机械式分动器的核心作用与检测必要性
机械式分动器作为四驱车辆动力分配系统的核心部件,承担着将发动机动力按需传递至前后驱动轴的重要任务。其性能直接关系到车辆的越野能力、传动效率及行驶安全性。在复杂工况下,分动器长期承受高扭矩、频繁换挡冲击以及外部环境侵蚀,内部齿轮组、轴承、拨叉等关键部件易出现磨损、变形或润滑失效等问题。因此,定期开展系统化检测不仅能预防突发故障,还能延长分动器使用寿命,降低车辆维护成本。
机械式分动器的基本结构
典型机械式分动器由壳体、齿轮传动系统、拨叉机构、输出轴系和润滑系统组成,通过手动或电动切换实现两驱/四驱模式转换。其中,高速齿轮与低速齿轮的啮合精度、同步器磨损状态、轴系同轴度等参数是影响性能的关键因素。
机械式分动器核心检测项目
1. 外观与密封性检测
使用内窥镜及渗漏检测仪检查壳体裂纹、渗油痕迹;测量结合面平面度误差≤0.05mm;验证通气阀工作状态,确保内部压力平衡。
2. 齿轮啮合精度分析
采用三坐标测量仪测定齿轮齿形误差(≤0.02mm)、齿向偏差(≤0.015mm);通过红丹粉接触印痕试验验证啮合面积(≥85%);检测齿侧间隙(0.10-0.25mm)。
3. 拨叉机构功能性测试
测量拨叉导轨磨损量(允许极限值0.3mm);检测换挡力曲线是否符合标准(20-50N);利用位移传感器记录换挡行程精度(±0.5mm)。
