钢材、构件及焊缝检测的重要性
在建筑工程、桥梁工程、压力容器制造及重型机械领域,钢材、构件及焊缝的检测是保障工程安全性和耐久性的核心环节。钢材作为基础材料,其化学成分、力学性能和内部缺陷直接影响结构承载能力;构件加工过程中的尺寸精度、表面质量及组装工艺需符合设计要求;而焊缝作为连接钢材的关键部位,其内部气孔、裂纹或未熔合等缺陷可能成为结构失效的隐患。通过科学系统的检测手段,能够有效预防工程事故、延长使用寿命,同时满足行业标准和法规要求。
钢材检测项目
钢材检测主要包括以下内容:
1. 化学成分分析:通过光谱仪或化学滴定法检测碳、硅、锰、硫、磷等元素的含量,确保符合牌号标准(如Q235、Q345等);
2. 力学性能测试:拉伸试验测定抗拉强度、屈服强度及延伸率,冲击试验评估低温韧性,硬度测试反映材料耐磨性;
3. 金相组织分析:利用显微镜观察晶粒度、夹杂物分布及热处理效果;
4. 缺陷检测:采用超声波探伤(UT)或磁粉探伤(MT)探测内部裂纹、分层等缺陷。
构件检测项目
构件检测需关注加工与安装质量:
1. 几何尺寸检测:使用卡尺、激光扫描仪校验长度、厚度、角度及形位公差;
2. 表面质量检查:目视或渗透探伤(PT)识别锈蚀、划痕、焊接飞溅等表面问题;
