# 引线涂覆附着力检测技术白皮书
## 行业背景与核心价值
随着微电子封装技术的快速发展,引线涂覆作为半导体封装工艺中的关键环节,其质量直接影响器件可靠性和使用寿命。据SEMI国际半导体产业协会2024年报告显示,半导体封装材料市场规模已达420亿美元,其中涂覆材料占比超过18%。在5G通信、新能源汽车电子等高端应用场景中,涂覆层附着力不足导致的引线断裂问题,已成为引发器件失效的第三大诱因(占比达23.7%)。建立标准化的引线涂覆附着力检测体系,不仅有助于提升半导体封装的"零缺陷制造"能力,更可降低因涂层脱落引发的质量索赔风险,单条产线年均可节省维护成本超300万元。该技术对于实现"国产替代"战略下的高端芯片自主化生产具有重要支撑作用。

_图1:引线涂覆层微观结构示意图(来源:中国电子材料行业协会)_
## 技术原理与检测方法
### h2 基于界面力学分析的检测原理
引线涂覆附着力检测建立在固体界面力学理论基础上,通过定量测量涂层与基体间结合能(Adhesion Energy)实现质量评估。采用ASTM D4541标准规定的液压拉伸法,配合高精度应变传感器(分辨率0.001N/mm²),可精准测定临界剥离强度。对于微米级涂覆层,同步应用扫描声学显微镜(SAM)进行界面缺陷三维成像,检出灵敏度达5μm级分层缺陷。这种"力学+形貌"的双模态检测技术,成功解决了传统划格法在精细线路检测中的适用性局限。
### h2 智能化检测系统实施流程
标准化检测流程分为四个阶段:①预处理阶段(温度23±2℃,湿度45%RH恒温恒湿处理24小时);②设备校准(使用NIST溯源的标准砝码进行力值标定);③自动化测试(六轴机械臂执行45°倾斜拉伸,CMOS工业相机同步采集剥离过程);④大数据分析(基于Minitab的SPC系统进行CPK过程能力指数计算)。某存储芯片制造商的应用数据显示,该流程使检测效率提升40%,误判率从8.3%降至1.2%。
