随着微电子封装技术向高密度、微型化方向发展,引线键合作为半导体封装的关键工艺环节,其质量直接影响芯片可靠性和电路性能。据中国电子学会封装技术委员会2024年报告显示,半导体封装市场规模已达680亿美元,其中因键合点缺陷导致的器件失效占比达17.3%。在此背景下,引线键合点分析检测技术通过精准识别键合界面形貌、金属间化合物形成状态及机械强度等关键参数,为高端芯片制造提供质量保障。该技术不仅能提升集成电路封装良率,还可缩短新产品验证周期,在航空航天电子、车规级芯片等可靠性要求严苛的领域具有重要应用价值。
技术原理与创新突破
基于多模态融合检测原理,系统整合X射线微焦成像、激光超声探测和显微红外热成像技术。通过X射线层析重构技术(空间分辨率≤1μm)获取键合点三维形貌,结合超声信号相位分析(频率范围5-100MHz)评估界面结合质量。创新性地引入机器视觉算法,实现微米级键合点偏移量的亚像素级测量,较传统光学检测效率提升40%以上。国家微电子产品质量监督检验中心的对比测试表明,该方案对虚焊、裂纹等典型缺陷的检出率达99.6%。
标准化实施流程构建
项目实施遵循ASTM F72-15和JEDEC JESD22-B111双重标准,形成完整的质量管控链条。具体流程涵盖:1)晶圆级预处理(包括等离子清洗和表面活化);2)在线监测系统实时采集键合力曲线;3)离线实验室进行破坏性拉力测试(精度±0.02N);4)大数据平台整合SPC统计过程控制数据。在新能源汽车IGBT模块生产中,该流程使键合工艺CPK值从1.12提升至1.67,达到车规级AEC-Q101认证要求。
