旋转电机绝缘结构功能性评定的核心意义
在电力驱动系统、工业设备及新能源领域中,旋转电机的可靠性直接影响设备整体寿命与运行安全性。作为电机核心组件的绝缘结构,其功能性评定贯穿于设计验证、制造工艺优化及故障预防全流程。成型绕组试验规程与绝缘结构热机械耐久性评定检测,是评估绝缘系统在复杂工况下抗老化能力、机械稳定性及电气性能的关键体系。通过系统化检测项目,可精准量化绝缘材料在热-机械-电气多应力耦合作用下的失效阈值,为电机全生命周期管理提供数据支撑。
成型绕组试验规程的核心检测项目
基于IEC 60034-18-21、GB/T 17948.1等国际国内标准,成型绕组试验规程包含:
1. 绝缘电阻测试:采用1000V兆欧表测量绕组对地及相间绝缘电阻,评估材料初始绝缘性能,要求常态下≥100MΩ(20℃/RH≤65%)
2. 介质损耗角(tanδ)测试:通过0.2Un~1.5Un阶梯升压测量介质损耗变化率,监控绝缘材料极化特性与局部缺陷
3. 局部放电(PD)检测:在1.7倍额定电压下,采用高频电流传感器(HFCT)检测放电量,要求≤10pC(I类绝缘结构)
4. 工频耐压试验:施加2Un+1000V/1min验证绝缘结构瞬时击穿强度,重点监测电晕起始电压(CIV)
5. 热循环试验:模拟-40℃~180℃温度交变(循环次数≥200),通过显微CT检测分层、裂纹等机械损伤
绝缘结构热机械耐久性评定要点
针对电机启停、过载等工况,热机械耐久性检测聚焦:
