石油钻机和修井机井架、底座检测的重要性与内容
在石油钻探与修井作业中,井架和底座作为支撑系统的核心部件,承担着悬挂钻具、承受动态载荷、保障作业安全的关键作用。由于长期暴露在恶劣工况(如高载荷、腐蚀性环境、频繁震动等)下,其结构完整性和稳定性直接影响人员安全与设备运行效率。因此,定期开展石油钻机和修井机井架、底座的专业检测,是石油行业安全生产规范中的强制性要求,也是预防重大事故的核心措施。
主要检测项目及技术手段
1. 结构完整性检测:通过超声波探伤(UT)、磁粉检测(MT)等技术,排查井架立柱、横梁、连接销轴等部位的裂纹、腐蚀及焊接缺陷。针对底座支撑板、基座螺栓等重点区域,采用渗透检测(PT)确认表面微裂纹。
2. 几何尺寸测量:使用全站仪、激光测距仪等设备,测量井架垂直度、底座水平度及关键节点间距,确保符合API Spec 4F或SY/T 5609等行业标准允许的偏差范围。
3. 载荷性能测试:通过静载试验验证最大承载能力,动态载荷监测系统实时记录作业时的应力分布,分析是否存在局部过载风险。
4. 腐蚀与疲劳评估:结合材料厚度检测(UT测厚)与金相分析,评估金属部件的剩余寿命,对盐雾腐蚀、硫化氢侵蚀等特殊环境进行专项检查。
检测标准与合规性要求
