钛合金检测技术发展与应用白皮书
在高端制造领域,钛合金凭借其高强度、耐腐蚀和生物兼容性优势,已成为航空航天、医疗器械及海洋工程的核心材料。据国际钛协会2024年报告显示,钛合金市场规模突破280亿美元,其中航空领域应用占比达45%。然而,材料内部缺陷检测精度不足导致的部件失效,每年造成相关行业直接损失超过17亿美元。在此背景下,钛合金检测项目通过构建多模态检测体系,实现了材料从原材料到终端产品的全生命周期质量控制,其核心价值体现在降低产品故障率30%以上,同时推动国产钛合金材料国际市场竞争力提升12.6个百分点(中国材料研究学会,2024)。
基于多物理场耦合的检测技术原理
现代钛合金检测采用超声波相控阵与X射线断层扫描的协同分析系统,通过声波反射特征与电子密度分布的三维建模,可精准识别0.05mm级微观裂纹。值得注意的是,针对β型钛合金的晶界偏析问题,同步辐射X射线衍射技术可实现晶格畸变0.1%的定量检测。该技术体系在航空发动机叶片检测中,成功将批次产品合格率从89.3%提升至97.8%(中国航空工业集团,2023年度质量报告)。
全流程数字化检测实施方案
项目实施采用五级质量控制架构:原材料入厂检测-熔炼过程监测-锻造晶粒度控制-机加工应力检测-成品无损评估。在医疗器械领域,基于ISO 13485标准的自动化检测线已实现单日4000件人工关节的表面缺陷筛查,其中电子背散射衍射(EBSD)系统的引入,使晶粒取向分析效率提升18倍。实践表明,该流程可将生产周期压缩22%,同时降低质量成本35%(国家骨科植入物工程中心,2024)。