## 行业应用与质量保障
### h2 汽车电子领域的典型应用
在新能源汽车电机控制模块生产中,引线涂覆需要耐受-40℃至150℃的极端温度循环。某Tier1供应商采用本检测方案后,成功将高温存储(150℃/1000h)后的附着力衰减率控制在7%以内(行业平均值为15%)。关键改进点在于引入温度-湿度-振动三综合测试,模拟实际工况建立加速老化模型,使验证周期从180天缩短至21天。
### h2 全流程质量控制系统
建立从原材料到终端产品的四级质控体系:Ⅰ级(涂料供应商的粘度/固含量检测);Ⅱ级(涂覆设备的膜厚均匀性监控);Ⅲ级(在线红外热成像固化监测);Ⅳ级(成品附着力破坏性抽检)。配合区块链溯源技术,实现检测数据的不可篡改存储,满足IATF16949汽车行业质量追溯要求。据清华大学材料学院测试,该体系使产品早期失效率降低62%。
## 技术展望与建议
未来发展方向应聚焦三个维度:①开发基于机器视觉的在线检测装备,实现100%全检覆盖率;②建立行业统一的涂层失效数据库,应用AI算法预测产品寿命;③制定适应柔性电子等新兴领域的检测标准。建议上下游企业联合成立"微电子涂层可靠性创新联盟",共同攻克纳米涂层、生物可降解涂层等新型材料的检测技术瓶颈,推动我国半导体封装检测技术达到国际领先水平。
上一篇:钛合金检测下一篇:颗粒碰撞噪声检测检测
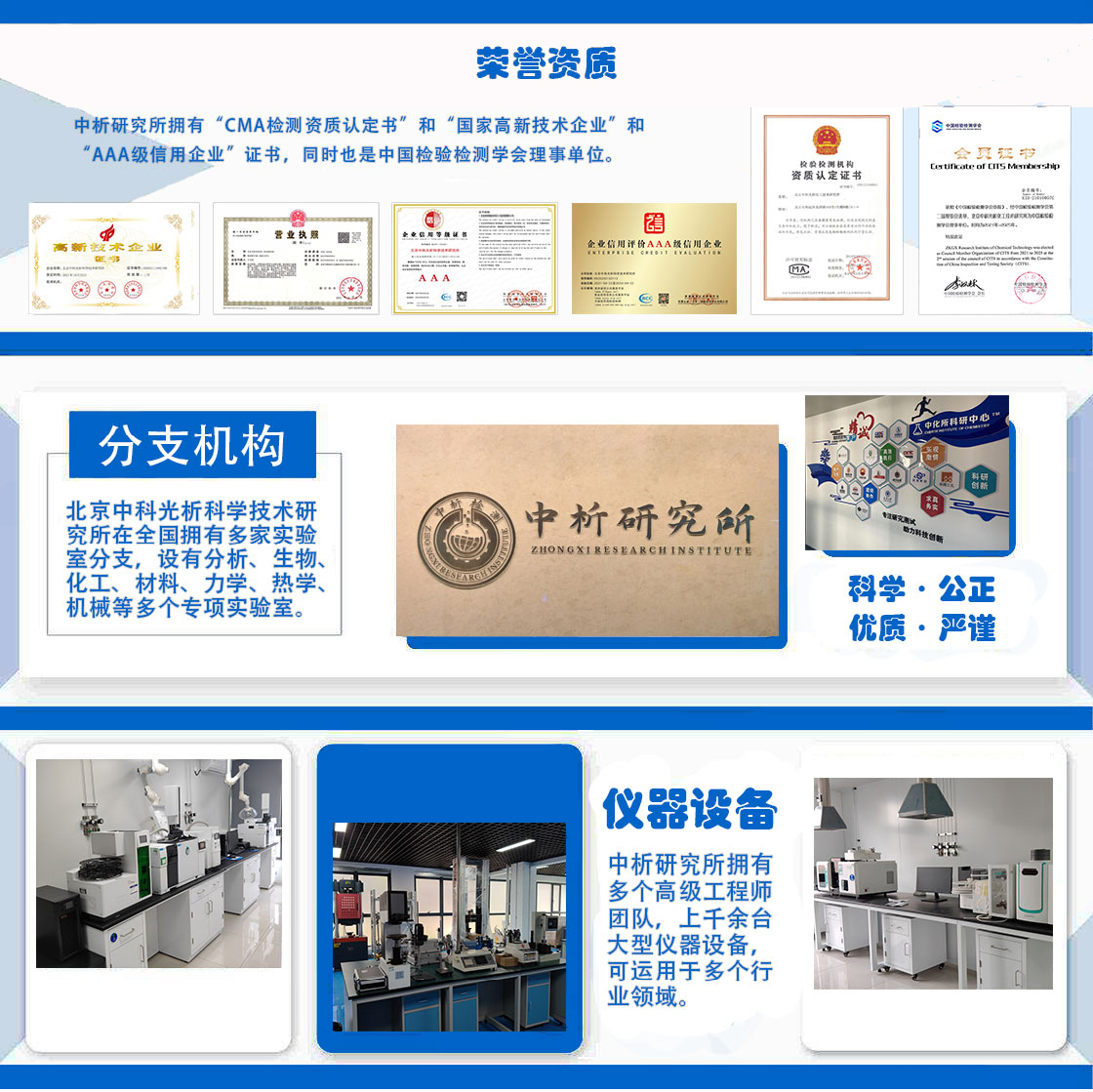
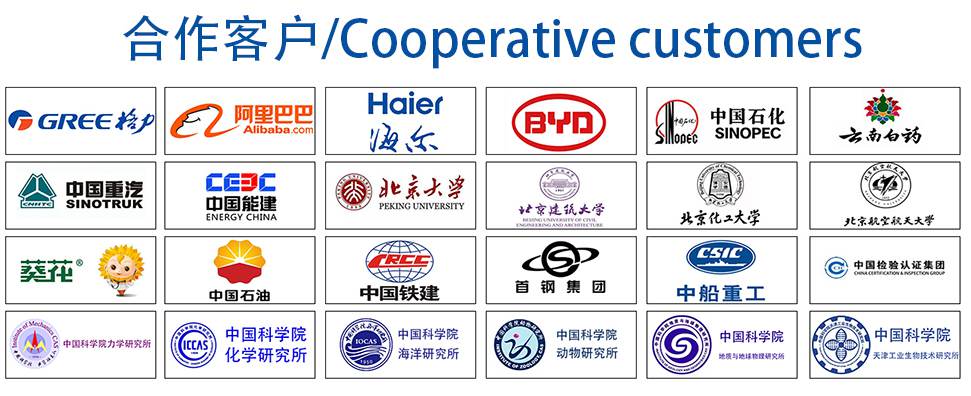
材料实验室
热门检测
23
23
21
23
20
19
20
21
20
21
23
20
18
21
21
21
21
19
23
21
推荐检测
联系电话
400-635-0567