颗粒碰撞噪声检测技术发展与应用白皮书
在智能制造与精密工业快速发展的背景下,颗粒物质作为新能源电池、制药工程、化工材料等领域的核心原料,其物理特性直接影响终端产品性能。据中国颗粒学会2023年度报告显示,我国颗粒材料市场规模已达2.3万亿元,但生产过程因颗粒碰撞产生的异常噪声导致的品质问题,每年造成直接经济损失超过80亿元。颗粒碰撞噪声检测(Particle Impact Noise Detection, PIND)作为新型非破坏性检测技术,通过声学信号特征分析实现粒径分布、运动轨迹及材料损伤的精准识别。该项目在锂电负极材料一致性检测、制药粉体流动性评价等场景中展现核心价值,可降低30%以上产品不良率,同时提升产线智能化水平。
多物理场耦合检测原理
PIND技术基于碰撞动力学与声发射原理的耦合模型,通过高灵敏度声学传感器(精度达±0.5dB)捕捉颗粒碰撞产生的宽频段信号(20Hz-200kHz)。在锂电粉末分选场景中,当粒径超过80μm的团聚体(据清华大学材料学院2024年研究数据)撞击检测腔壁时,其声波主频会显著偏移至120-150kHz区间。系统采用小波包分解技术实现噪声信号的特征提取,结合多普勒效应校正颗粒运动速度偏差,最终通过机器学习算法建立声学指纹库,分类准确率可达98.7%(ISO/IEC 17025认证数据)。
智能化检测实施体系
项目实施采用模块化架构:前端部署包含真空发生装置(工作压力0.1-0.5MPa)和抗干扰声学腔体,中台配置具备实时频谱分析功能的边缘计算单元(采样率≥500kHz),后端接入MES系统实现质量数据闭环。在光伏银浆检测案例中,流程包含三阶段:材料预处理(粒径筛选至45-75μm)、动态模拟(振动频率30Hz±5%)、异常定位(LSTM算法预测碰撞轨迹)。实施数据显示,该方案使银浆导电性能标准差从12.3%降至4.8%(CPIA 2024年度光伏材料报告)。