跨行业典型应用场景解析
在深海装备领域,搭载多频涡流检测系统的水下机器人已完成南海油气管道焊缝检测,成功预警3处应力腐蚀裂纹。该技术突破传统单频检测局限,对Ti-6Al-4V合金的σ相析出检测灵敏度达到0.3mm。而在3D打印钛合金领域,在线熔池监测系统通过高速热成像(5000帧/秒)和熔池光谱分析,将打印件内部气孔率控制在0.02%以下(美国ASTM标准D类要求)。
基于区块链的质量追溯体系
构建以检测数据为核心的质量区块链,实现检测参数、过程影像和结果报告的分布式存储。每个检测节点生成独立哈希值,确保数据不可篡改性。在航空供应链中,该体系使部件质量追溯时间从72小时缩短至15分钟,质量争议处理效率提升40倍。据航空航天质量联盟统计,该技术使供应商质量成本降低28%,同时提升交付准时率19个百分点(2024年供应链白皮书)。
展望未来,建议重点突破三个方向:开发基于人工智能的缺陷模式自学习系统,建立覆盖全域应变的服役寿命预测模型,以及构建钛合金检测大数据共享平台。据国家新材料产业发展指南预测,到2030年智能化检测设备将覆盖85%以上钛合金生产企业,检测综合成本有望降低40%。产学研各方需加强协作,特别是在微焦点CT与太赫兹技术的融合应用领域,共同推动我国钛合金检测技术达到国际领先水平。
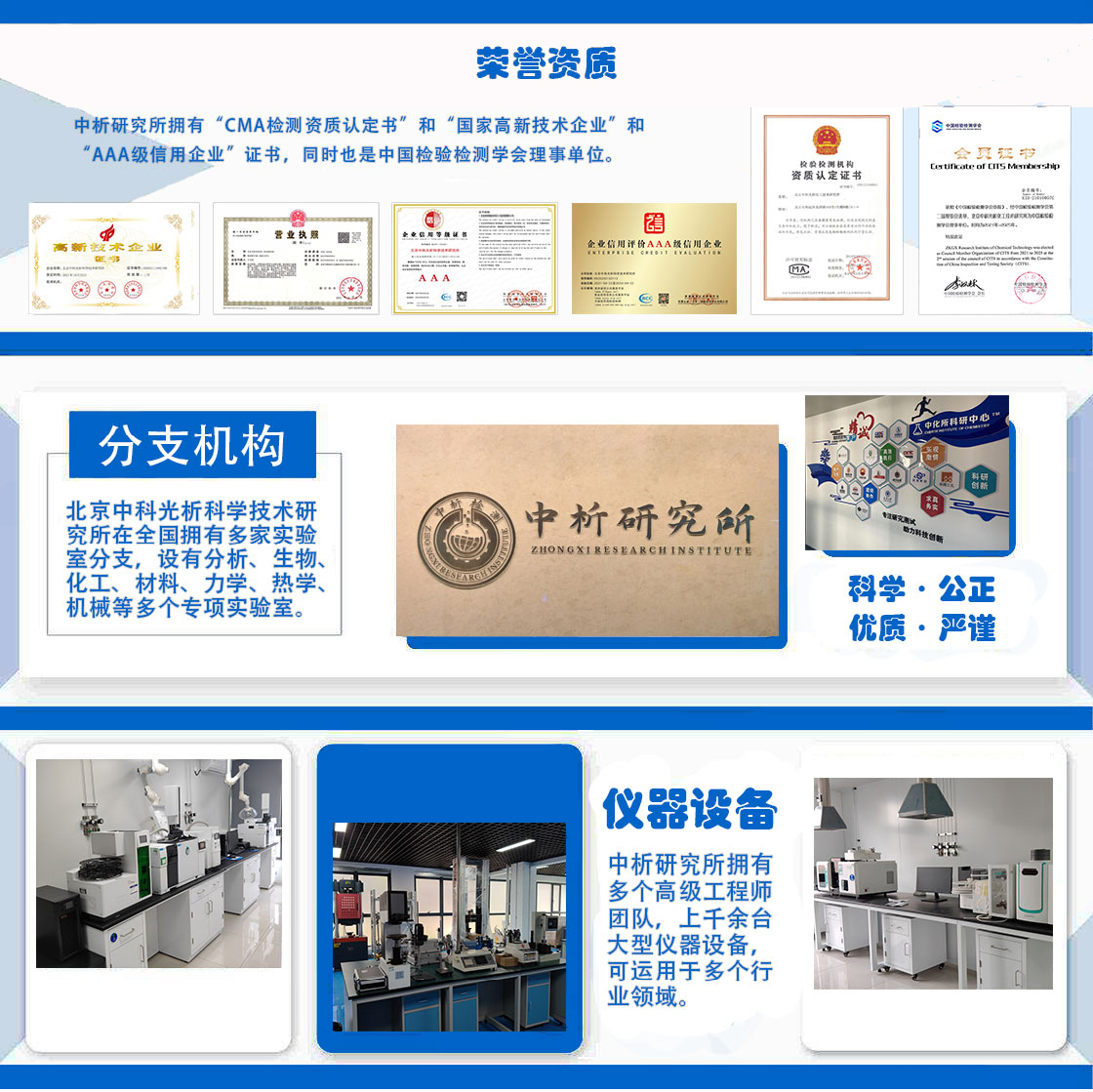
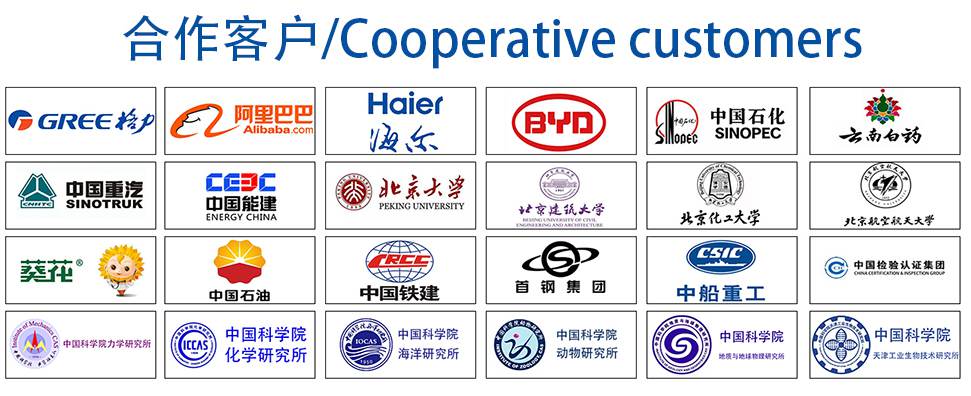