液压离合器传动缸检测项目及方法详解
液压离合器传动缸作为车辆动力传输系统的核心部件,其性能直接关系离合器的操作灵敏度与行车安全。在使用过程中,因油液泄漏、密封老化或机械磨损等原因可能导致传动效率下降甚至失效。为确保其长期稳定运行,需通过系统性检测发现隐患。本文将重点介绍液压离合器传动缸的关键检测项目及实施规范。
一、密封性检测
通过目视检查缸体表面、接头处是否存在油渍,结合压力测试仪进行保压测试。将系统加压至1.5倍工作压力(通常2-3MPa),观察10分钟内压力降是否超过10%。若发现渗漏需更换密封圈或修复缸体划痕。
二、活塞行程测量
使用数显千分尺测量活塞全行程位移量,对比制造商标定值(常见为25-40mm)。当实测值偏差超过±2mm时,需检查复位弹簧弹力或排除液压系统气阻问题。
三、压力响应测试
在模拟工作状态下,采用压力传感器记录踩踏踏板时的压力建立曲线。正常系统应在0.3秒内达到额定压力(1.2-1.8MPa),若响应延迟超过0.5秒,需排查主缸供油量或油路堵塞情况。
四、油液质量分析
提取液压油样本进行三项检测:1) 含水量不得超过0.5%;2) 粘度变化率需在±15%范围内;3) 金属微粒含量每100ml应少于20mg。建议每2万公里或每年更换DOT4标准液压油。
五、缸体内壁磨损检测
使用内径千分表多点测量缸筒圆度误差,允许公差为0.02mm。当出现纵向拉痕深度超过0.1mm或局部腐蚀斑点时,需采用珩磨工艺修复或更换缸体组件。
通过上述检测可有效预防离合器打滑、分离不彻底等故障。建议每5万公里或大修时进行全面检测,特殊工况下(如频繁半联动)应缩短至3万公里检测周期。对于检测异常的部件,需严格按原厂标准进行维修或更换,确保系统恢复出厂性能指标。
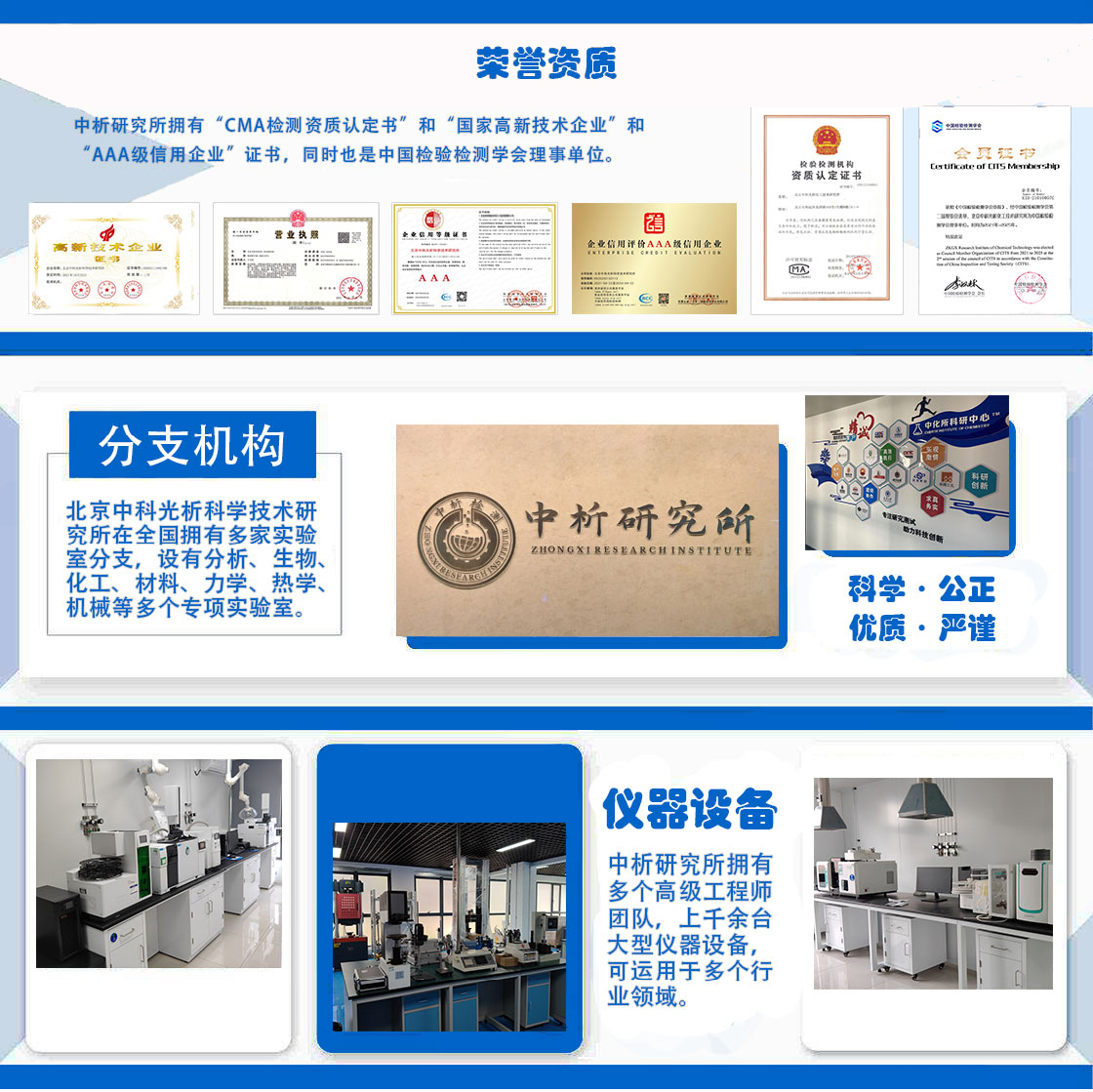
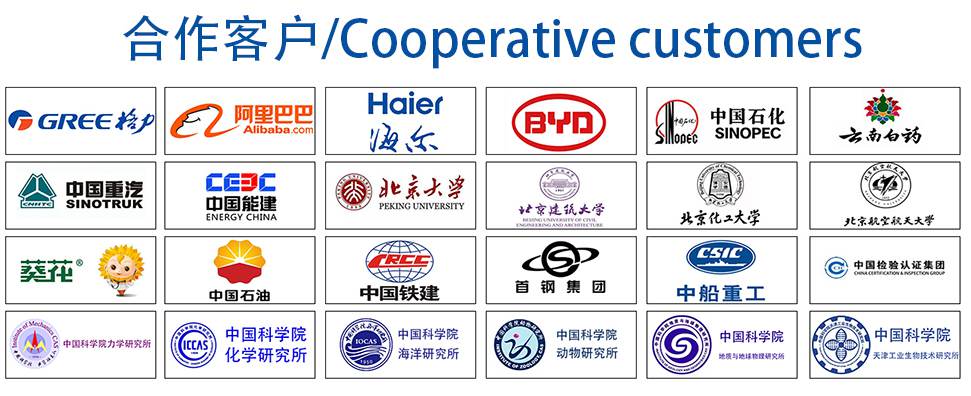