管道材料及配件检测的重要性与应用领域
管道系统作为工业生产和市政基础设施的核心组成部分,其材料及配件的质量直接影响着输送介质的安全性、系统使用寿命及运维成本。从石油化工到城市供水,从核电工程到燃气输送,管道材料需要承受高温高压、腐蚀介质、机械应力等多种复杂工况的考验。开展管道材料及配件检测不仅是工程验收的强制性要求,更是预防泄漏事故、保障公共安全的重要技术手段。根据GB/T 20801、ASME B31.3等国内外标准体系,检测需覆盖原材料性能、加工工艺、成品质量等全生命周期环节,通过科学的检测数据为工程质量提供可靠保障。
核心检测项目分类与内容
1. 材料物理性能检测
包括拉伸强度测试(测定屈服强度、抗拉强度、延伸率)、冲击试验(-40℃低温冲击韧性评估)、硬度测试(布氏/洛氏硬度法)、弯曲试验(验证材料塑性变形能力)。对于双金属复合管还需检测结合强度,通过剪切试验或超声波检测判定层间结合质量。
2. 化学成分分析
采用光谱分析法(OES)、X射线荧光光谱(XRF)对碳钢、不锈钢、合金钢等材质的C、Mn、Cr、Ni等元素含量进行精准测定,确保符合GB/T 14976、ASTM A312等材料标准要求。对PVC、PE等高分子材料则需检测添加剂含量及分子量分布。
3. 耐腐蚀性能测试
