航空紧固件检测:守护飞行安全的核心环节
航空紧固件作为飞机结构连接的关键部件,承担着传递载荷、保障气动外形稳定性的重要使命。从发动机叶片到机翼蒙皮,从起落架到舱门铰链,数以万计的螺栓、铆钉、螺钉等紧固件构成了现代飞机的"骨架网络"。根据波音公司统计,一架商用客机平均使用超过300万件紧固件,其质量直接关乎飞行安全。航空紧固件检测通过系统性技术手段,确保这些微小零件在极端温度、高压、振动等复杂工况下依然保持可靠性能,是航空装备制造与维护中不可或缺的环节。
核心检测项目体系
1. 力学性能测试
通过拉伸试验机测定抗拉强度、屈服强度和延伸率,验证材料是否符合AMS/AS/GB等标准要求。例如钛合金螺栓需满足抗拉强度≥1100MPa,铝合金铆钉需完成剪切强度测试。配套进行硬度测试(洛氏/布氏硬度法)和扭矩-预紧力关系试验,模拟实际装配工况。
2. 尺寸精度检测
采用三坐标测量机(CMM)进行全尺寸扫描,公差控制达到±0.005mm级别。重点检测螺纹中径、螺距、牙型角等参数,使用GO-NO GO量规进行快速筛选。针对异形紧固件,需建立三维数字模型进行形位公差比对。
3. 表面质量检查
借助电子显微镜(SEM)和能谱仪(EDS)分析表面镀层(如镀镉、镀锌)的厚度均匀性,检测微裂纹、折叠等缺陷。按照NASM 1312标准进行盐雾试验,评估耐腐蚀性能。同时检查涂层附着力,采用划格法测试达到ASTM D3359 B级标准。
4. 材料成分分析
运用光谱分析仪对Inconel 718、Ti-6Al-4V等航空合金进行元素定量分析,确保C、O、N等杂质含量符合AMS 4928/4930规范。金相显微镜观察晶粒度等级,检测是否存在偏析、夹杂等冶金缺陷。
5. 环境适应性测试
在气候箱中模拟-55℃~150℃温度循环,验证热膨胀系数匹配性。进行振动台试验,按照RTCA DO-160标准完成10~2000Hz扫频测试。湿热试验要求紧固件在95%RH环境中持续500小时无性能衰减。
