工业金属管道检测的重要性与必要性
工业金属管道作为石油、化工、能源、冶金等行业的重要传输载体,其安全性和可靠性直接影响生产系统的稳定性与人员安全。由于长期承受高温、高压、腐蚀性介质及机械应力,管道可能出现材质劣化、焊缝缺陷、腐蚀减薄等问题。若未及时发现隐患,可能引发泄漏、爆炸等严重事故,造成经济损失甚至环境灾难。因此,通过科学系统的检测手段对金属管道进行定期检验与状态评估,是保障工业安全运行、延长设备寿命、降低维护成本的核心环节。
工业金属管道主要检测项目
1. 材质与尺寸检测
通过光谱分析、硬度测试等方法验证管道材质的化学成分及力学性能是否符合设计标准,使用卡尺、测厚仪等工具测量管道厚度、直径等尺寸参数,确保其满足使用工况要求。
2. 腐蚀与壁厚检测
采用超声测厚技术(UT)对管道壁厚进行多点测量,结合电磁涡流检测(ECT)定位局部腐蚀区域。对于隐蔽部位,可使用射线检测(RT)或工业内窥镜进行内部腐蚀状况评估,建立腐蚀速率模型预测剩余寿命。
3. 焊接质量检测
针对焊缝实施X射线探伤(DR)、超声波探伤(UT)或磁粉探伤(MT),检测未熔合、气孔、裂纹等缺陷。相控阵超声检测(PAUT)可对复杂焊缝进行三维成像分析,提高缺陷检出率。
