低温压力容器用钢板检测的重要性与关键项目
低温压力容器是广泛应用于液化天然气(LNG)、液氮储罐、化工设备等领域的特种设备,其工作环境通常需承受-20℃以下的低温及高压载荷。由于低温环境下材料的韧性会显著降低,一旦钢板存在缺陷或性能不达标,极易引发脆性断裂等安全事故。因此,低温压力容器用钢板的检测是确保设备安全运行的核心环节,需通过多项关键检测项目验证其化学成分、力学性能和微观结构是否符合国家标准(如GB 3531)及行业规范。
核心检测项目及技术要求
1. 化学成分分析
钢板的化学成分直接影响其低温性能。需通过光谱分析法、电感耦合等离子体发射光谱(ICP-OES)等检测碳(C)、锰(Mn)、镍(Ni)、磷(P)、硫(S)等元素含量。例如,镍元素可显著提升钢的低温韧性,但过量会增加成本,需精准控制。
2. 力学性能测试
包括拉伸试验、弯曲试验和硬度试验: - 拉伸试验:测定屈服强度(Rp0.2)、抗拉强度(Rm)及断后伸长率(A),确保材料在低温下具备足够抗变形能力; - 低温冲击试验(Charpy V型缺口):在-40℃至-196℃环境下测试冲击吸收能量(KV2),验证材料抗脆断能力; - 弯曲试验:评估钢板在低温下的塑性变形能力,通常要求180°弯曲后无裂纹。
3. 无损检测