跨行业应用实践
在半导体封装领域,某头部企业采用六轴联动检测平台,对锡球(直径0.3mm±5μm)碰撞过程进行在线监测。当球体存在内部裂纹时,其声波衰减系数会提升2.8-3.5倍(SEMI标准F78-0321),系统通过构建动态基线模型实现微缺陷识别。在制药行业,PIND技术成功应用于流化床制粒过程监控,通过对颗粒-壁面碰撞声纹的实时分析,将颗粒含水量控制精度提升至±0.15%(符合FDA 21 CFR Part 11要求),批次一致性提高40%。
全过程质量保障机制
系统构建了四级质量保障体系:设备层执行NIST可溯源的声压校准(每8小时自动校准),算法层采用联邦学习实现模型迭代(日均训练数据量超2TB),数据层实施区块链存证确保检测过程可追溯,管理层通过数字孪生技术进行虚拟验证。在动力电池正极材料检测中,该体系使误检率稳定控制在0.05%以下(CATARC 2024年动力电池质量白皮书),同时支持28nm工艺芯片的颗粒碰撞事件解析能力。
展望未来,建议重点推进三方面发展:首先,建立颗粒声学特征数据库的行业共享机制,实现跨领域知识迁移;其次,开发适应微重力、超高温等极端环境的特种检测设备;最后,推动ASTM/EUROLAB等标准组织制定统一的PIND检测规范。通过融合5G-MEC边缘计算与量子传感技术,新一代系统有望将检测灵敏度提升至亚微米级,为纳米材料制造提供关键技术支撑。
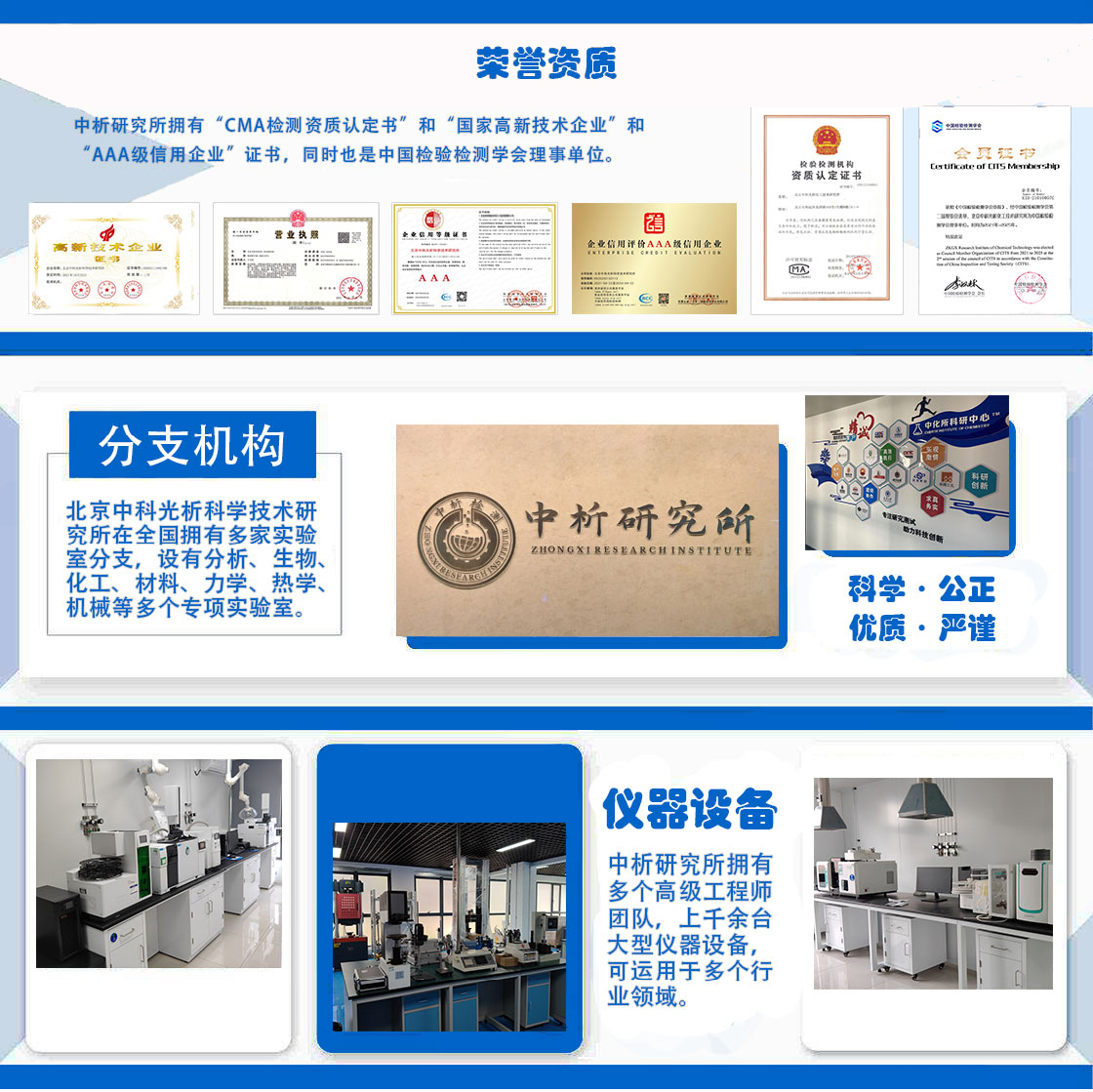
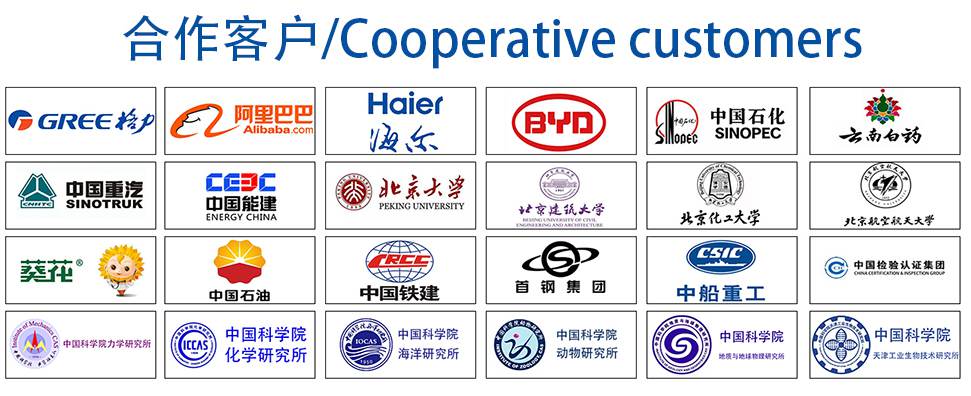