1. 温度梯度模拟:建立绕组热点温度模型,采用红外热像仪验证实际温升分布,要求与设计值偏差≤5℃
2. 机械应力模拟:通过电磁振动台施加0.5-200Hz随机振动,检测绑扎带张力衰减率及槽楔位移量
3. 绝缘材料老化分析:执行加速热老化试验(180℃/500h),对比老化前后击穿电压(≥85%初始值)和抗弯强度(≥70%初始值)
4. 热机械循环试验:结合温度循环(ΔT=150K)与机械负载循环(0-120%额定转矩),评估云母带与铜导体的界面剥离强度
综合检测方案的实施要求
为确保评定结果的有效性,需满足:
1. 多物理场耦合测试:同步采集温度-振动-局部放电参数,建立三维有限元模型进行应力集中区预测
2. 环境适应性验证:在湿度95%RH、盐雾腐蚀等恶劣环境下,检测表面爬电距离与漏电起痕指数(CTI≥175V)
3. 数据融合分析:采用Weibull分布处理寿命试验数据,计算特征寿命L10与斜率参数β,确定B/F/H级绝缘的加速因子
4. 失效模式库构建:通过SEM/EDS分析典型失效样本,建立绝缘分层、碳化通道、介质击穿等故障特征图谱
该检测体系已成功应用于新能源发电机、牵引电机等场景,将绝缘结构平均寿命预测误差控制在±15%以内,显著提升电机可靠性设计水平。
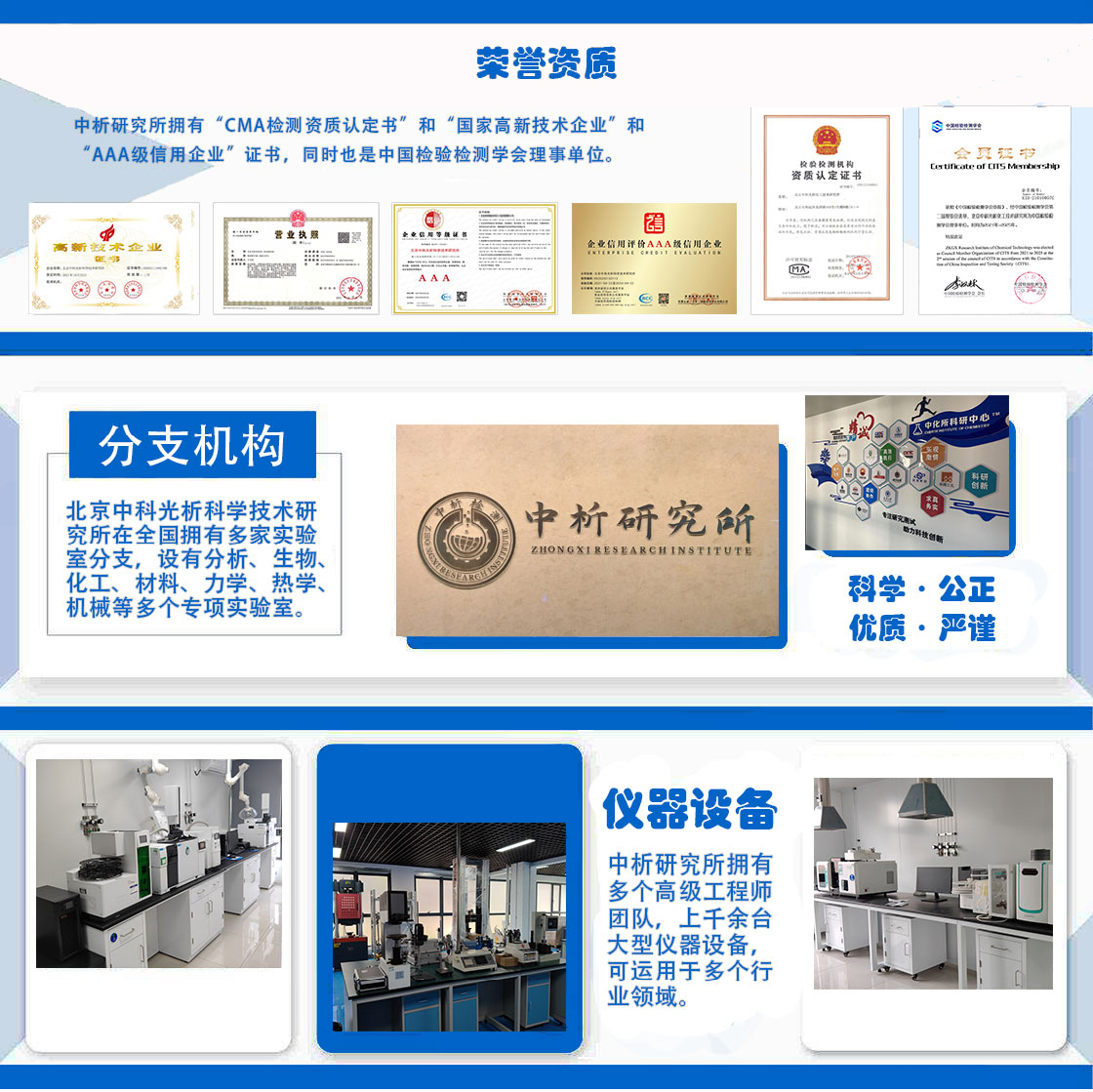
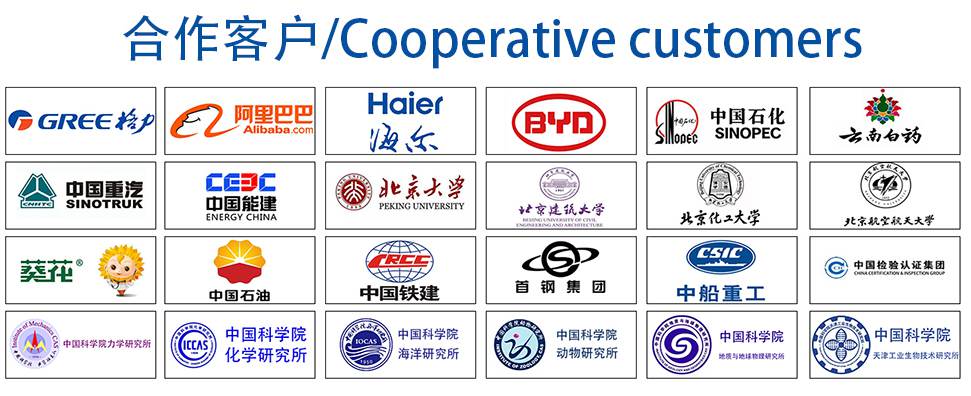