型材切割机检测项目及技术规范
型材切割机作为金属加工行业的核心设备,其性能直接关系到生产效率和产品质量。为确保设备安全运行、切割精度符合标准并延长使用寿命,需定期开展系统性检测。根据国家机械安全标准GB 13887-2019及行业规范要求,型材切割机的检测应涵盖机械结构、控制系统、安全防护、精度指标等核心模块,通过综合性技术评估实现设备全生命周期管理。
一、安全防护装置检测
重点检测急停按钮响应速度(≤0.5秒)、防护罩连锁装置有效性、漏电保护装置灵敏度。使用接地电阻测试仪测量设备接地电阻值(应≤4Ω),验证紧急制动系统在异常工况下的制动距离是否符合安全规程。
二、切割精度检测
采用激光跟踪仪和千分表进行三维精度测试,包括纵向切割直线度(≤0.1mm/m)、切口垂直度(≤0.05°)、重复定位精度(±0.02mm)。检测前需在标准试件(Q235钢板)上进行10次连续切割试验,评估设备热变形对精度的影响。
三、动力系统性能检测
使用功率分析仪测试主轴电机负载特性,检测额定功率波动范围(±5%内)、主轴径向跳动(≤0.01mm)、传动系统振动值(应<4.5mm/s)。同时对液压/气动系统进行保压试验,验证管路密封性及压力稳定性。
四、控制系统功能验证
通过PLC信号模拟检测各轴运动逻辑,验证数控系统G代码解析能力。测试自动润滑系统周期控制精度(±5秒)、刀具补偿功能有效性,以及人机界面报警功能的完整性(需覆盖32种以上故障类型)。
