轴类零件检测技术体系与核心项目解析
在机械制造领域,轴类零件作为动力传动的核心载体,其质量直接影响设备的运行精度和使用寿命。据统计,机械装备故障中约35%与传动轴失效相关,这使得轴类零件检测成为现代制造业质量控制的关键环节。轴类零件检测通过系统化的测量手段,对零件尺寸公差、形位精度、表面完整性及材料特性进行全方位验证,确保其满足设计规范和使用要求。随着智能制造技术的发展,现代检测体系已形成包含光学测量、三坐标扫描、无损探伤等多元化技术融合的解决方案。
一、几何尺寸精度检测
几何尺寸检测是轴类零件质量控制的基础环节。使用精密千分尺、数显卡尺等量具对轴颈直径、轴肩高度、键槽宽度等关键尺寸进行测量,误差需控制在±0.005mm以内。对于高精度传动轴,需采用三坐标测量机(CMM)进行三维空间坐标采集,通过点云数据重构实现全尺寸数字化检测。特别关注轴承配合面的尺寸链计算,确保装配时的过盈配合或间隙配合符合设计要求。
二、形位公差综合检测
形位公差检测针对轴的几何特征进行定量分析,包含圆度、圆柱度、同轴度、跳动度等核心指标。采用圆度仪测量主轴颈的轮廓偏差,评价其径向跳动量;使用激光干涉仪检测轴向全长的直线度误差;对于阶梯轴的各段轴颈,需通过V型块配合百分表进行同轴度检测。现代检测系统可自动生成形位误差色谱图,直观显示超差区域。
三、表面完整性评估
