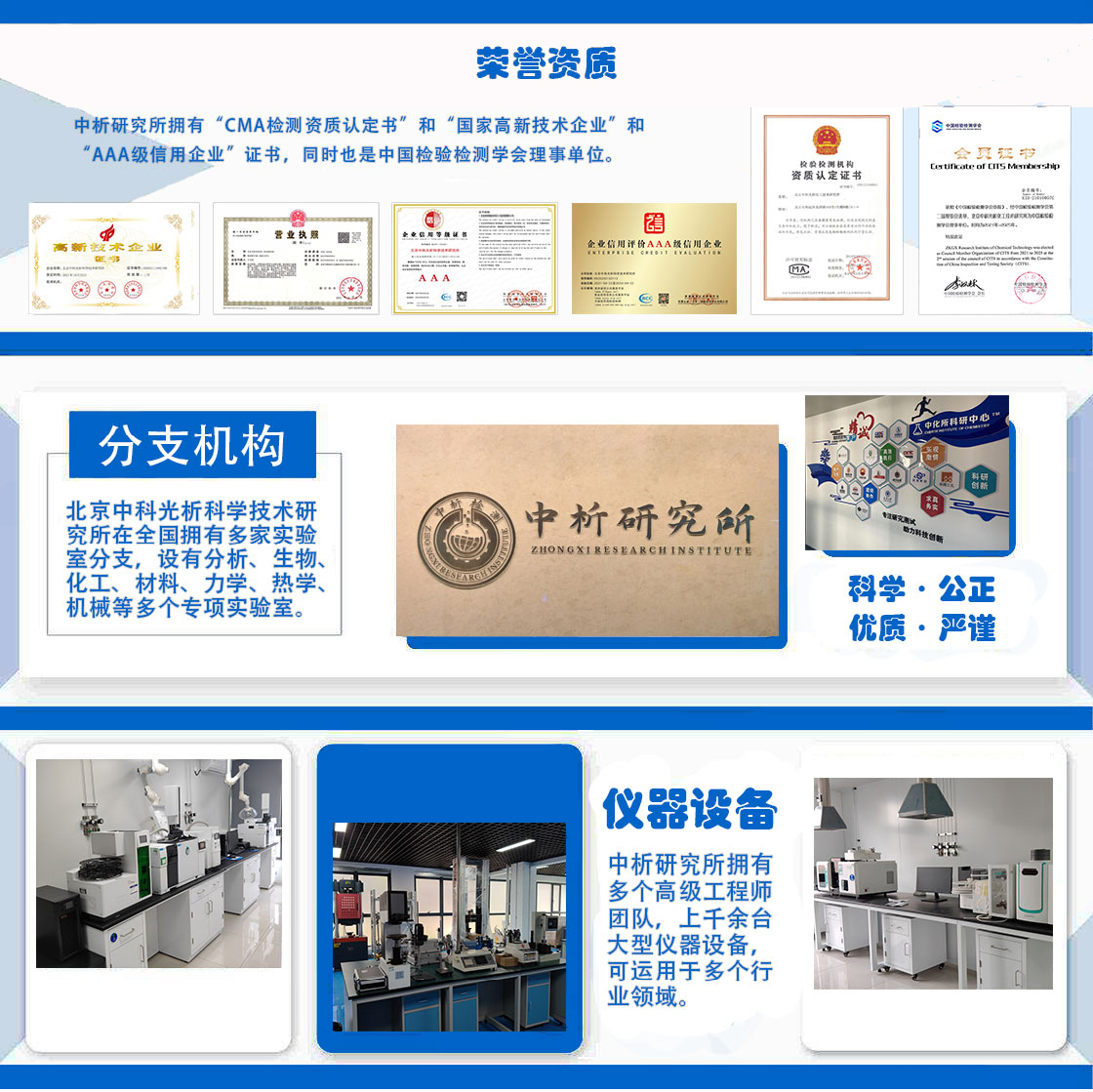
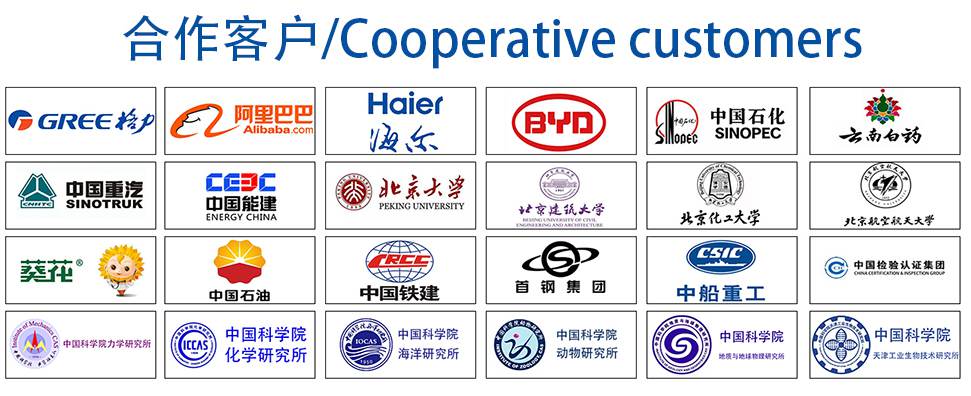