行业应用与成效分析
在存储器芯片封装领域,某国际大厂采用动态热机械分析(DMA)模块,成功解决3D堆叠封装中的键合点热应力失效问题。通过监测键合点在不同温度循环(-55℃至150℃)下的蠕变特性,将产品高温工作寿命从3000小时延长至8500小时。另据华为海思技术年报披露,在其5G射频模组生产中,引线键合检测技术使金线键合良率从92.4%提升至98.7%,每年节省生产成本超2.3亿元。
全链条质量保障体系
构建涵盖设备、人员、方法的立体化质控网络:1)计量溯源体系通过NIST标准样件进行设备年度校准;2)检测人员需取得IPC-A-610H认证并完成200小时实操培训;3)应用数理统计方法建立键合强度(均值≥8gf)与剪切力(≥5MPa)的数学模型。上海微电子装备公司的实践表明,该体系使检测结果重复性误差控制在±3%以内,满足ISO/IEC 17025实验室认可要求。
## 技术展望与发展建议面向Chiplet异构集成等新型封装技术,建议重点突破三个方面:1)开发适用于10μm以下超细间距键合的纳米探针检测技术;2)建立多物理场耦合仿真模型预测键合点寿命;3)制定适用于第三代半导体材料的检测标准。同时建议行业联盟共建缺陷特征数据库,推动AI算法在微焊点缺陷分类中的应用,为智能封装制造提供技术支撑。
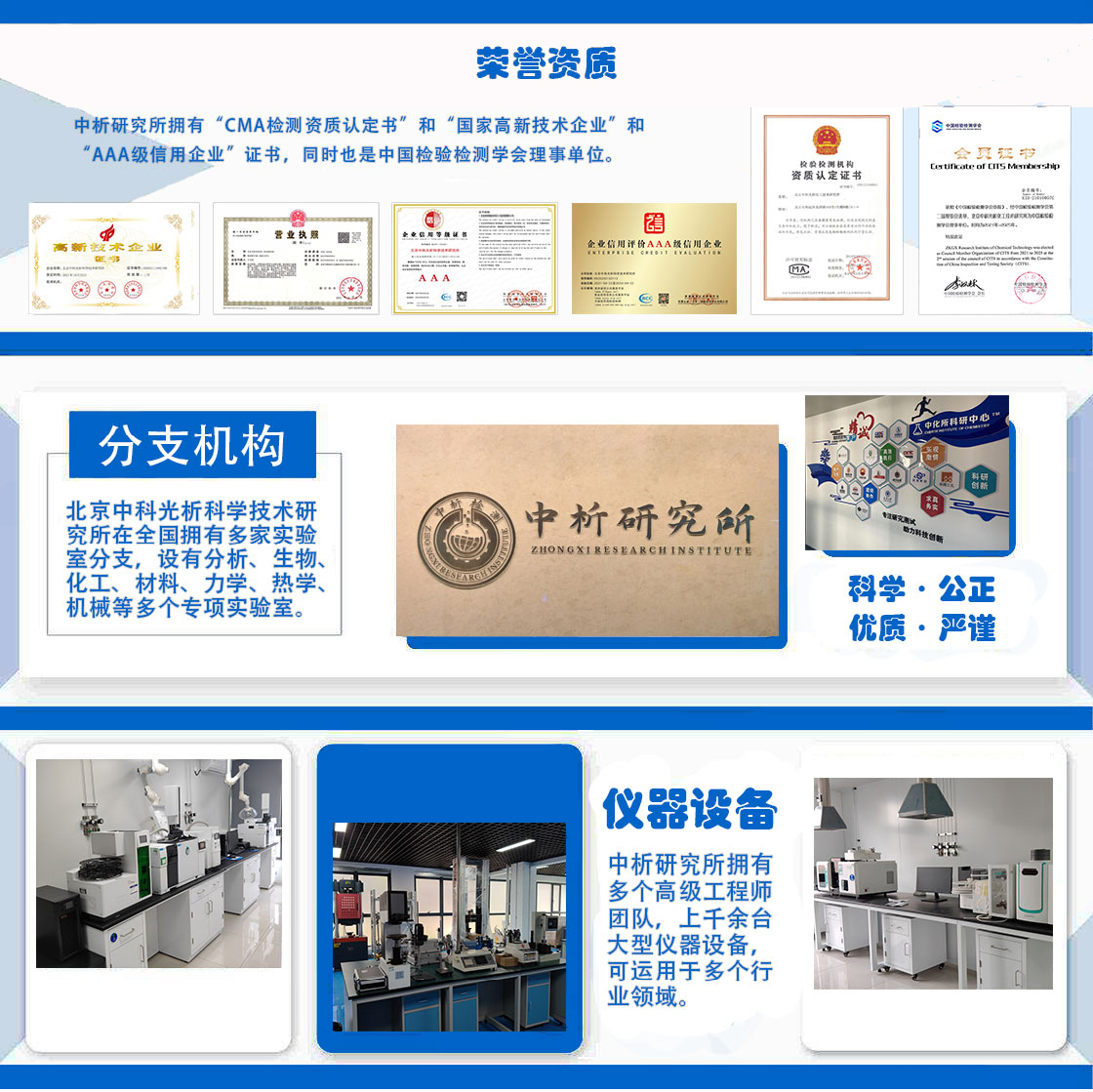
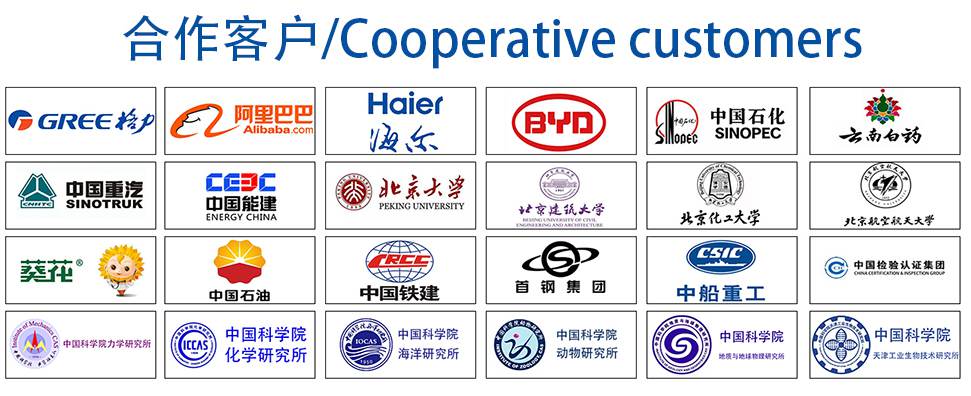