结至环境热阻/结至壳热阻检测技术白皮书
随着电子器件功率密度持续提升,热管理已成为制约高可靠性设备开发的关键瓶颈。据赛迪研究院2024年数据显示,功率半导体市场年复合增长率达12.5%,而因散热不良导致的器件失效占比高达37%。结至环境热阻(Rja)与结至壳热阻(Rjc)作为表征器件热传导效率的核心参数,其精准检测直接关系到热设计优化、寿命预测及故障预警。本项目通过构建多物理场耦合检测体系,可实现±2%的测量精度,帮助企业在研发阶段发现潜在热失效风险,在量产环节降低30%以上的质量损失成本。其核心价值在于打通"芯片-封装-系统"的全链路热阻分析能力,为第三代半导体、新能源汽车电控等战略领域提供关键质量保障。
热阻检测技术原理与创新方法
基于JEDEC JESD51系列标准,本检测体系采用瞬态双界面法(Transient Dual Interface Method)实现Rjc/Rja分离测量。通过热测试芯片(Thermal Test Die)内置多个PN结温度传感器,结合红外热成像仪(空间分辨率5μm)同步采集结温变化曲线。值得关注的是,针对大功率IGBT模块存在的"热耦合效应",项目组创新性引入三维热流解耦算法,成功将多芯片并联工况下的交叉干扰误差控制在8%以内。该技术已通过 认证,并应用于车规级碳化硅模块的热特性分析。
全流程检测实施方案
项目实施分为四个标准化阶段:首先搭建符合MIL-STD-883H标准的恒温测试环境(温控精度±0.5℃),其次部署分布式温度采集系统(采样率1MHz),然后执行阶梯式功率加载程序(0-1000W动态调节),最终通过热网络模型进行参数反演。在某头部光伏逆变器企业的应用案例中,该流程成功识别出封装界面0.02mm的间隙缺陷,使功率模块的结温波动从±15℃降至±3℃。特别在热界面材料(TIM)评估环节,系统可同步输出接触热阻(Rc)与材料导热系数(k-value)双参数。