五、环境适应性检测
在模拟工况下进行连续8小时负载试验,监测设备温升(电机表面≤65℃)、噪音水平(≤85dB(A))、粉尘防护等级(IP54标准)。特殊环境还需测试设备在湿度90%RH、温度-10℃~45℃条件下的运行稳定性。
六、能耗效率评估
依据GB 19153-2019标准,使用电能质量分析仪测量空载/负载功耗比,计算单位切割长度能耗指标。评估节能模式下设备待机功率(应≤额定功率3%),并对切削液循环系统进行流量匹配度检测。
七、辅助功能检测
包括自动送料机构定位精度(±0.1mm)、废料收集系统密封性、除尘装置颗粒物过滤效率(PM2.5过滤≥95%)。同时验证设备与MES系统的数据交互功能,确保生产数据采集准确率≥99.9%。
八、设备寿命预测
通过振动频谱分析、润滑油金属颗粒检测等技术手段,评估关键部件(导轨、丝杠、轴承)磨损状态。结合累计运行时长和负载曲线,建立剩余寿命预测模型,为预防性维护提供数据支持。
完整的检测流程应包含初始状态记录、动态性能测试、数据比对分析三个阶段,最终形成包含80项以上参数的检测报告。建议每500小时运行或半年周期实施一次全面检测,对于高负荷工况需缩短至300小时检测周期,确保设备始终处于最优工作状态。
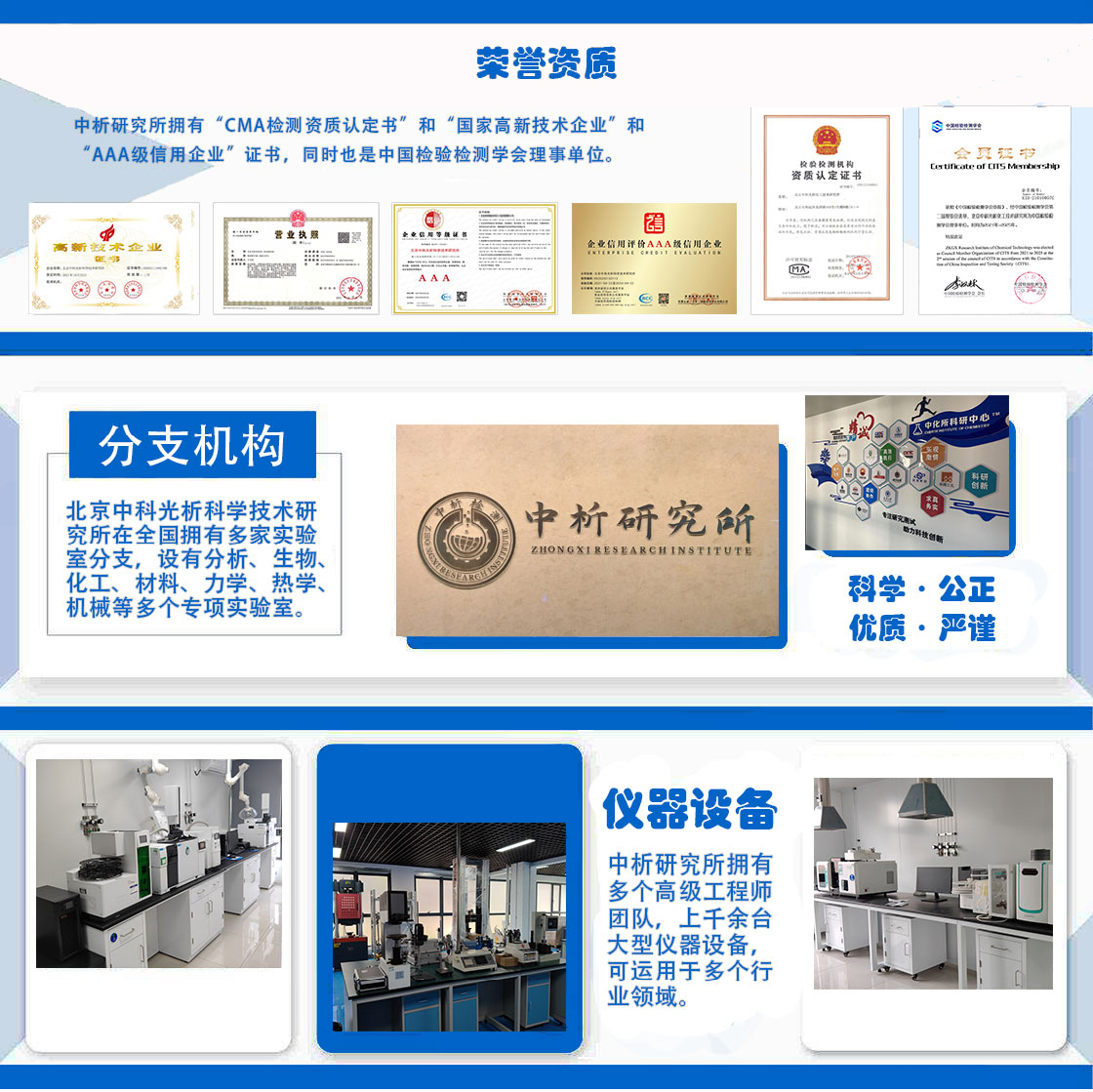
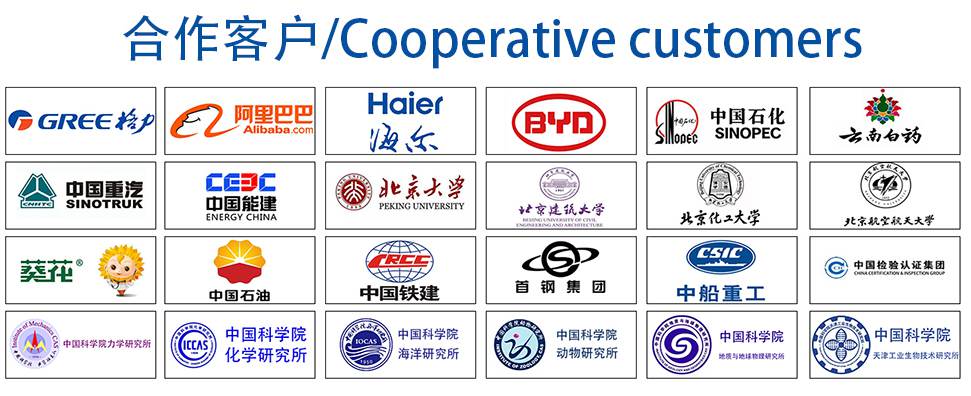