采用超声波检测(UT)、射线检测(RT)及磁粉检测(MT)等技术,检测钢板内部及表面的缺陷: - 超声波检测:发现分层、夹渣等内部缺陷; - 射线检测:识别气孔、未熔合等体积型缺陷; - 磁粉检测:排查表面及近表面裂纹。
4. 金相组织分析
通过显微镜观察钢板的显微组织(如铁素体、贝氏体比例)及晶粒度,确保晶粒细化(通常要求≥8级),以提升低温韧性。需重点关注夹杂物(如硫化物、氧化物)的形态与分布,避免局部应力集中。
5. 低温时效敏感性试验
模拟材料长期处于低温环境下的性能变化,通过对比时效前后的冲击试验数据,评估韧性劣化程度,确保钢板在服役周期内稳定性。
检测标准与质量控制
检测依据需严格遵循GB/T 713-2014《锅炉和压力容器用钢板》、GB/T 229-2020《金属材料夏比摆锤冲击试验方法》等标准。生产企业及第三方检测机构需建立完整的质量追溯体系,确保每批次钢板的检测数据可追溯,并留存试样以备复检。
结语
低温压力容器用钢板的检测是保障设备本质安全的关键步骤,需通过多维度、高精度的检测手段全面评估材料性能。只有严格把控化学成分、力学性能、无损缺陷及微观组织等核心指标,才能有效避免低温环境下的失效风险,为压力容器的全生命周期安全运行提供技术支撑。
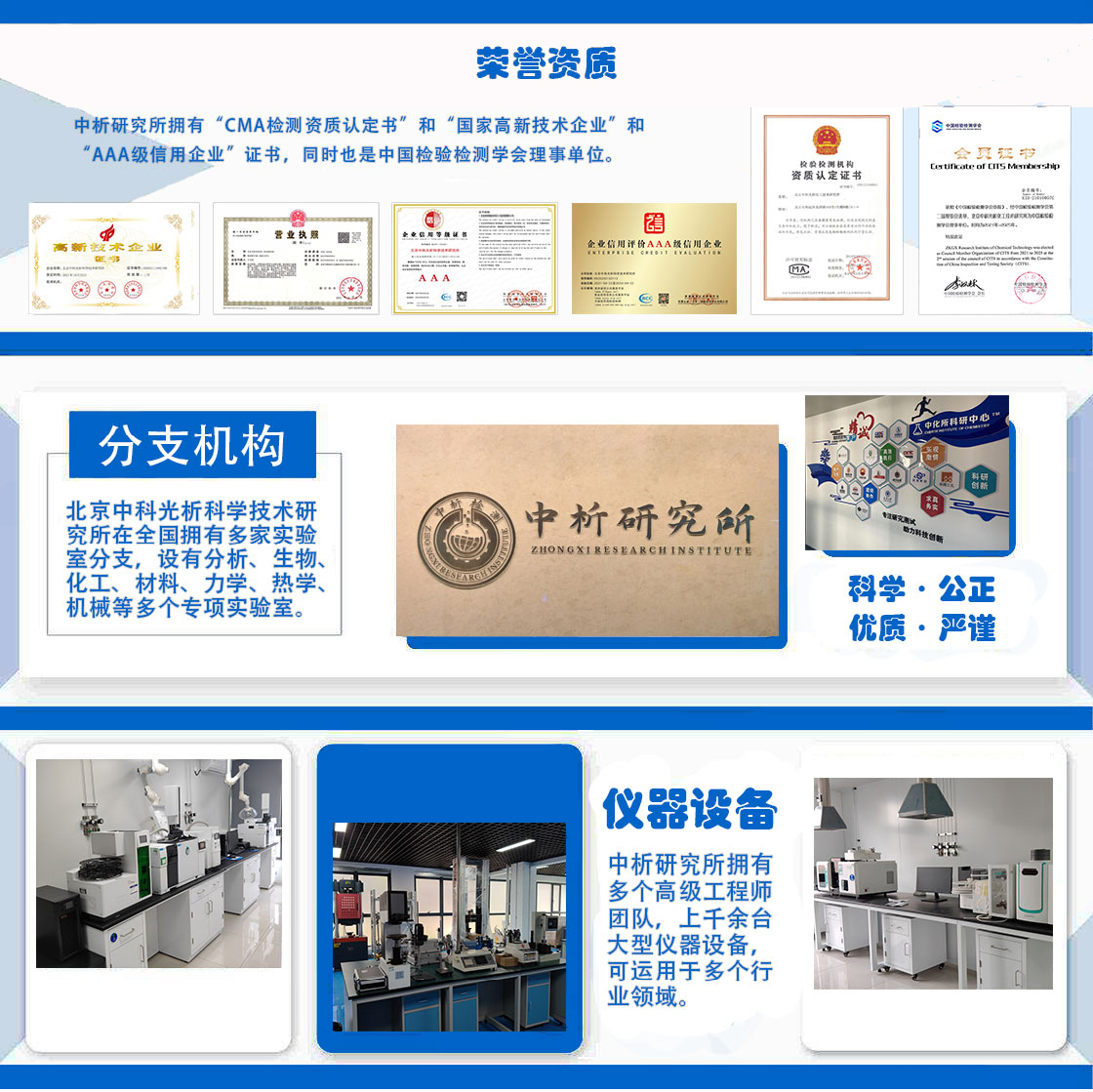
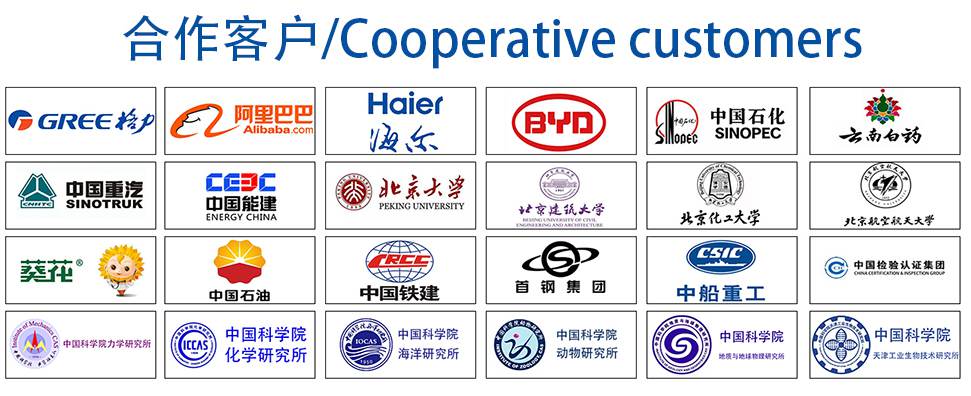