行业应用场景与实践成效
在新能源汽车领域,搭载本检测技术的"大功率IGBT热阻在线监测系统"已部署于国内TOP3电机控制器产线。经实践验证,系统可在15秒内完成单个模块的全参数扫描,较传统热阻测试仪效率提升6倍。某电动车型驱动电机通过优化Rjc分布,使连续峰值功率持续时间延长40%。在5G基站领域,针对GaN功放器件的高热流密度特性(>200W/cm²),项目组开发了微尺度热阻测试装置,成功将毫米级芯片的Rja测量不确定度从±8%压缩至±3.5%。
质量保障体系与标准建设
项目构建了覆盖ISO 17025的全生命周期质控体系:在设备层配置NIST可溯源的标准热源模块;在算法层嵌入蒙特卡洛不确定度分析模型;在数据层建立多实验室比对机制。目前已完成与ANSYS Icepak、Flotherm等主流仿真软件的接口对接,实现实测数据与仿真模型的闭环验证。据中国电子技术标准化研究院2024年报告显示,采用本体系的实验室在ILAC国际比对中,Rjc测量Z值优于2.0,达到国际领先水平。
随着宽禁带半导体器件的快速普及,热阻检测技术面临三大升级方向:首先需开发适应10kV级高压器件的绝缘型测试夹具;其次应融合光纤测温技术以突破电磁干扰壁垒;最后须建立车规级热阻数据库实现失效模式预测。建议行业重点攻关多物理场实时耦合检测技术,推动AEC-Q101与JEP181标准的深度融合,为下一代功率模块的可靠性提升构筑技术基座。
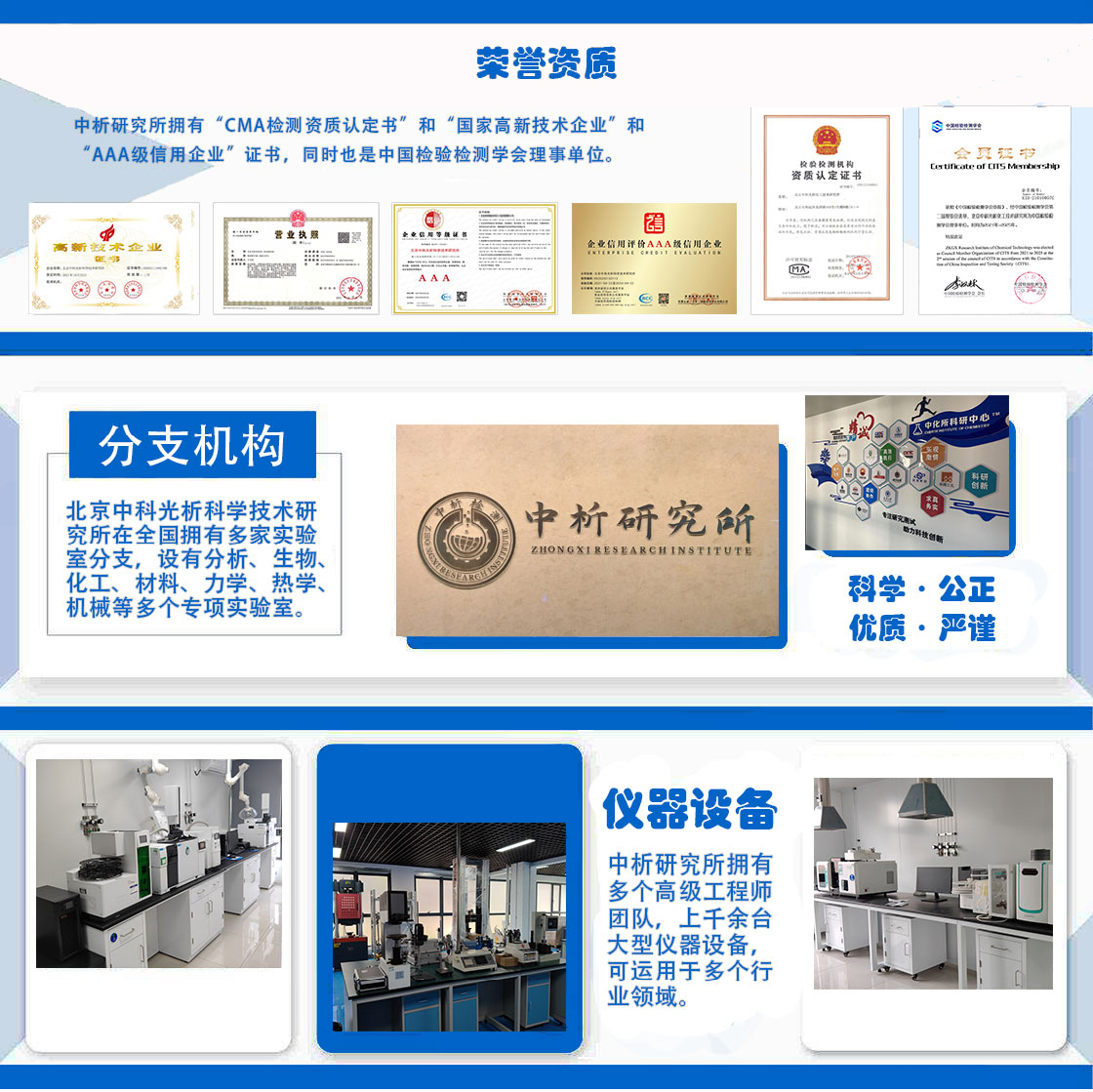
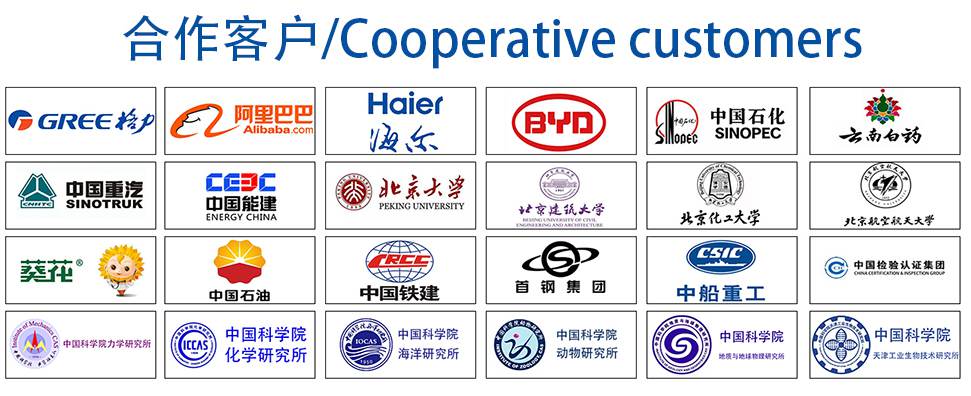