4. 应力与变形分析
通过声发射检测(AE)实时监测管道应力集中区域,结合激光扫描技术获取管道整体形变数据。对高温高压管道需进行蠕变损伤检测,采用金相显微镜观察材料微观结构变化。
5. 涂层与防腐层检测
使用电火花检漏仪检测防腐层完整性,通过附着力测试仪评估涂层结合强度。对于埋地管道,借助直流电压梯度法(DCVG)或密间隔电位测量(CIPS)判断防腐层破损点。
检测标准与技术创新
检测过程需遵循《GB/T 20801-2020压力管道规范》等国家标准,结合API 570、ASME B31.3等国际规范。近年来,数字射线成像(CR/DR)、导波检测(GW)、智能爬行机器人等新技术显著提升了检测效率和精度,为管道全生命周期管理提供数据支撑。
结语
工业金属管道检测是一项涉及多学科、多技术的系统性工程,需根据介质特性、运行环境及历史数据制定针对性方案。通过多维度检测数据的综合分析,企业可实现风险分级管控,为预防性维护和改造决策提供科学依据,最终构建安全、高效、可持续的工业管道管理体系。
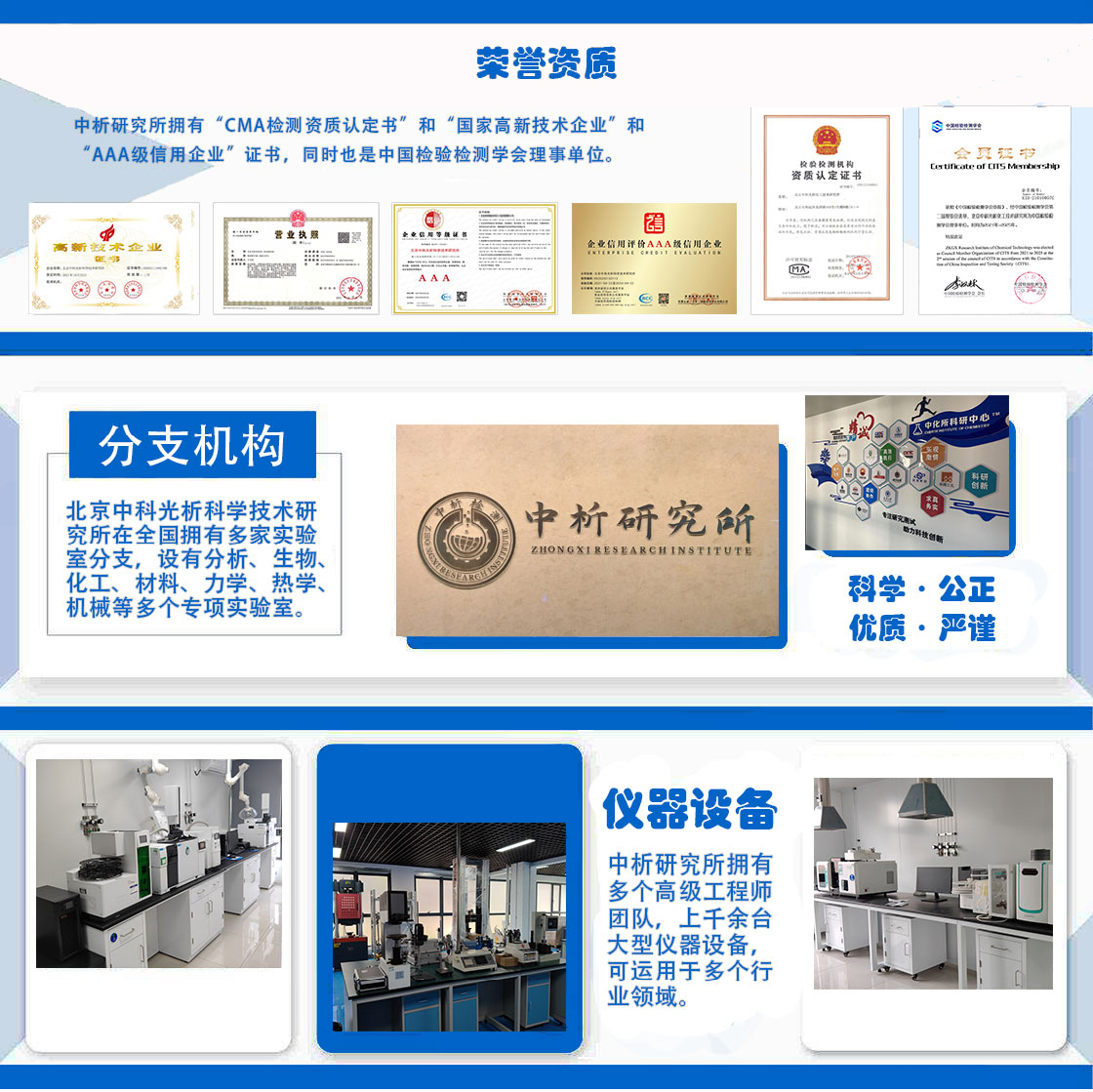
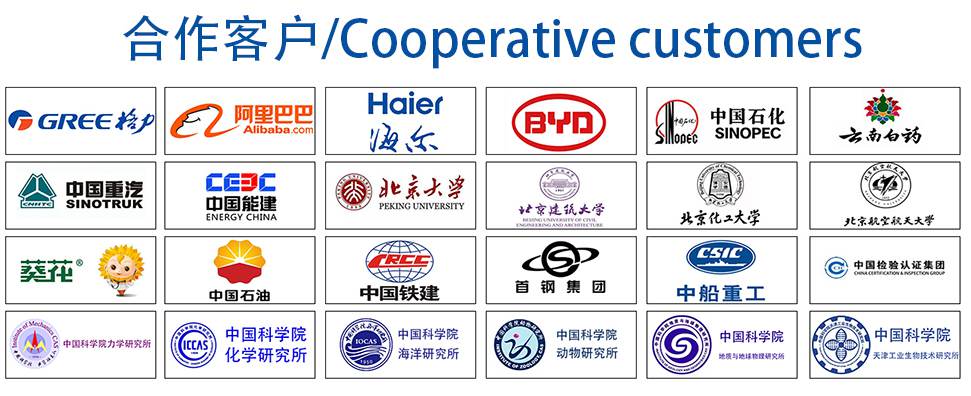