4. 轴系同轴度与轴承状态评估
使用千分表检测输入/输出轴径向跳动(≤0.03mm);采用超声波探伤仪排查轴承滚道剥落缺陷;测量轴向间隙(0.05-0.15mm)。
5. 润滑系统有效性验证
检测油液粘度变化(新油±15%范围内)、金属颗粒浓度(≤100ppm);通过流量计确认润滑油循环量(>2L/min);评估油泵输出压力(1.5-2.8bar)。
6. 动态负载试验
在台架测试中模拟最大扭矩的120%负载(持续30分钟),检测温升(≤85℃)、振动加速度(≤4.5m/s²);记录异常噪音(声压级≤78dB)。
智能化检测技术的发展趋势
当前行业已开始应用基于振动频谱分析的故障预警系统,通过AI算法识别齿轮早期点蚀特征;红外热成像技术可实时监测轴承温升梯度;而数字孪生模型则能模拟极端工况下的应力分布,为预防性维护提供数据支撑。
结语
完善的机械式分动器检测体系需融合传统测量方法与现代智能诊断技术,严格执行GB/T 5373-2023《汽车分动器台架试验方法》等行业标准,才能确保检测结果的准确性与可靠性,为车辆动力系统的稳定运行提供坚实保障。
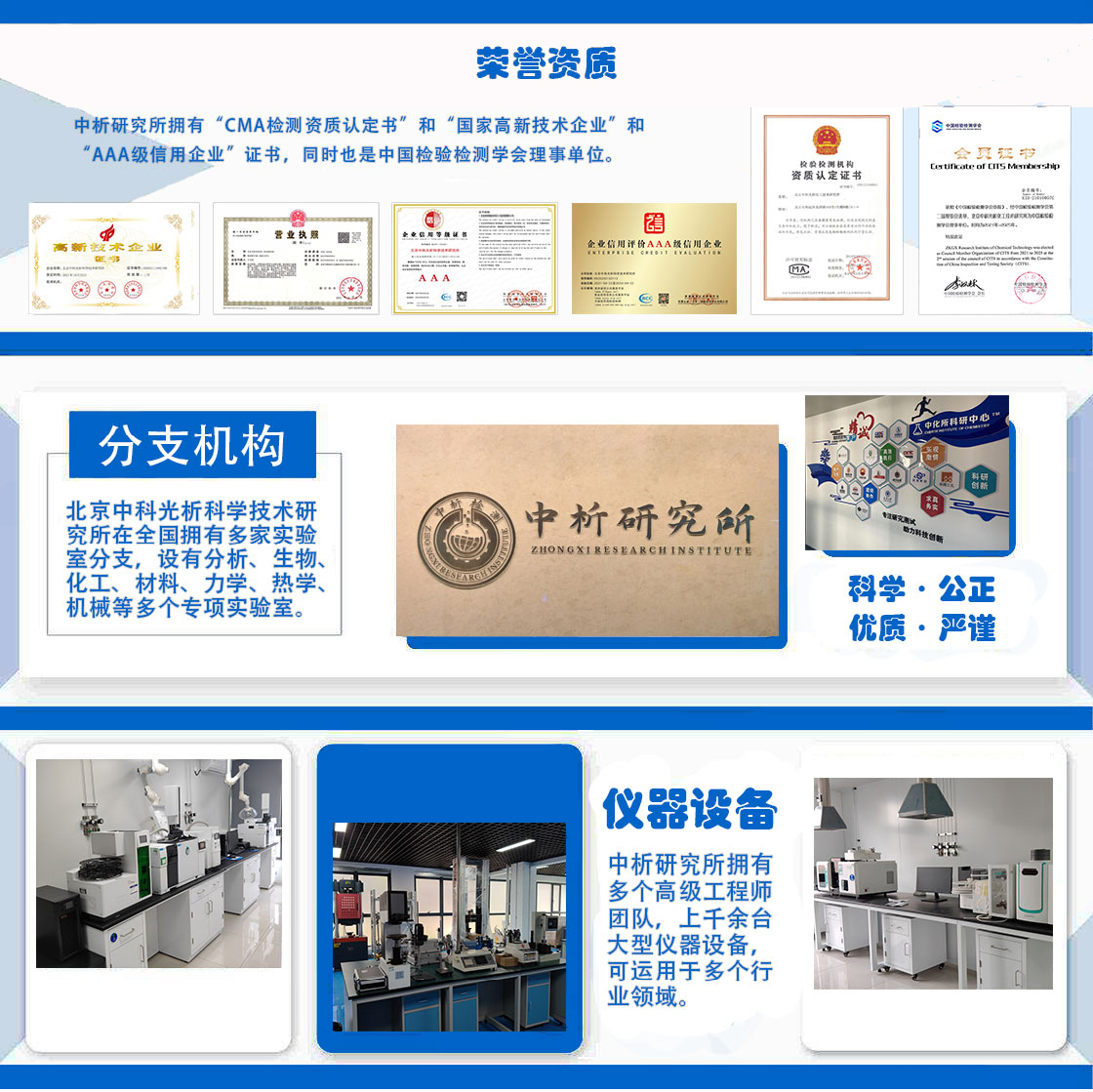
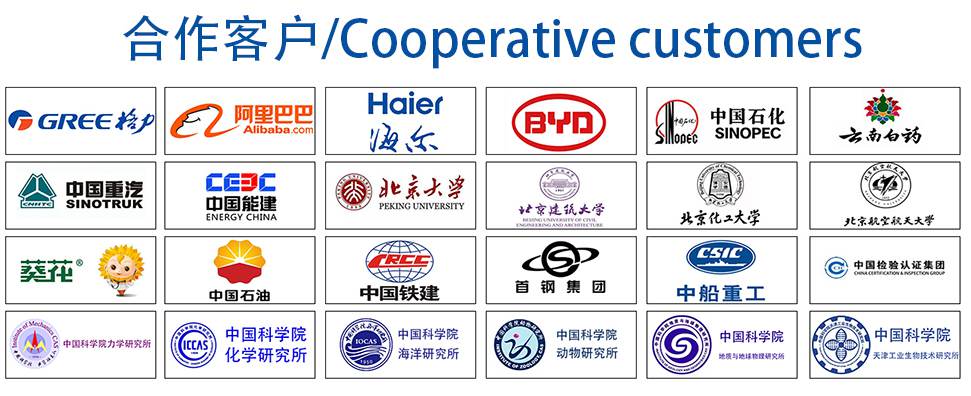