通过盐雾试验(中性/酸性环境)、晶间腐蚀试验(硫酸-硫酸铜法)、应力腐蚀试验(C形环法)等评估材料抗蚀能力。针对特殊介质需模拟工况开展高压釜腐蚀试验,检测周期腐蚀速率和点蚀倾向。
4. 密封性能验证
对法兰、阀门、管接头等配件进行气密性试验(氦质谱检漏法)和水压试验(1.5倍设计压力保压),检测阀座密封面的泄漏率。三通、弯头等管件需通过爆破试验验证极限承压能力。
5. 尺寸与几何精度检测
使用三坐标测量仪检测管件内径、壁厚均匀度、法兰平面度等形位公差,螺纹连接件需通过通止规检验螺纹配合精度。对焊接管件还需进行焊缝余高检测和坡口角度测量。
6. 环境适应性评估
针对埋地管道开展阴极剥离试验,评估防腐层粘结强度;对低温管道材料进行-196℃液氮冲击试验;高温工况材料需测试蠕变强度和持久强度等高温力学性能。
齐全检测技术应用趋势
随着技术进步,相控阵超声检测(PAUT)可实现焊缝缺陷三维成像,激光诱导击穿光谱(LIBS)实现现场快速成分分析,数字射线检测(DR)提升缺陷识别效率。智能化检测系统通过大数据分析实现质量预测,为管道全生命周期管理提供技术支撑。
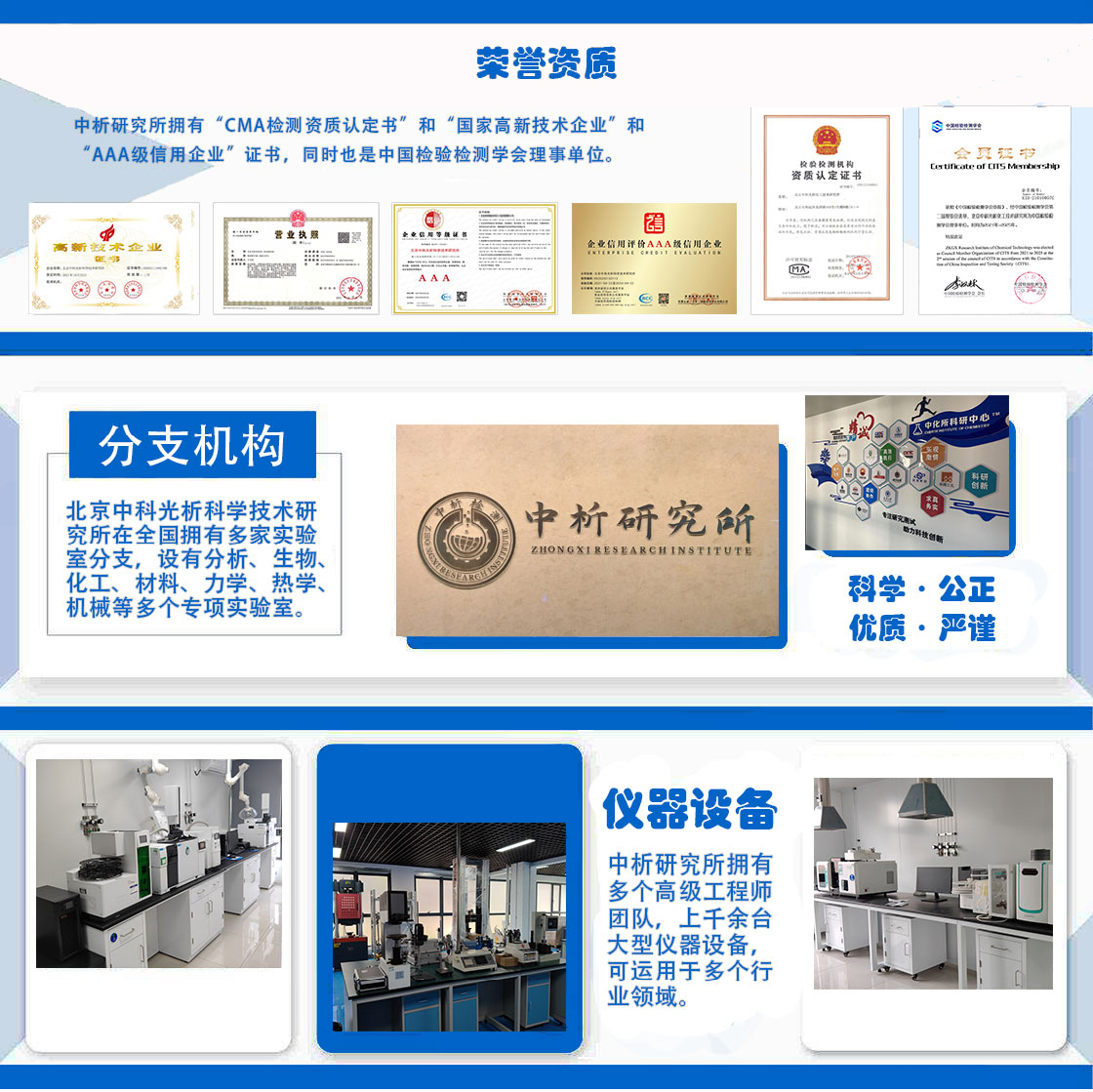
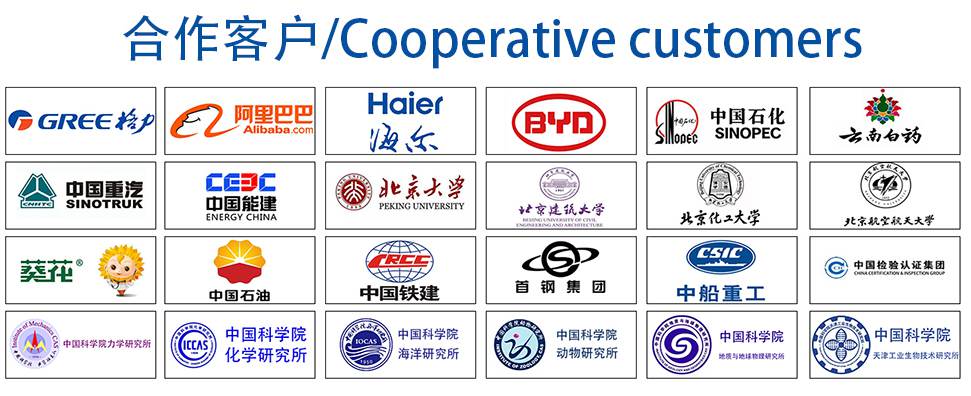