油气分离器检测的核心价值与技术要点解析
油气分离器作为压缩空气系统、发动机润滑系统和工业设备中的关键部件,承担着高效分离油气混合物、确保系统稳定运行的重要职责。其性能直接影响设备能耗、油品消耗量及排放指标,因此定期开展专业检测已成为设备维护中的必要环节。据行业统计,80%以上的压缩机故障均与油气分离器效能下降存在直接关联,科学的检测流程可延长设备寿命30%以上。
核心检测项目体系
1. 结构完整性检测
通过三维扫描和壁厚测量仪对分离器壳体、焊缝进行0.1mm级精度检测,配合20MPa耐压试验验证承压能力。重点排查壳体变形、裂纹及内部滤芯支架结构完整性,确保在脉冲压力下无结构性失效风险。
2. 分离效率测试
采用激光粒子计数器进行动态检测,在额定工况下测量出口气体含油量。符合ISO 8573-1标准的0级分离器要求残余油雾≤0.01mg/m³,同时使用称重法测定油液回收率,优秀产品应达到99.9%以上的分离效率。
3. 材料耐受性分析
对滤材进行150℃高温老化试验和耐腐蚀测试,使用光谱仪检测金属部件材质成分。重点验证不锈钢部件在CL⁻离子环境中的抗点蚀能力,橡胶密封件需通过2000小时耐油膨胀试验,确保材料性能符合工况要求。
4. 压降特性监测
运用高精度压差传感器测量新旧状态下的气流压损,标准规定初始压降不得超过0.15bar,使用过程中压升达到0.5bar时必须更换。建立压降-时间曲线可预判滤芯堵塞趋势,实现预测性维护。