3. 组装精度验证:通过三维坐标测量仪检测构件间的配合间隙与对位偏差;
4. 无损检测(NDT):对关键承力部位进行X射线探伤(RT)或相控阵超声检测(PAUT)。
焊缝检测项目
焊缝质量直接决定连接可靠性,检测重点包括:
1. 外观检查:检查焊缝余高、咬边、焊瘤及表面裂纹;
2. 无损检测:
• 射线检测(RT)探查内部气孔、夹渣;
• 超声波检测(UT)定位未熔合或裂纹深度;
• 磁粉检测(MT)或渗透检测(PT)发现表面开口缺陷;
3. 破坏性试验:抽样进行弯曲试验、宏观金相分析及硬度测试;
4. 工艺评定:核查焊接参数(电流、电压、速度)是否符合工艺规程。
检测标准与技术创新
检测需依据GB/T 11345、ASME Section V、ISO 5817等国内外标准执行。近年来,数字化技术如工业CT扫描、TOFD衍射时差法及智能机器人检测系统的应用,显著提升了检测精度与效率。通过多维度数据融合分析,可实现缺陷的智能评级与寿命预测,推动钢结构工程向更高安全等级发展。
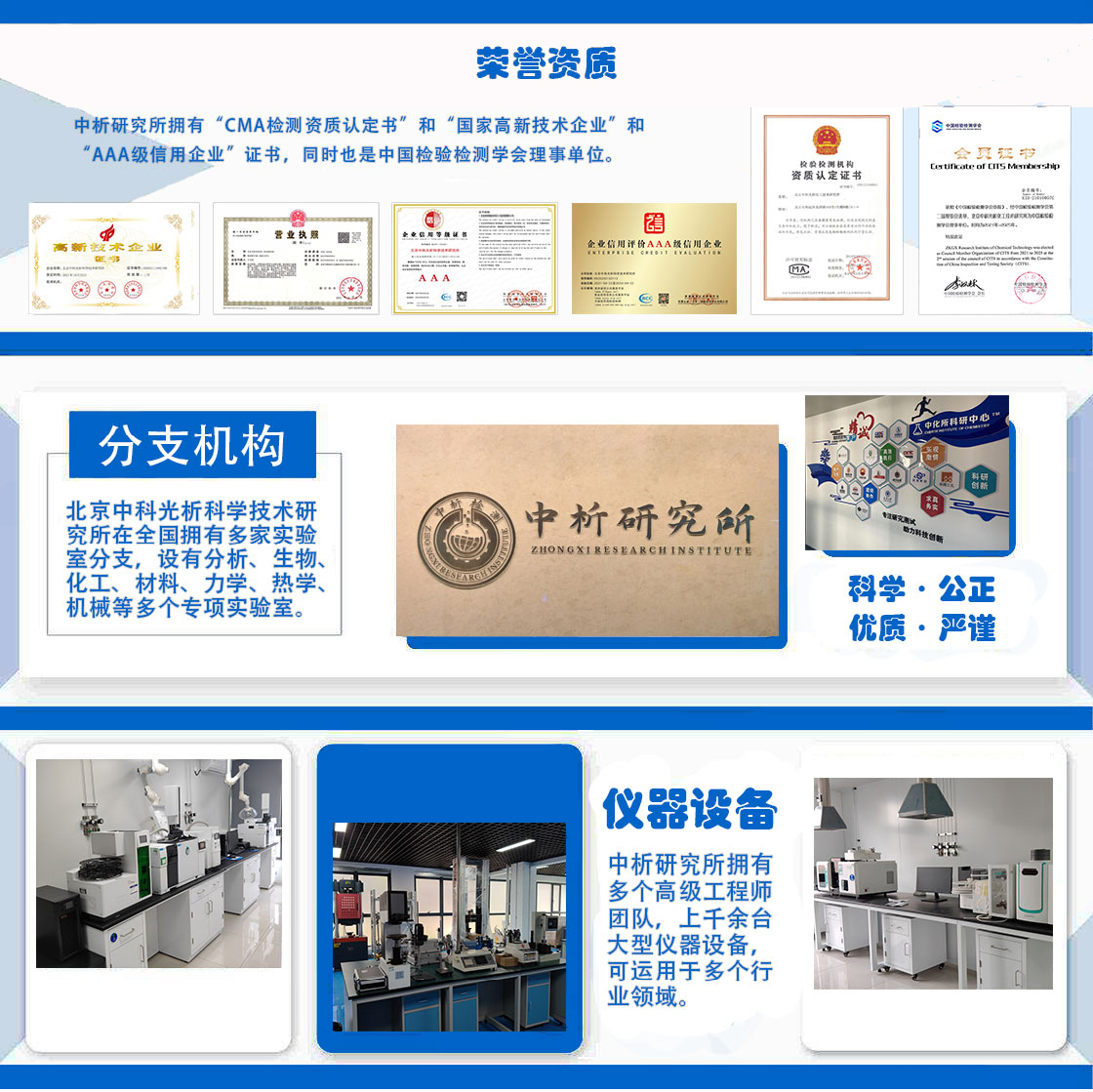
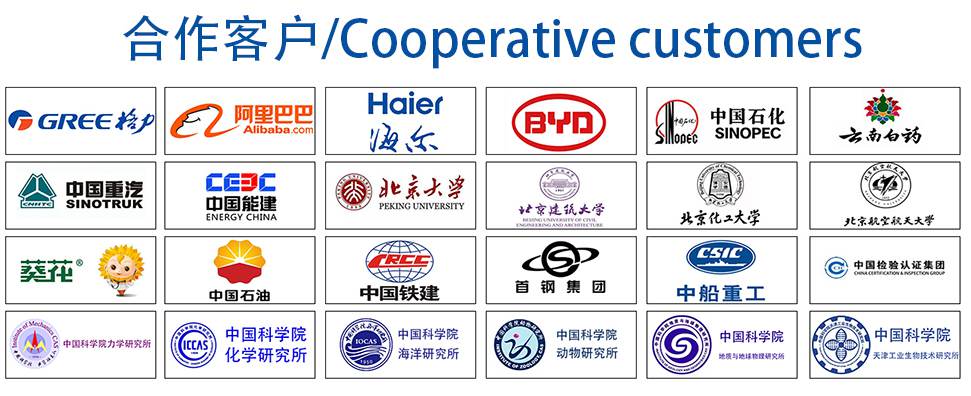