表面质量直接影响轴的耐磨性和疲劳强度。采用表面粗糙度仪测量Ra、Rz参数,精密磨削表面Ra值应控制在0.4μm以下。磁粉探伤或涡流检测用于发现表面微裂纹,荧光渗透检测可识别0.02mm级缺陷。对于高频淬火或渗碳处理的轴件,需通过显微硬度计检测硬化层梯度分布,确保表面硬度达到HRC58-62的技术规范。
四、材料性能验证
通过光谱分析仪进行材料成分检测,验证合金元素含量是否符合牌号标准。万能材料试验机执行拉伸测试,获得屈服强度、抗拉强度等力学参数。金相显微镜观察微观组织,评估热处理工艺效果。对于高速运转轴件,还需进行X射线残余应力检测,预防应力集中导致的变形失效。
五、动态性能测试
在模拟工况下进行动平衡测试,采用动平衡机测量不平衡量,通过去重法将残余不平衡量控制在G2.5等级以内。振动测试系统采集运转时的频谱特征,分析临界转速和共振风险。对于汽车传动轴等旋转部件,需进行扭转疲劳试验,验证其承受交变载荷的能力。
通过构建覆盖设计、加工、装配全周期的检测体系,现代制造业已实现轴类零件质量控制的数字化闭环。采用智能检测装备与MES系统的深度集成,检测数据实时上传至质量数据库,为工艺优化提供数据支撑。这种全方位的检测策略不仅能有效预防质量缺陷,更能推动轴类零件制造向精密化、智能化方向发展。
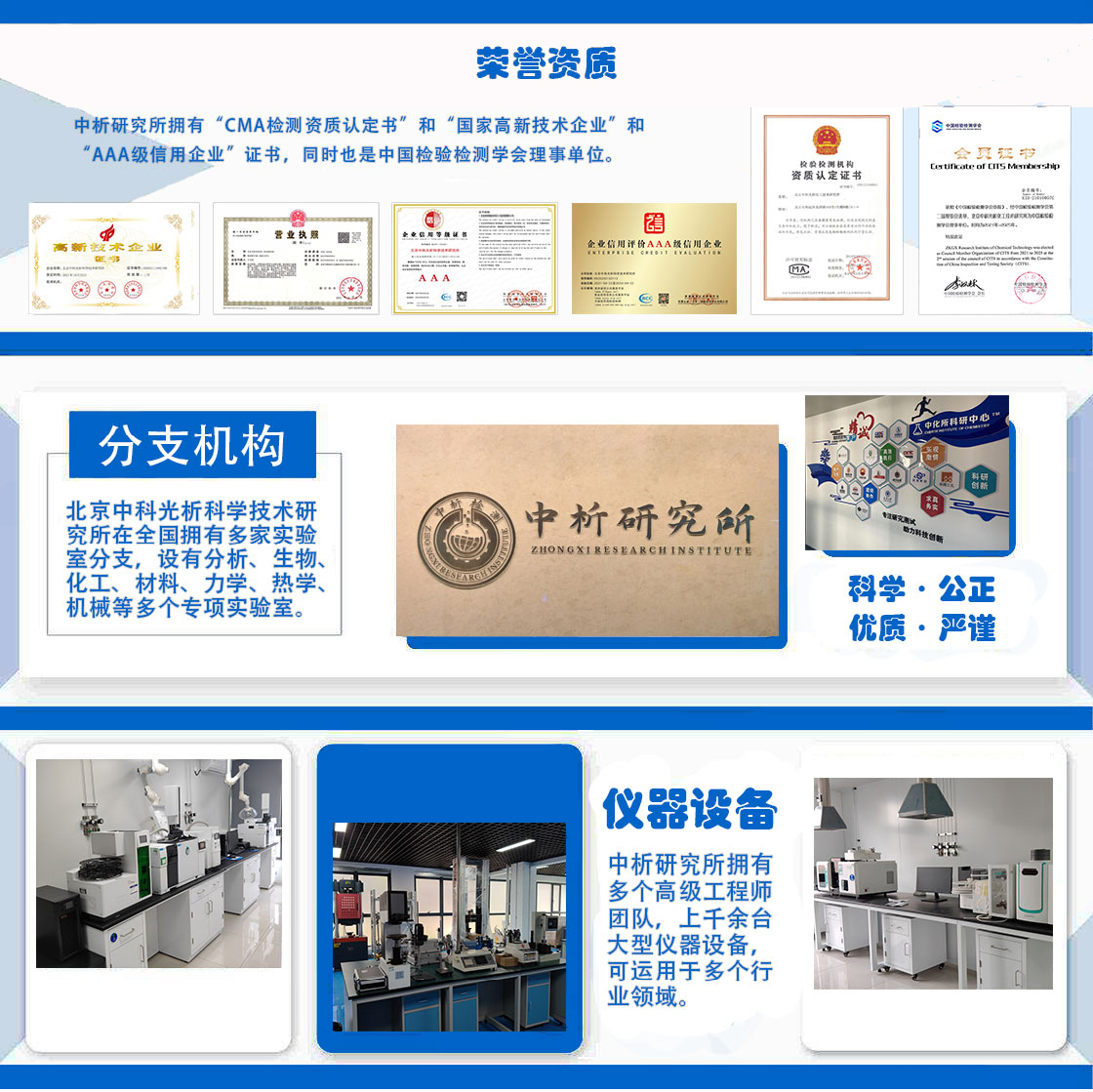
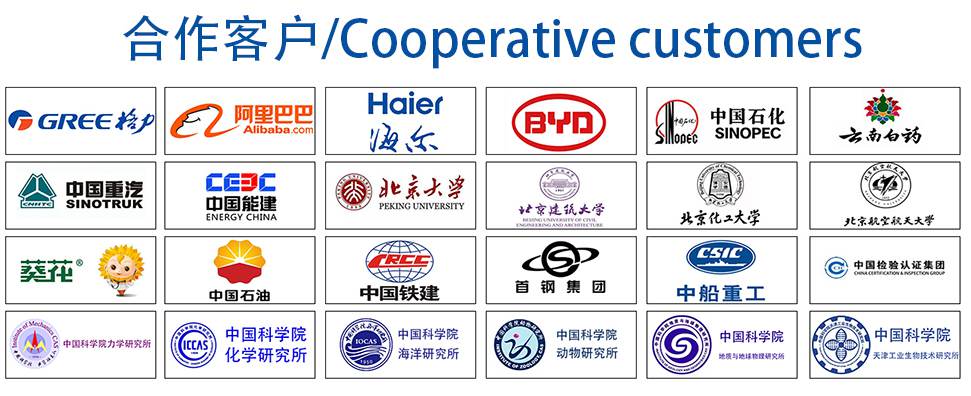