5. 密封性能验证
采用氦质谱检漏仪进行10⁻⁶Pa·m³/s级灵敏度检测,对法兰接口、观察窗等关键部位进行气密性测试。同时进行50万次脉冲压力循环试验,验证密封系统在交变载荷下的可靠性。
进阶检测维度
6. 油品污染度检测
使用颗粒计数器分析分离后润滑油NAS等级,配合铁谱仪检测异常磨损金属颗粒。优质分离器应能将油液清洁度维持在NAS 6级以内,避免因微小颗粒引发的二次磨损。
7. 振动噪声评估
通过加速度传感器测量壳体振动烈度,使用声级计在1米距离进行噪音检测。符合GB/T 7777标准的设备运行噪音应≤75dB(A),异常振动往往预示内部流场紊乱或结构松动。
8. 智能监测集成
新型检测方案集成压力、温度、差压传感器,通过工业物联网实时传输运行数据。结合AI算法可提前30天预警分离器失效,实现检测模式从定期维护向状态监测的转型升级。
系统的检测体系不仅需要覆盖传统性能指标,更要结合智能运维发展趋势。通过建立多维检测数据库,企业可精准制定更换周期,将设备非计划停机率降低60%以上,真正实现降本增效的运维目标。
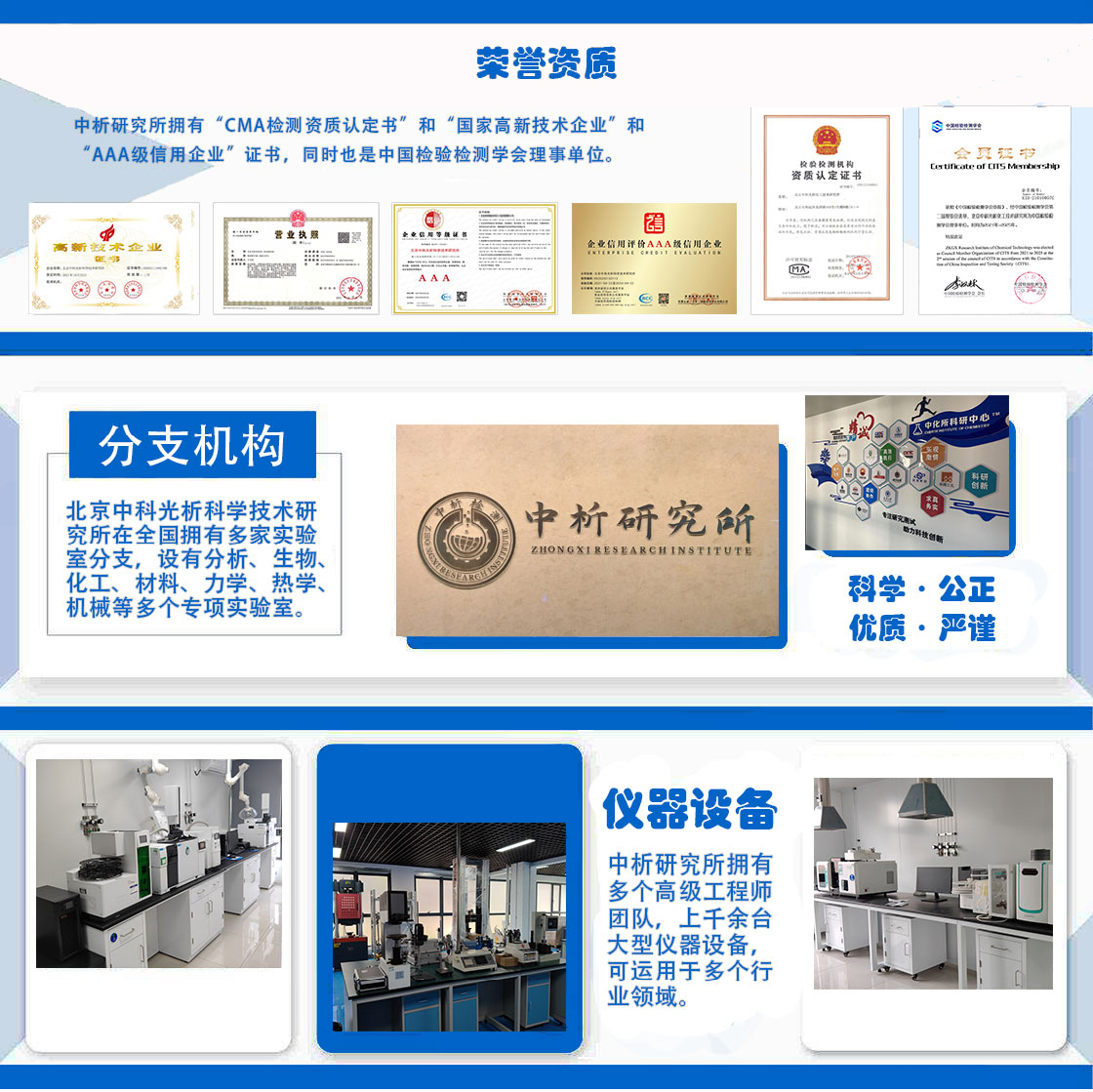
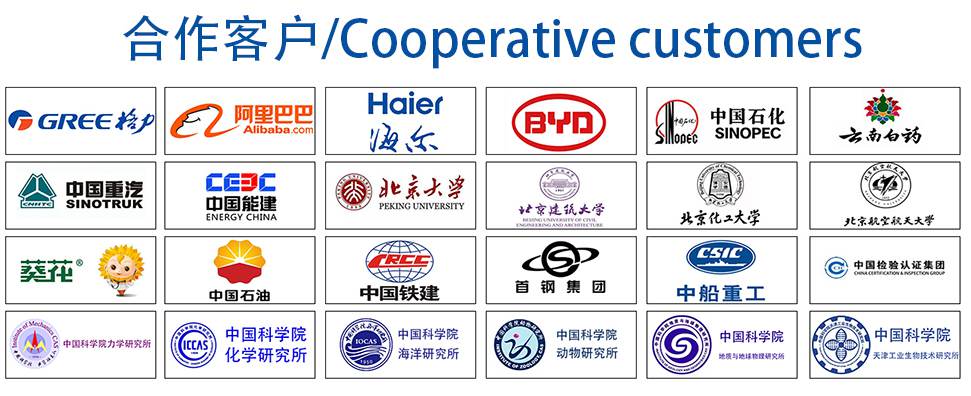