检测需依据《石油天然气钻井井架分级评定规范》(SY/T 6326)、API RP 4G(井架和底座维护)等标准执行。第三方检测机构须具备CMA/ 资质,检测报告须包含缺陷定位图谱、安全等级评定及维修建议,并纳入设备管理档案。
常见问题与处理措施
典型问题包括井架立柱变形(需矫正或更换)、底座基础沉降(需灌浆加固)、连接件磨损(需补焊或升级材质)。对于达到报废标准的构件(如裂纹深度超过壁厚20%),必须强制停用并更换。2021年某油田事故调查显示,未及时修复的底座螺栓疲劳断裂导致井架倾覆,凸显定期检测的必要性。
智能化检测技术发展
当前行业正推进无人机巡检、三维激光扫描建模、物联网应力监测等技术的应用。例如,通过无人机搭载高清摄像头与热成像仪,可快速完成高空节点检测;基于AI的裂纹识别算法能将分析效率提升40%以上,显著降低人工漏检风险。
检测流程管理建议
企业应建立年度检测计划,结合设备使用频次调整周期(如高寒地区每6个月检测一次)。建议采用PDCA循环模式:检测(Plan)-分析缺陷(Do)-维修验证(Check)-优化标准(Act),并依托数字化平台实现检测数据全生命周期管理。
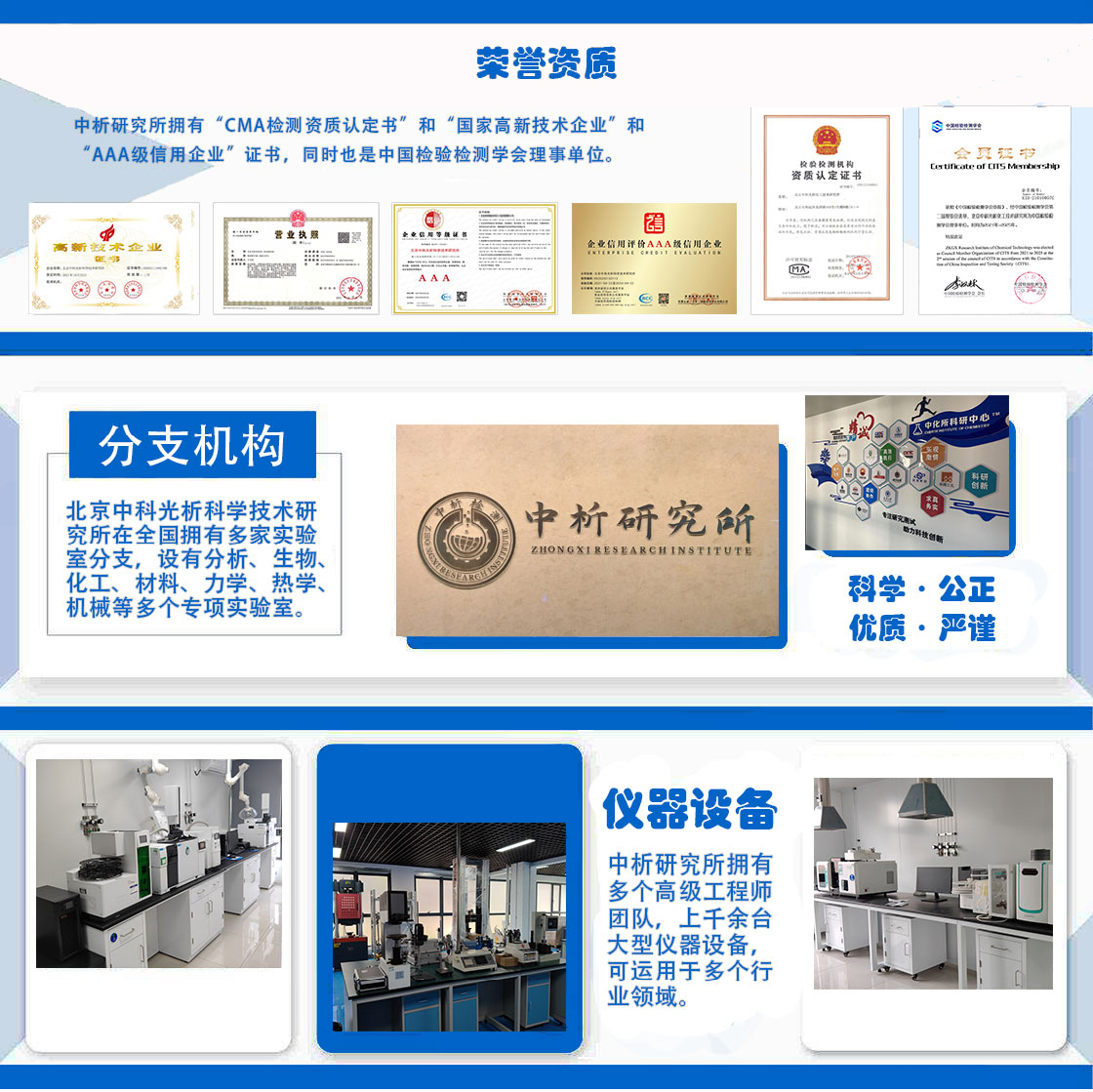
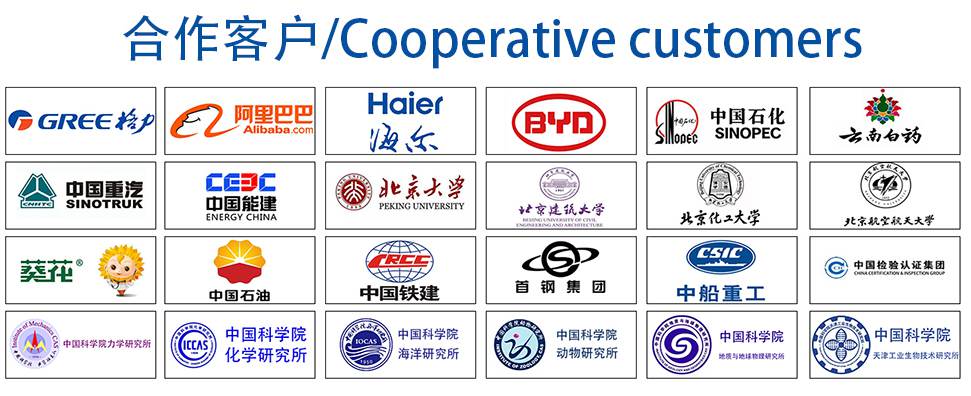