6. 无损检测技术
应用渗透检测(PT)发现表面微裂纹,磁粉检测(MT)用于铁磁性材料近表面缺陷探测。针对内部缺陷,采用工业CT进行三维成像,分辨率可达1μm。涡流检测(ET)在线监控螺纹根部疲劳裂纹,检测效率提升60%。
7. 防腐蚀性能验证
执行ASTM B117中性盐雾试验,评估镀层/涂层的耐蚀等级。对于复合材料紧固件,需通过电偶腐蚀试验验证与异种金属接触时的相容性。氢脆敏感性测试采用缺口拉伸法,保持载荷持续200小时无断裂。
8. 疲劳寿命评估
在伺服液压疲劳试验机上开展轴向循环加载,建立S-N曲线预测使用寿命。基于损伤容限设计理念,采用断裂力学方法计算临界裂纹尺寸。针对发动机用紧固件,需额外进行高频振动疲劳试验(200Hz以上)。
9. 安装工艺验证
通过应变计测量预紧力离散度,优化扭矩-转角控制策略。使用超声波测长仪监控紧固件伸长量,确保夹紧力一致性。开发智能安装工具,实时采集并分析20+项装配参数,预防过拧/欠拧缺陷。
质量控制的数字化升级
随着工业4.0技术发展,航空紧固件检测正加速向智能化转型。基于机器视觉的自动分拣系统可实现0.1mm级缺陷识别,大数据平台整合SPC统计过程控制数据,AI算法预测设备维护周期。数字孪生技术构建虚拟检测环境,使新产品开发周期缩短40%。通过贯穿全生命周期的质量数据链,航空紧固件的平均缺陷率已降至0.3ppm以下。
从原材料入厂到装机使用,航空紧固件检测覆盖18类200余项技术指标,形成严密的"过程控制+终端验证"体系。随着适航规章的持续完善(如CCAR-25-R4第25.981条款更新),检测技术将持续迭代,为航空安全构筑坚实的技术防线。
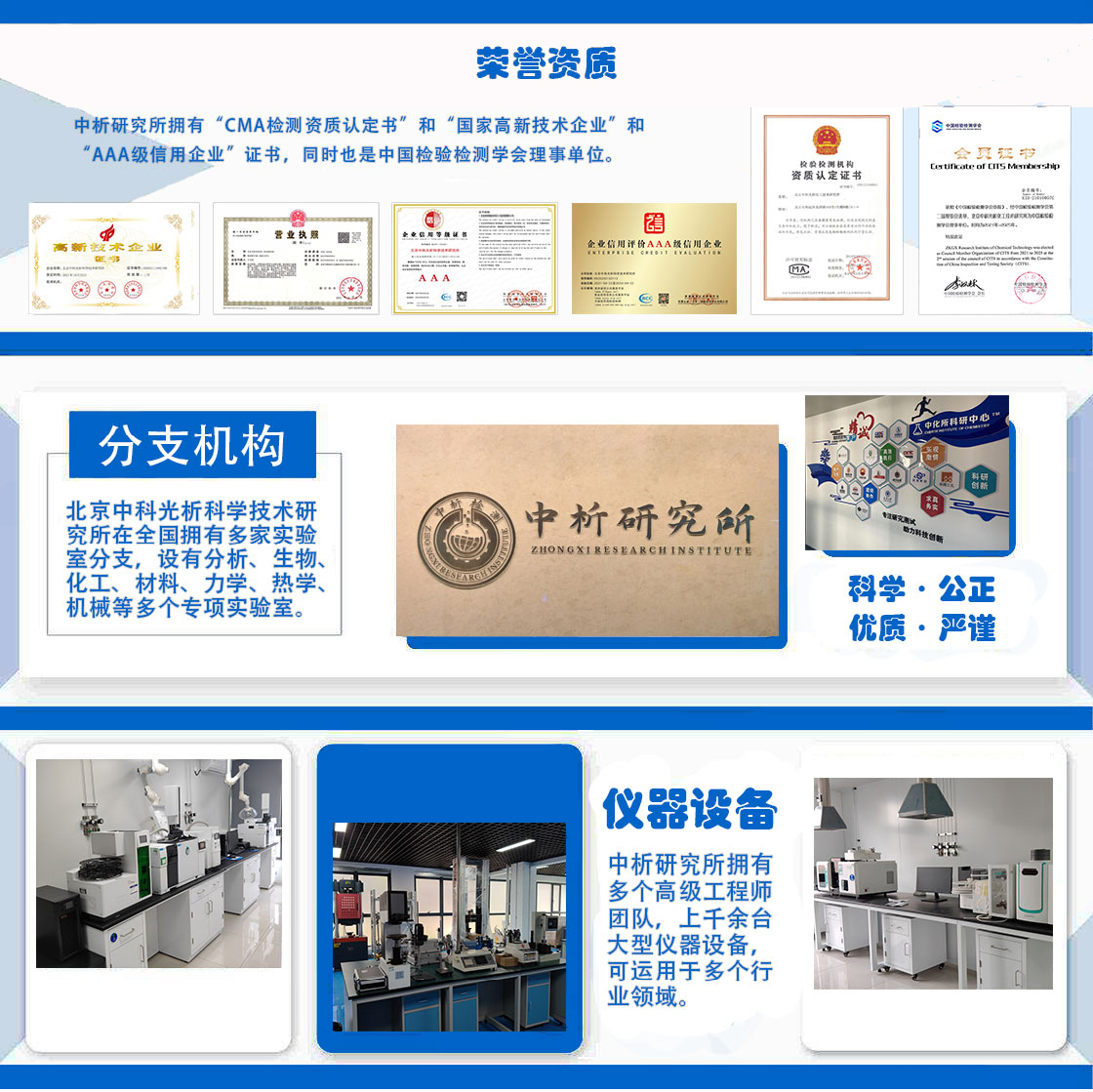
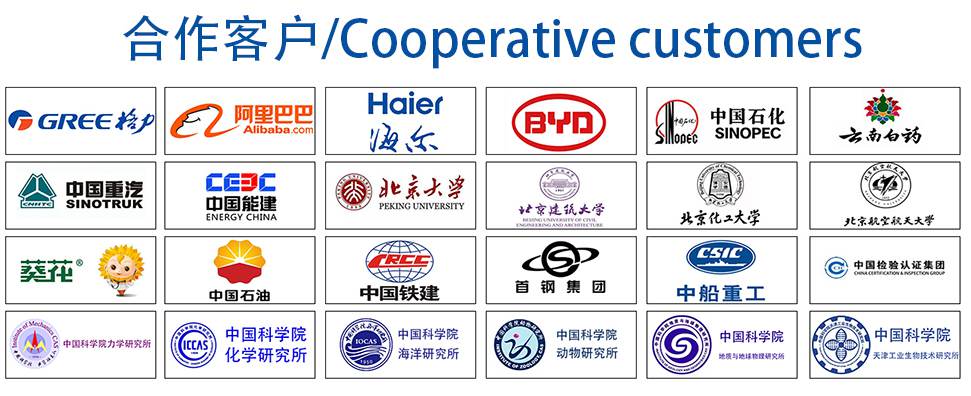